Case Study

ABB
See how the implementation of our solution has impacted the results achieved by ABB.

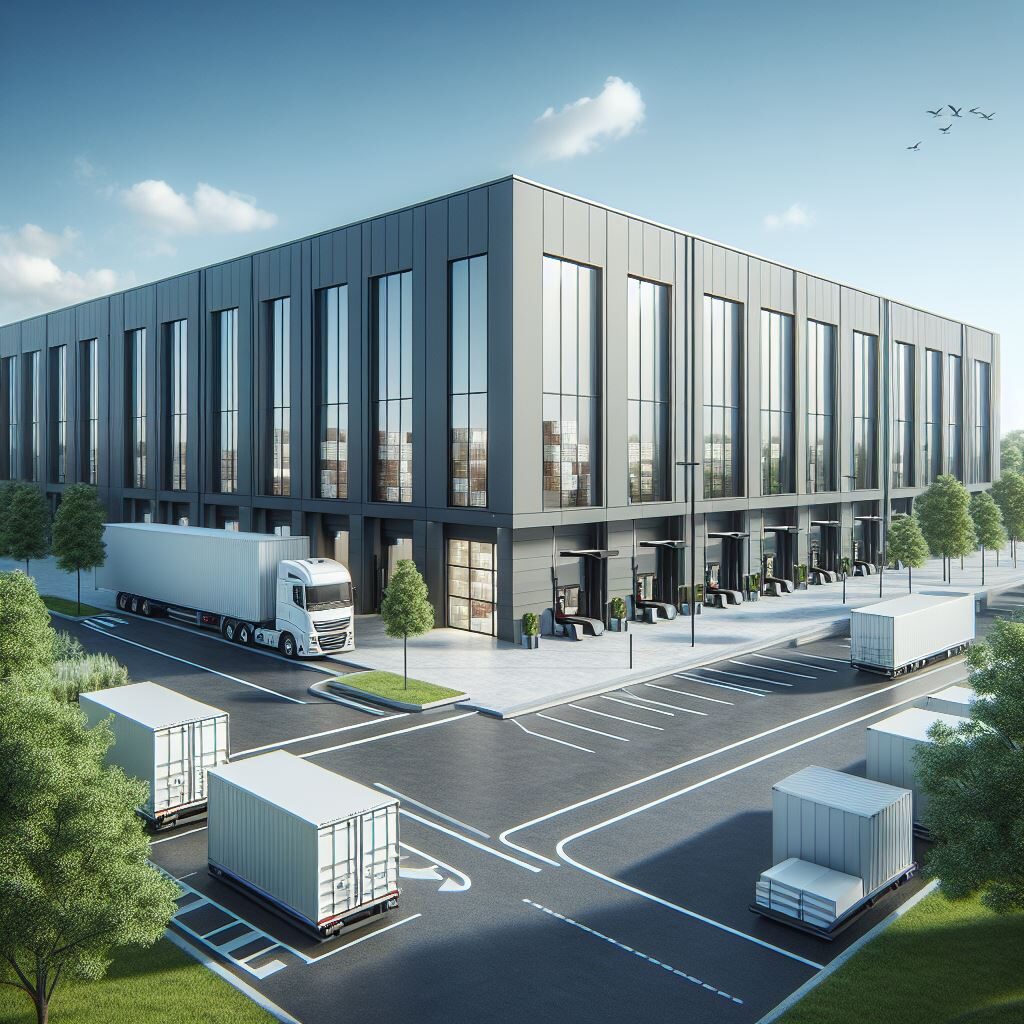
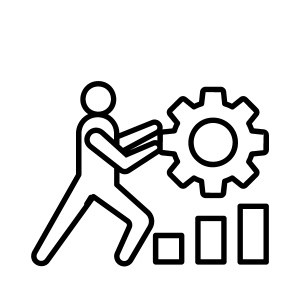
Challenge
Cost reduction
Improvement of organization
Insight into processes
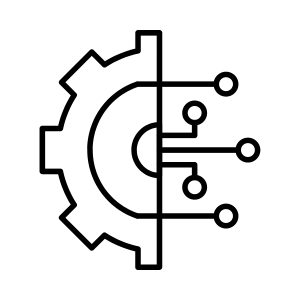
Transformation
Partnership with SIGNALO involving the implementation of the Forkfleet system.
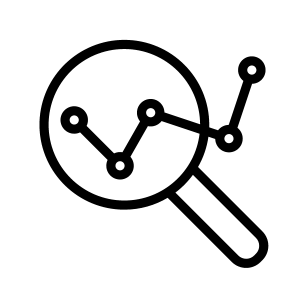
Results
Increase in productivity
Optimizing the use of resources
Cost reduction

