- SCOR (Supply-Chain Operations Reference-model) is a supply chain operations model approved by the US Supply-Chain Council. It is a standard, cross-industry diagnostic tool for supply chain management. It is used for assessing, optimizing, and monitoring supply chain processes.
- However, in simplest terms, it can be described as a plan that supports the situation where products such as food, toys, or clothing are delivered to stores or homes in a timely manner and desired quality.
- The original structure of the SCOR model has been verified with leading companies in the industry, such as Intel, IBM, Rockwell Semiconductor, and Procter and Gamble.
- The model can be used to describe supply chains that are very simple or very complex, using a common set of definitions. As a result, different industries can be combined to describe the depth and breadth of almost any supply chain.
Example of operation based on SCOR
An example of this model in action could be a car manufacturer looking to optimize its supply chain operations for various markets:
- Under the SCOR model, a car manufacturer can identify areas where there is room for improvement in efficiency. For example, they may notice that the time between a customer ordering a car and its delivery is too long. To address this, the manufacturer can implement several changes in their delivery process.
- For instance, they can choose to enhance order and delivery status tracking using advanced computer systems. This will help in better monitoring and managing each stage of the delivery process.
- The manufacturer can also introduce better warehouse management to reduce the waiting time for availability of car parts, thus enabling faster order fulfillment.
- Additionally, they can take actions to streamline the production processes themselves, such as car assembly. They can implement automation or upgrade the production line to reduce the time required for producing one car.
All of these actions are consistent with the SCOR model, as they focus on optimizing the supply process to improve efficiency. As a result, the manufacturer can shorten the car delivery time to the customer, leading to increased customer satisfaction and greater competitiveness in the market.
What is the SCOR model?
Scalable
The SCOR model is flexible and scalable, allowing for adaptation to various business requirements and situations.
Practical
The SCOR model is easy to implement and apply in practice.
Preventive
The SCOR model enables proactive resource management, providing full control over processes and utilizing all tools and techniques to maximize efficiency.
Forward-looking
The SCOR model allows for the creation of long-term strategies that are tailored to current market conditions and facilitate better preparation for the future.
Transparent
The SCOR model facilitates quick conclusion drawing and implementing changes through clear and transparent definition of processes and metrics.
The 6 main SCOR processes
Planning
Planning involves determining the quantity of products that need to be delivered and planning how and when they will reach the customer. This process involves creating plans for product demand, procurement, and distribution. To optimize this process, it is important to collect and analyze data on demand, forecast sales trends, and use a customer relationship management (CRM) system.
Procurement
Procurement involves finding and ordering necessary materials, raw materials, and parts for production. This stage includes all activities related to order fulfillment, such as preparing goods, packaging, and shipping. To optimize the process, it is beneficial to use technologies that automate warehouses and shipment tracking systems. Additionally, proper storage of goods and efficient inventory management should be ensured.
Production
Production refers to the creation of a product using raw materials and tools. In this process, a company creates products according to specifications and demand. To optimize production, it is important to monitor machine performance, effectively manage working time, and continuously improve production processes. The use of modern technologies such as automation and robotics can significantly improve production efficiency.
Delivery
It includes the transportation and delivery of finished products from factories to warehouses, stores, or directly to customers. To optimize the distribution process, it is worth applying several practical guidelines:
- Plan ahead – Prepare a schedule and delivery plan to know when and what products are to be delivered. This will help avoid delays and errors.
- Utilize technology – Implement inventory management systems or software to track and trace shipments. This will facilitate monitoring of stock levels and flow of goods.
- Collaborate with suppliers – Build good relationships with suppliers to ensure timely and accurate deliveries. Communication is key.
- Invest in logistics – Focus on optimizing warehouse processes, such as product layout and space organization.
Well-organized warehouse will expedite the distribution process.
Return
This concerns the handling of returns when customers return damaged or unsatisfactory products. This process may include activities such as accepting returns, checking the condition of the product, and issuing refunds.
If you want to optimize the return process, it would be beneficial for you to apply a few practical tips:
- Simplify the return procedure – Ensure that customers have clear instructions regarding the return process and are informed about their rights. This will make the process quick and efficient.
- Evaluate reasons for returns – Analyze the causes of returns and complaints to identify any potential quality issues with products or services. This allows for implementing improvements and avoiding similar situations in the future.
- Focus on customer service – Give customers a sense of being heard and assure them that their issues are being resolved. Train staff to handle complaint situations and provide customer satisfaction.
- Monitor the process – Track the progress of the return process to know how long it takes and what costs are incurred. This will help identify areas for improvement.
