CASE STUDY

TENNECO
Take a look at how the implementation of our IT systems has impacted the results achieved by Tenneco.
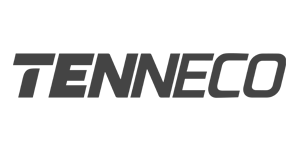
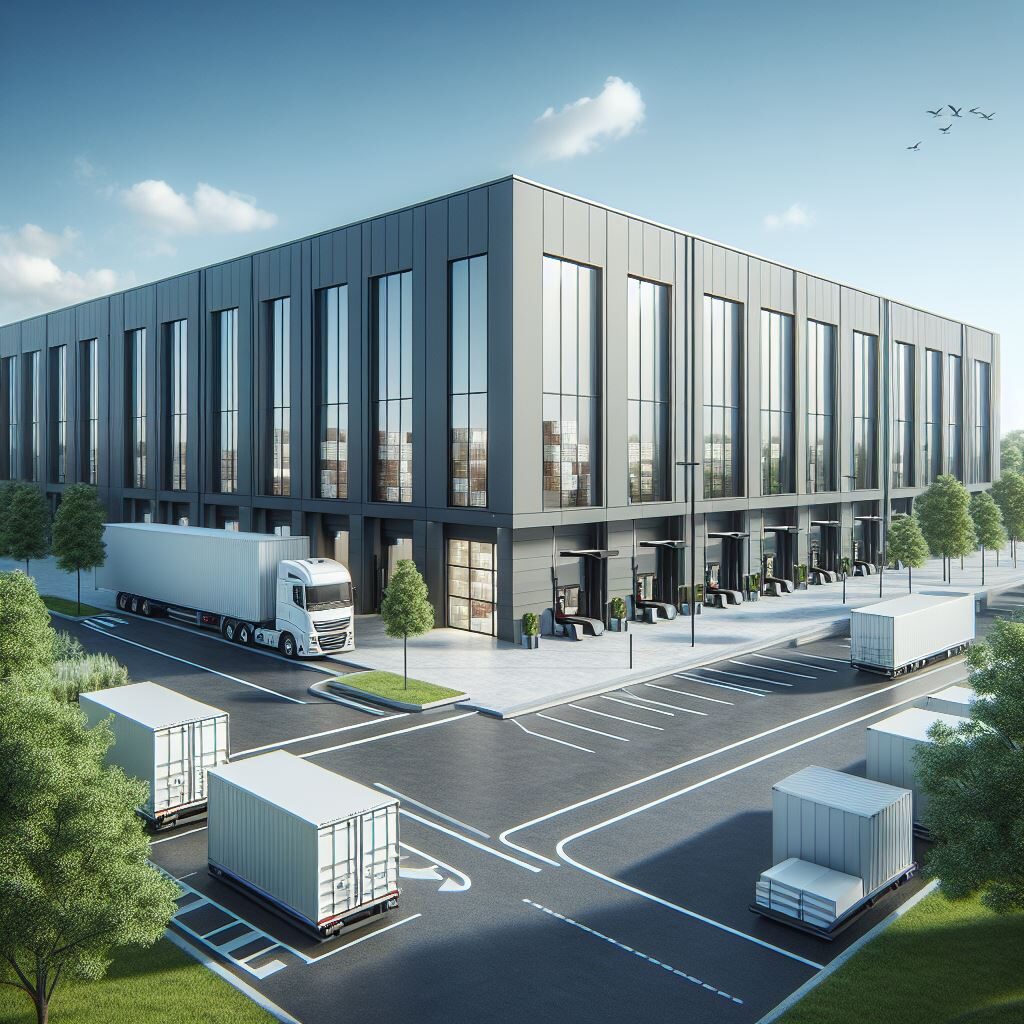
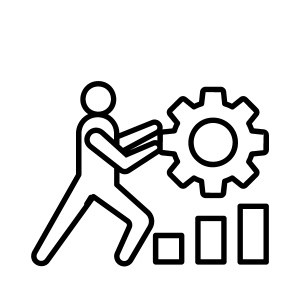
Challenge
Cost reduction,
Improvement of communication
Leveling of production losses
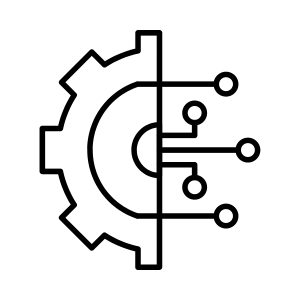
Transformation
Partnership with SIGNALO involving the implementation of a number of our systems.
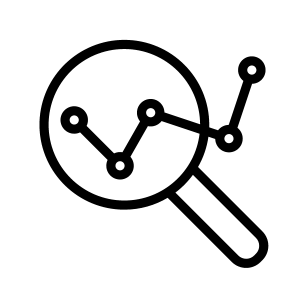
Results
Increase in productivity
Optimizing the use of resources
Cost reduction

Challenge

Resource management
To maintain its position as one of the leaders in the automotive industry, TENNECO must provide an optimized work environment in which people, equipment and technology work together seamlessly.
☛ Employees rely on properly managed and maintained equipment to achieve their production goals, so efficient resource management is a top priority for the company. Previously, TENNECO used various point solutions.
Efficiency
The result was inefficient and inconsistent processes that made it difficult for teams to ensure that resources were used and maintained in the most cost-effective, compliant and productive way.
Productivity
TENNECO wanted to adopt a more simplified and integrated approach to production management, maintenance and intralogistics.
☛ This would ensure better visibility and control of resources and would enable TENNECO to maintain very high standards in the functioning of the production process.

