Data-Driven Decision
Harnessing the Power of Data-Driven Decision Making: A Game-Changer for Manufacturing Industry Leaders
In today’s rapidly changing business landscape, manufacturing industry leaders face numerous challenges, such as increasing global competition, evolving customer demands, and complex supply chain dynamics. To stay ahead in this highly competitive environment, making well-informed decisions is crucial. This is where data-driven decision making comes into play.
The Role of Data in Manufacturing
From production data to supply chain data and quality control data, every aspect of the manufacturing process contributes to the colossal volume of information available. This abundance of data has opened up new possibilities for manufacturing industry leaders to make informed decisions and drive their businesses forward.
Data generated in the manufacturing industry
The manufacturing industry operates on a scale that produces an unprecedented amount of data. Every step in the manufacturing process, from raw material acquisition to the final product’s delivery, generates immense volumes of information. Production data captures details about machine performance, downtime, cycle times, and output rates. Supply chain data records information about inventory levels, lead times, and supplier performance. Quality control data collects data on product defects, rejections, and customer complaints. All of this data together holds the potential to unlock valuable insights and improve business operations.
Traditional decision-making processes
Traditionally, decision-making in the manufacturing industry relied heavily on intuition, experience, and gut feelings. However, these traditional approaches had their limitations and were prone to errors. Without the support of data analysis, decision-makers lacked accurate and objective insights into their business operations. This resulted in a higher likelihood of making suboptimal decisions that could adversely affect productivity, efficiency, and profitability.
No analysis = no good decisions
Moreover, traditional decision-making processes often suffered from biases and subjective judgement. Decision-makers were influenced by personal beliefs, organizational pressures, and incomplete information. Without data-driven analysis, these decisions were at risk of being based on faulty assumptions or incomplete understanding of the true situation. This made it difficult to identify underlying problems, implement effective solutions, and achieve tangible results.
Wasting
Furthermore, the speed at which data is generated in the manufacturing industry often overwhelms traditional decision-making processes. Human capabilities alone are insufficient to process, analyze, and interpret the volumes of data being produced in real-time. This leads to delays in decision-making, missed opportunities, and an inability to respond swiftly to changing market dynamics.
Benefits of Data-Driven Decision Making
By analyzing vast amounts of data, manufacturers can gain valuable insights and make more informed decisions that drive operational efficiency, reduce costs, and improve overall productivity.
Operational Efficiency
Data analysis provides manufacturers with valuable insights into their operational processes, allowing them to identify bottlenecks and streamline workflows. By understanding where inefficiencies lie, manufacturers can make targeted improvements, optimizing resource allocation and minimizing downtime. For example, by analyzing machine performance data, manufacturers can pinpoint equipment issues and proactively address maintenance needs, reducing costly downtime and increasing overall productivity.
Predictive Analytics
Predictive analytics is another powerful tool enabled by data-driven decision making in the manufacturing industry. By leveraging historical and real-time data, manufacturers can anticipate maintenance needs and prevent equipment failures before they occur. This proactive approach not only reduces unplanned downtime but also improves overall productivity by ensuring that machinery is operating at its optimal level. By adopting predictive analytics, manufacturers can effectively allocate resources, schedule maintenance activities, and maximize uptime, which directly translates into increased productivity and reduced costs.
Inventory Management
Effective inventory management is crucial for manufacturers, as it impacts both cost control and customer satisfaction. Data-driven decision making allows manufacturers to accurately track inventory levels, analyze demand patterns, and identify trends. By having real-time data at their disposal, manufacturers can optimize inventory levels, reduce unnecessary stock, and avoid stockouts or overstock situations. This improved visibility into inventory management enhances cost control, reduces waste, and ensures that customer demands are met effectively and efficiently.
Agile Decision-Making
The manufacturing industry operates in a dynamic and ever-changing market environment. To stay competitive, manufacturers need to be agile and responsive to emerging trends and market dynamics. Data-driven decision making provides manufacturers with the necessary insights to make informed and agile decisions. By analyzing market data, consumer preferences, and internal operational metrics, manufacturers can identify emerging trends, adapt their strategies, and make timely decisions. This agility allows manufacturers to stay ahead of the curve, respond quickly to shifting demands, and capitalize on new opportunities.
Challenges and Solutions
- One of the major challenges faced by manufacturers when implementing data-driven decision making is concerns regarding data security. With the increasing amount of data being generated and utilized, ensuring its protection is of paramount importance. Manufacturers need to invest in robust cybersecurity measures to safeguard their sensitive data from potential threats. This may involve implementing end-to-end encryption, multi-factor authentication, regular security audits, and employee training programs to raise awareness about data security best practices.