Challenge

The challenge, in this case, was the effective management of the forklift fleet and operators in the factory. In the existing situation, there were many forklifts and operators, which caused certain difficulties related to suboptimal use of resources and insufficiently effective work organization.

Transformation

This system has brought several benefits that significantly impacted the efficiency and profitability of the factory’s operations
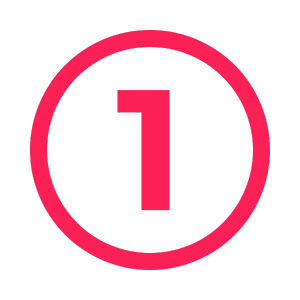
Reduction in the need for forklift operators
Before implementing the forklift management system, the ABB factory had to employ a significant number of forklift operators. Thanks to the new system, it became possible to automate many processes, significantly reducing the need for forklift operators. As a result, the company could save significant costs associated with employee salaries and benefits.
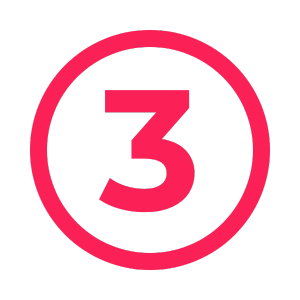
Shortening order processing times
The new system allows for precise monitoring and tracking of the movement of materials and products within the factory. This enables the optimization of routes and movement times, resulting in shorter order processing times. Shorter processing times mean faster order fulfillment, which contributes to increased customer satisfaction and the company’s competitiveness.
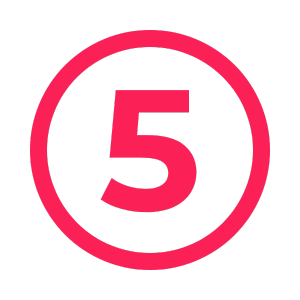
Data-driven decision-making
The forklift management system collects important data about operations within the factory. With advanced analytical tools, the company can now make more informed decisions. Data analysis helps identify areas that require optimization and prevent of wasting, which is according for the company’s long-term strategy.
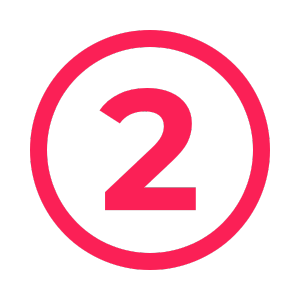
Reduction in the need for forklifts
Through process optimization and automation of operations using the forklift management system, the company was able to significantly reduce the number of required forklifts. This, in turn, translates into a reduction in the costs of purchasing, maintaining, and servicing these vehicles. Fewer forklifts also mean a safer and more organized working environment.
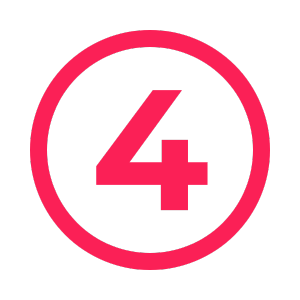
Control over intralogistics orders
The forklift management system enables more complex and precise planning of routes and internal operations within the factory. This allows the company to have better control over intralogistics processes, preventing delays and errors in the delivery of raw materials and components.