Enablement
Processes describe actions related to supply chain management. They include, among others, business rule management, performance management, data management, resource management, object management, contract management, delivery management, supply chain network management, compliance management, risk management, and procurement management.
Benefits of implementing SCOR
Increasing supply chain management efficiency
SCOR supports supply chain management and helps organizations monitor, control, and improve their logistical processes.
Improving data quality
SCOR enables users to access reliable, consistent, and standardized data, significantly improving its credibility.
Cost reduction
SCOR allows organizations to reduce costs by optimizing supply chain processes, such as reducing inventory, increasing operational efficiency, and implementing monitoring and reporting systems.
Enhancing collaboration
SCOR enables companies to collaborate and exchange data through shared platforms, providing easier access to information and ultimately leading to stronger partnerships with business partners.
Supporting data analysis
SCOR relies on a strong analytical system that enables organizations to effectively analyze data related to supply chain processes. This allows organizations to better understand and improve their supply chains.
Where to start the implementation?
- The implementation of SCOR should start with selecting the appropriate implementation team. The team should consist of representatives from all participating companies in the process. Then, the scope and objectives of the implementation should be defined.
- Next, an implementation schedule should be developed, and all required resources should be determined.
- After selecting the suitable tools and applications for implementation, they should be tested and customized to fit the company’s individual needs.
- Before starting the SCOR implementation, training (APICS) should be conducted for all participants to ensure that all team members are fully aware of the intended goals and benefits of implementing this system.
- After the system is implemented, it should be monitored to ensure that all tasks have been completed according to the plan.
Which companies use SCOR?
SCOR (Supply Chain Operations Reference) is a supply chain management model that is used by many large companies, including Amazon, Walmart, Apple, Microsoft, and many others.
Who in the company is responsible for implementation?
The person responsible for implementing SCOR in a company is typically a business process management manager. They are responsible for understanding the company’s goals and values, developing an implementation plan, selecting the tools and technologies needed for implementation, implementing and monitoring the process.
IT systems supporting SCOR
Information systems supporting the SCOR (Supply Chain Operations Reference) methodology primarily focus on improving supply chain performance.
- They support organizations in the analysis, modeling, and optimization of supply chain processes.
- These systems encompass applications such as logistics optimization, supply chain planning systems, trade collaboration systems, and inventory management systems.
- The software typically offers many features, including asset tracking, order tracking, delivery monitoring, production planning, and process optimization.
- These systems can also offer supply chain visualization, data and report display, international collaboration, and many other functions.
All these functions help organizations improve their supply chain processes so that they can better cope with limited resources and ensure efficiency.
Important benefits of using IT systems in logistics
Shortening order fulfillment time
Information systems in logistics allow for the automation of the ordering and delivery process, which shortens the order fulfillment time.
Increasing efficiency
Information systems in logistics enable monitoring and optimization of logistics processes, which increases efficiency and productivity.
Facilitating inventory management
Information systems allow for tracking inventory levels and early detection of material shortages.
Improving service quality
Information systems in logistics enable accurate monitoring and control of service quality, which allows for delivering higher-quality products.
Cost savings
Information systems in logistics allow for the optimization of logistics processes, leading to cost reduction.
WE HELP OPTIMIZE PROCESSES
Our company specializes in delivering cost optimization solutions for production and warehousing to the market. Take advantage of our professional knowledge and experience. Contact us and we will advise you on how to reduce your company’s costs using proven IT systems. We have already helped many companies, including Tenneco, Dayco, ABB, Knauf, Saint-Gobain, and many others. Seize the opportunity and learn about the ways to implement cost-effective solutions quickly. Be the father of your company’s success!
HOW DO WE HELP?
SCOR is a supply chain management model that allows companies to optimize their business processes. Do you want to fully leverage the potential of this tool? Take advantage of the innovative IT solutions offered by Signalo.
- One of the main areas where Signalo can provide valuable IT solutions is in optimizing the operation of forklift fleets. With modern technologies and data analysis, Signalo enables better fleet management, route optimization, cost reduction, and improved resource utilization. This allows companies to achieve greater operational efficiency and increase profits.
- Another area where Signalo offers support is in improving communication between different departments within a company. With efficient communication solutions, Signalo enables smooth information flow and swift response to events requiring urgent intervention. This allows companies to make faster decisions and collaborate better within the organization.
- We also assist in better resource utilization. Our solutions increase efficiency within machine operations and optimize the utilization of human resources. This minimizes waste, reduces costs, and increases operational effectiveness.
- Signalo also provides a streamlined tool for collecting employee suggestions. Our modern platform allows for managing suggestions and rewarding employees for innovative ideas. As a result, companies can tap into the knowledge and creativity of their employees, often leading to significant improvements and innovations.