- Another challenge lies in integrating various technologies and systems within the manufacturing environment. Many manufacturers often operate with legacy systems that were not designed to handle the large volumes of data generated in today’s digital age. To overcome this challenge, manufacturers should consider adopting user-friendly data analysis tools that can seamlessly integrate with different systems. These tools should enable easy data collection, analysis, and visualization, empowering decision-makers with real-time insights for better decision making.
Strategies to Overcome the Challenges
- To address data security concerns, manufacturers should prioritize cybersecurity as a fundamental aspect of their digital transformation journey. This involves investing in state-of-the-art cybersecurity solutions, partnering with industry-leading experts, and establishing comprehensive data protection policies. By adopting a proactive approach to data security, manufacturers can mitigate risks and build trust among stakeholders.
- In terms of technology integration, manufacturers should invest in modern data analysis tools that are compatible with existing systems. These tools should offer intuitive interfaces and provide seamless integration capabilities. Additionally, manufacturers should focus on providing adequate training and support to employees to ensure a smooth transition to these new technologies. Collaboration with technology vendors who specialize in data integration can also be beneficial in overcoming integration challenges.
The Future of Data-Driven Decision Making in Manufacturing
As we look into the future, it is evident that emerging technologies will continue to shape the landscape of data-driven decision making in manufacturing.
Machine learning
One such technology is machine learning. By leveraging algorithms and statistical models, machine learning enables manufacturers to extract valuable insights from vast amounts of data. These insights can then be used to make informed decisions about production schedules, quality control, and supply chain management. With machine learning, manufacturers can automate processes and identify patterns that may not be apparent to human decision-makers. This technology has the potential to revolutionize the manufacturing industry by improving efficiency, reducing costs, and increasing productivity.
Artificial intelligence (AI)
Another technology that holds significant promise for data-driven decision making in manufacturing is artificial intelligence (AI). AI systems can process and analyze data in real-time, enabling manufacturers to make proactive decisions based on up-to-date information. For example, AI-powered predictive maintenance can anticipate equipment failures and schedule maintenance activities accordingly, preventing costly downtime. Additionally, AI algorithms can optimize production schedules, taking into account various factors such as demand fluctuations and resource availability. By harnessing the power of AI, manufacturing organizations can streamline operations and ensure optimal use of resources.
Industrial Internet of Things (IIoT)
The Industrial Internet of Things (IoT) is yet another technology that is reshaping the future of data-driven decision making in manufacturing. With IIoT, machines, sensors, and devices are interconnected, generating a wealth of data that can be analyzed and utilized to drive decision making. For instance, in a smart factory equipped with IoT devices, manufacturers can monitor production lines in real-time and receive alerts when anomalies occur. This allows for immediate corrective action, minimizing defects and ensuring product quality. Moreover, IoT enables manufacturers to collect data throughout the production process, providing valuable insights for continuous improvement efforts.
Changes
While these technologies hold immense potential, their successful implementation requires more than just technical capabilities. It necessitates a cultural shift within manufacturing organizations – a shift towards a data-driven culture. This culture promotes the use of data in decision making at all levels of the organization, from top management to shop floor operators. It encourages employees to embrace data analysis and empowers them to make informed decisions based on data insights. By fostering a data-driven culture, manufacturing organizations can maximize the value derived from data, leading to improved operational efficiency, enhanced product quality, and increased customer satisfaction.
Real-Time Data Acquisition with Signalo’s Predictive Solutions
Signalo’s predictive solutions empower manufacturers to gather real-time data from various sources within their production environment. By connecting machines, sensors, and other devices through an IoT framework, Signalo ensures that every aspect of the manufacturing process is constantly monitored and analyzed. Through advanced machine learning algorithms, these solutions enable companies to identify patterns, anomalies, and potential bottlenecks in their operations, all in real-time.
One of the key strengths of Signalo’s predictive solutions is their versatility in data acquisition. Whether it’s temperature, pressure, vibration, or any other parameter that affects production quality and efficiency, Signalo’s solutions capture and analyze this information in real-time. This means that manufacturers can proactively identify and address issues before they escalate, minimizing downtime and maximizing productivity.
Huge experience
From automotive to pharmaceuticals, Signalo has a proven track record of driving operational excellence through data-driven decision making.
By leveraging Signalo’s expertise, manufacturers can unlock the full potential of their data and make informed decisions to enhance their production processes. With improved visibility into their operations and the ability to predict and prevent potential disruptions, companies can achieve higher levels of efficiency and cost savings.
Free consultation
To explore the possibilities of real-time data acquisition and learn more about how Signalo can support your specific manufacturing needs, we invite you to schedule a complimentary consultation. Signalo’s team of dedicated professionals will work closely with you to understand your goals and challenges, and present customized solutions tailored to your unique requirements. Don’t miss this opportunity to harness the power of data-driven decision making in your manufacturing operations.