Results

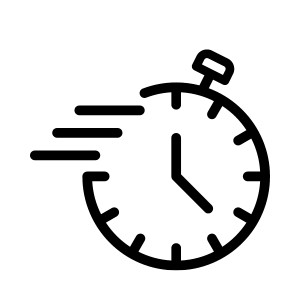
Time reduction
Distribution of orders
Service calls
Performing tasks
Process analysis
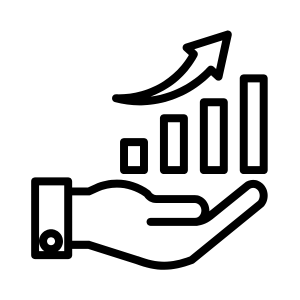
Growth
Performance
Situational orientation
Resource utilization
The introduction of the forklift management system at the ABB factory in Bielsko-Biała (Poland) has brought significant benefits, both in terms of operational efficiency and economics. The reduction in the need for forklift operators and forklifts, shorter order processing times, better control over intralogistics, and the ability to make data-driven decisions have significantly improved the company’s competitiveness and profitability. This is an example of how our technology and solutions can innovate processes and deliver tangible benefits. Such implementation we have already a lot. We can reduce cost at your place also. Don’t wait and use your chance to optimization by contact with us.
Values
Discover the benefits of collaboration

We offer a free consultation as the first step of collaboration, allowing you to familiarize yourself with our approach and verify our advisory competencies.
☛ This way, even before making a decision, you’ll feel that your situation and problem have been well understood, and the proposed solution will be optimally tailored to your company’s situation.
Our services (support) are included in a subscription, which does not generate hidden costs.
☛ The subscription-based billing allows for a significant reduction in the entry threshold into the system and enables immediate testing.
We are communicationally independent – we can develop our system without depending on the client’s IT department.
☛ We do not generate additional work for the client’s IT department. This way, we lower the implementation risk and associated costs.
The possibility of quicker implementation of the solution results in faster return on investment.
Login to our applications is secured at a high level, characteristic of banking solutions.
☛ At the same time, the login process is intuitive. Your data is as secure as in a bank thanks to our system.
We offer multilingualism in our solutions through real-time translation—each employee operates applications in their native language.
☛ This enhances efficiency and reduces costs by expanding the potential labor market and eliminating the need to hire translators.
Our software features an interface optimized for quick, easy, and intuitive use, even by digitally excluded or poorly skilled employees.
☛ This means real-time savings in both time and training costs for your workforce in using the new software.
The ability for rapid deployment of software for use results in a shorter transition/implementation period.
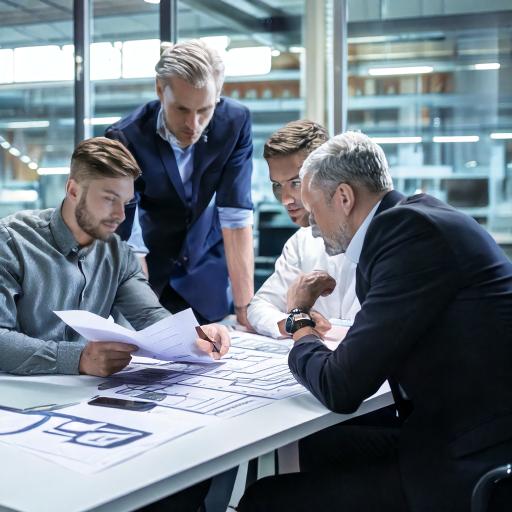
Seize the opportunity!
Order Free Consultation
Find out how you can take advantage

Don’t waste time on ineffective solutions! Take advantage of our free consultation and see how our software can increase your company’s efficiency.
☛ Reserve your free consultation now and accelerate the development of your business!
Innovative companies from around the world have trusted us
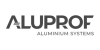
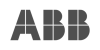
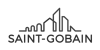
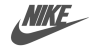
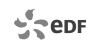
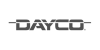
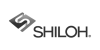
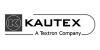
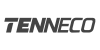
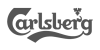
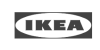