Values
Discover the benefits of collaboration
We offer a free consultation as the first step of collaboration, allowing you to familiarize yourself with our approach and verify our advisory competencies. This way, even before making a decision, you’ll feel that your situation and problem have been well understood, and the proposed solution will be optimally tailored to your company’s situation.
Our services (support) are included in a subscription, which does not generate hidden costs. The subscription-based billing allows for a significant reduction in the entry threshold into the system and enables immediate testing.
We are communicationally independent – we can develop our system without depending on the client’s IT department. We do not generate additional work for the client’s IT department. This way, we lower the implementation risk and associated costs. The possibility of quicker implementation of the solution results in faster return on investment.
Login to our applications is secured at a high level, characteristic of banking solutions. At the same time, the login process is intuitive. Your data is as secure as in a bank thanks to our system.
We offer multilingualism in our solutions through real-time translation—each employee operates applications in their native language. This enhances efficiency and reduces costs by expanding the potential labor market and eliminating the need to hire translators.
Our software features an interface optimized for quick, easy, and intuitive use, even by digitally excluded or poorly skilled employees. This means real-time savings in both time and training costs for your workforce in using the new software. The ability for rapid deployment of software for use results in a shorter transition/implementation period.
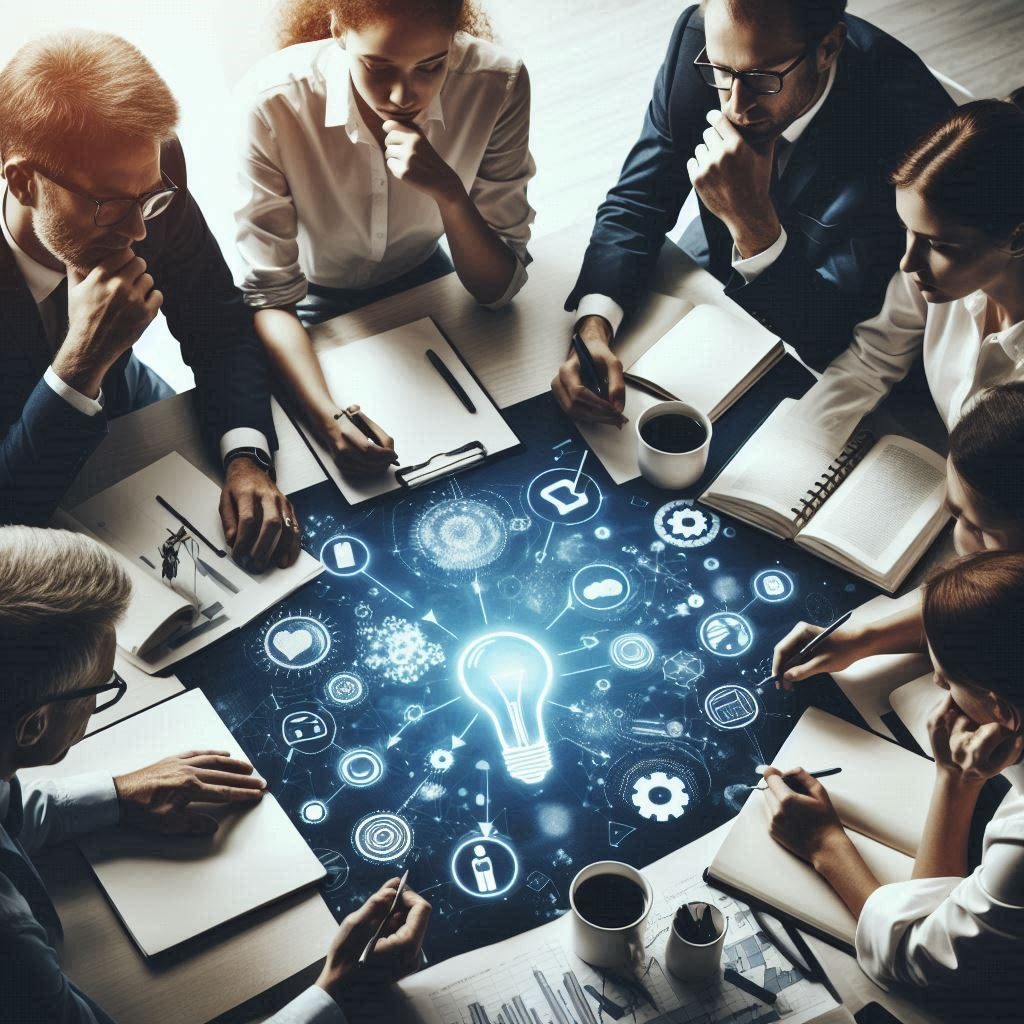