Transformation

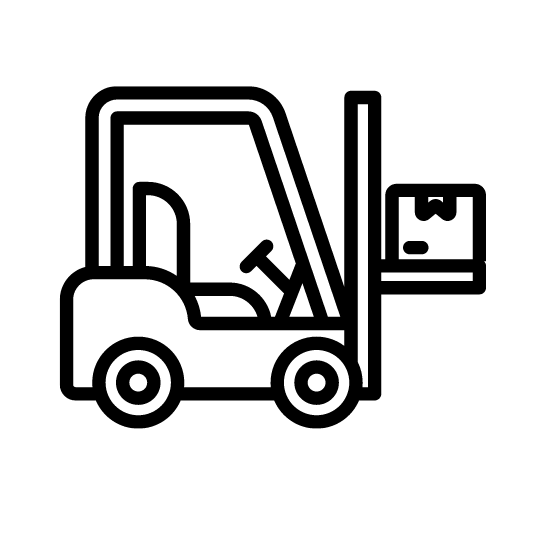
Based on the demonstrated needs, SIGNALO configured proprietary systems FORKFLEET and SKILLSMATRIX, and provided communication equipment (station tablets, trolley tablets, information boards).
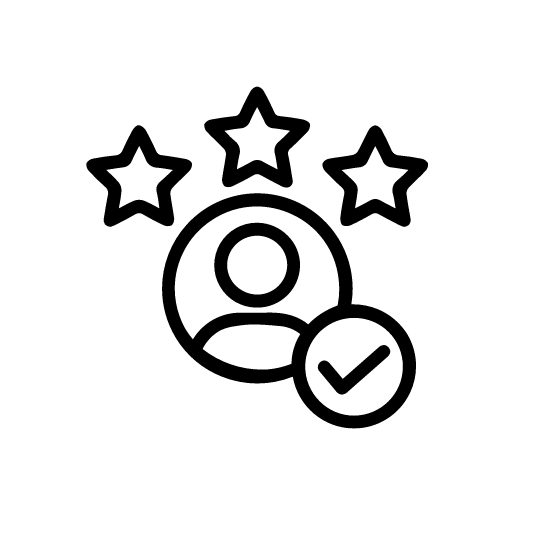
As a result, leaders and employees gained access to real-time data on breakdowns and calls, which allowed to reduce the times of intralogistics deliveries, intervention of leaders and the maintenance department.
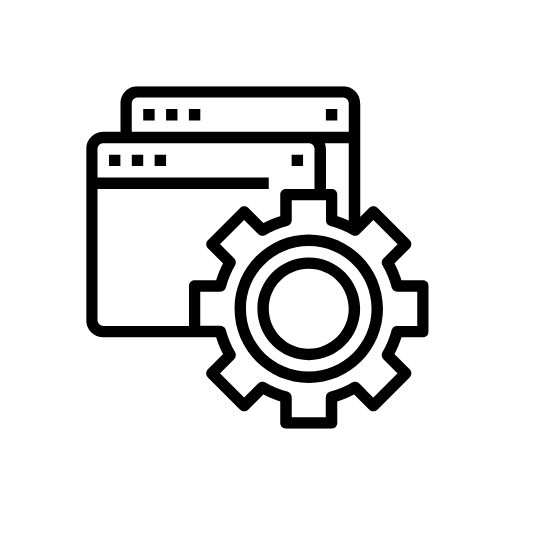
SIGNALO has also configured appropriate, web-accessible administration panels with advanced reporting functionalities that help to make optimization decisions.
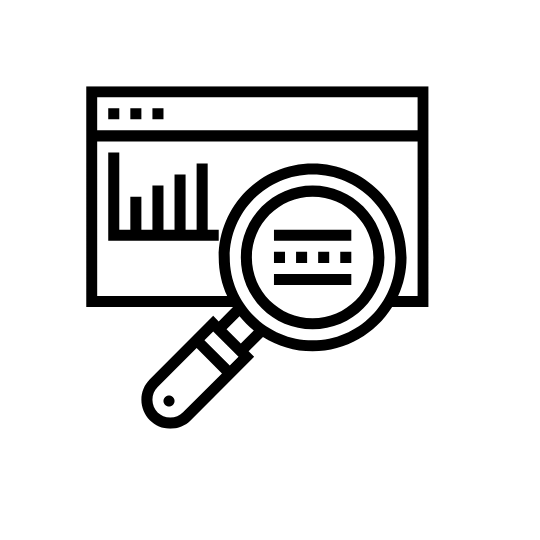
SKILLSMATRIX allowed for the ongoing monitoring of employees’ skills, training planning and machine staffing.