Contact us today to schedule your free consultation and embark on a journey towards revolutionizing your manufacturing processes with Signalo’s predictive solutions. Together, we can unlock the true potential of your data and propel your company to new heights of success.
Values
Discover the benefits of collaboration
We offer a free consultation as the first step of collaboration, allowing you to familiarize yourself with our approach and verify our advisory competencies. This way, even before making a decision, you’ll feel that your situation and problem have been well understood, and the proposed solution will be optimally tailored to your company’s situation.
Our services (support) are included in a subscription, which does not generate hidden costs. The subscription-based billing allows for a significant reduction in the entry threshold into the system and enables immediate testing.
We are communicationally independent – we can develop our system without depending on the client’s IT department. We do not generate additional work for the client’s IT department. This way, we lower the implementation risk and associated costs. The possibility of quicker implementation of the solution results in faster return on investment.
Login to our applications is secured at a high level, characteristic of banking solutions. At the same time, the login process is intuitive. Your data is as secure as in a bank thanks to our system.
We offer multilingualism in our solutions through real-time translation—each employee operates applications in their native language. This enhances efficiency and reduces costs by expanding the potential labor market and eliminating the need to hire translators.
Our software features an interface optimized for quick, easy, and intuitive use, even by digitally excluded or poorly skilled employees. This means real-time savings in both time and training costs for your workforce in using the new software. The ability for rapid deployment of software for use results in a shorter transition/implementation period.
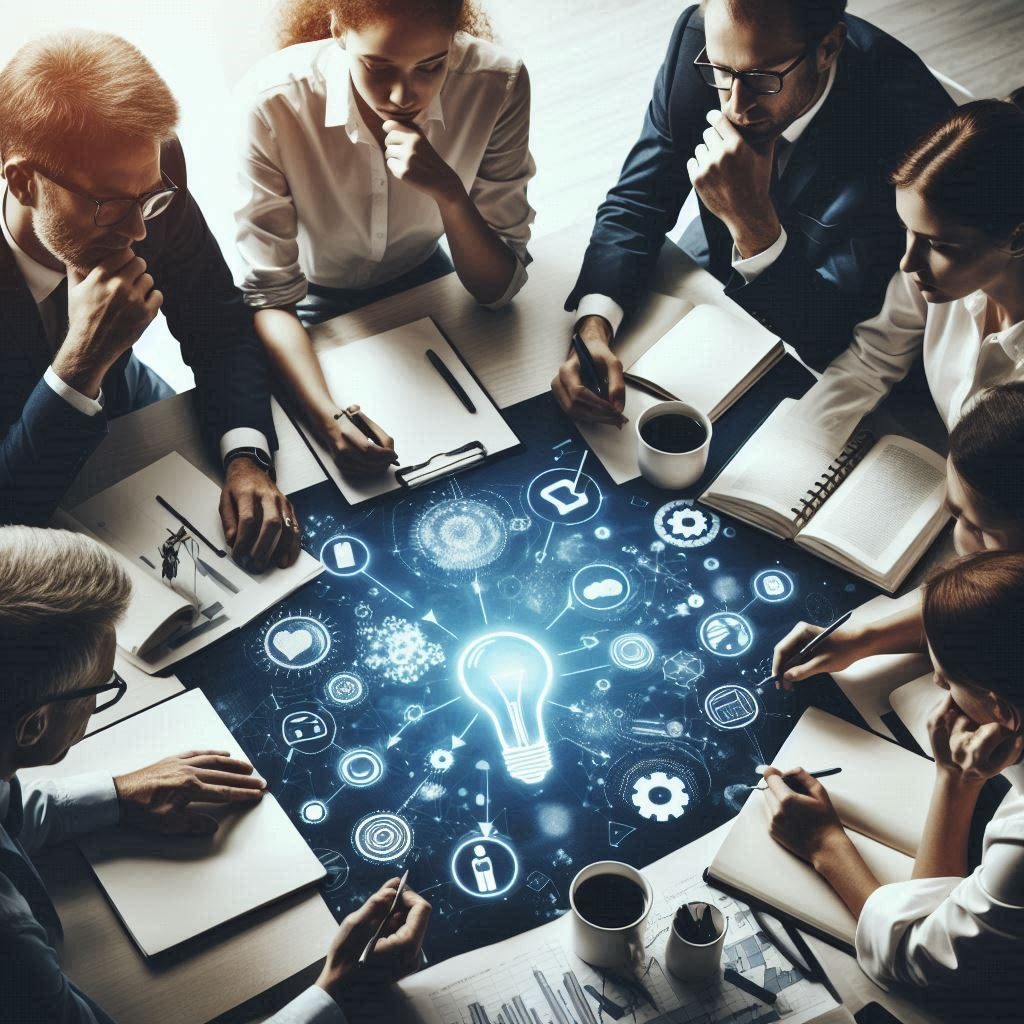