Results

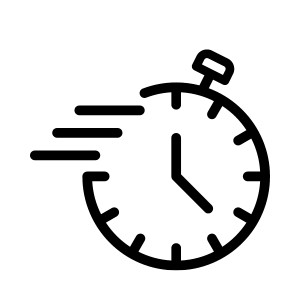
Time reduction
Machine downtime
Service calls
Implementation of deliveries
Error detection
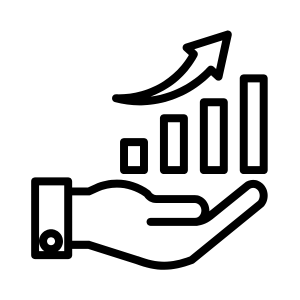
Growth
Performance
Situational orientation
Awareness of the problems
☛ TENNECO improved the visibility and control of the company’s assets, helping teams work more efficiently. From one point of control, people can see exactly what crashes are happening, where they occur and how long it takes to fix them. Employees receive clear messages regarding current tasks and their progress is monitored and assessed on the basis of substantive guidelines.
☛ Comprehensive process tracking and reliable metrics enable teams to make more informed decisions about maintenance planning, service delivery, budgets, hiring, and more.
☛ For example, when it comes to work orders, supervisors can now see how many work orders are open, which orders are currently being processed, queued or viewed, and so on. They can also view indicators such as the time it takes to execute different types of work orders, whether there are areas where certain orders are delayed, or whether more orders are processed during certain times of the year.
☛ With this type of insight, the company’s management team can more easily identify areas for improvement, make better use of existing resources, and more accurately forecast future demand.
Values
Discover the benefits of collaboration

We offer a free consultation as the first step of collaboration, allowing you to familiarize yourself with our approach and verify our advisory competencies.
☛ This way, even before making a decision, you’ll feel that your situation and problem have been well understood, and the proposed solution will be optimally tailored to your company’s situation.
Our services (support) are included in a subscription, which does not generate hidden costs.
☛ The subscription-based billing allows for a significant reduction in the entry threshold into the system and enables immediate testing.
We are communicationally independent – we can develop our system without depending on the client’s IT department.
☛ We do not generate additional work for the client’s IT department. This way, we lower the implementation risk and associated costs.
The possibility of quicker implementation of the solution results in faster return on investment.
Login to our applications is secured at a high level, characteristic of banking solutions.
☛ At the same time, the login process is intuitive. Your data is as secure as in a bank thanks to our system.
We offer multilingualism in our solutions through real-time translation—each employee operates applications in their native language.
☛ This enhances efficiency and reduces costs by expanding the potential labor market and eliminating the need to hire translators.
Our software features an interface optimized for quick, easy, and intuitive use, even by digitally excluded or poorly skilled employees.
☛ This means real-time savings in both time and training costs for your workforce in using the new software.
The ability for rapid deployment of software for use results in a shorter transition/implementation period.
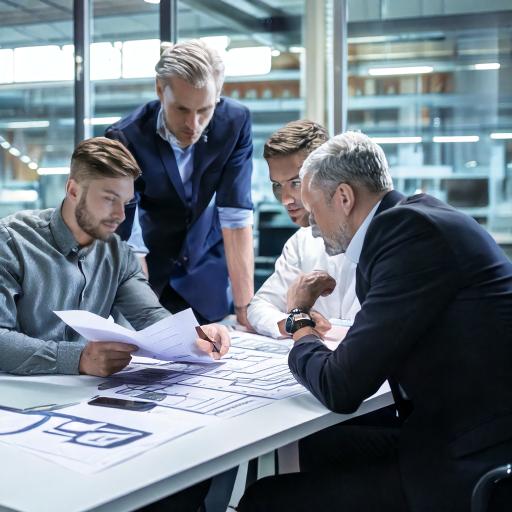
Seize the opportunity!
Order Free Consultation
Find out how you can take advantage

Don’t waste time on ineffective solutions! Take advantage of our free consultation and see how our software can increase your company’s efficiency.
☛ Reserve your free consultation now and accelerate the development of your business!
Innovative companies from around the world have trusted us
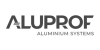
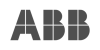
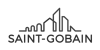
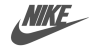
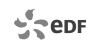
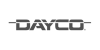
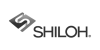
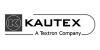
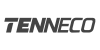
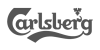
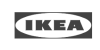
Free consultation
We create software and automation systems used in various sectors of the economy. Our systems are successfully used by manufacturing companies, logistics centers and warehouses.
☛ If you want to introduce a reliable system in your company and improve the processes happening in it, we encourage you to take advantage of a free consultation.
- Quick response to your message
- We take an individual approach to each customer
- The consultation is completely free
- Our consultants are well trained
Make an appointment
We will provide you with a personalized quote and discuss all the opportunities Singalo offers