Kanban manufacturing is a workflow management method that originated in Japan. The word “kanban” literally means “visible card” or “signal.” In simple terms, the method is used to control the flow of materials and information in a production process.
Kanban manufacturing – how does it work?
At the center of the kanban is a visual kanban board. This is nothing more than a large board on which cards, called kanbans, are placed. Each kanban represents a specific job to be done, such as a task, product or component.
Kanban manufacturing – kanban board
A kanban board is divided into sections that reflect different stages of the production process. For example, if we have an assembly line, the board might have sections for the assembly, testing and packaging stages.
When a stage is ready to accept new tasks, workers take the appropriate kanbans from the “Done” section. They move the kanbans to their workstation and start doing the work. When they finish a given task, the kanban is placed in the appropriate section of the board, such as “Completed.”
The kanban board has several important functions:
- As a visual tool that allows the team to see what tasks are in progress, what delays are occurring and where the bottleneck may be. This allows them to react quickly to problems and make adjustments.
- The kanban board is a source of information about the status of production. Every employee can see on it what tasks are available, their priorities and quantities. This helps in planning and organizing work.
- It acts as a signaling system. When a kanban is moved from one section to another, it means that the stage is ready to accept new tasks. This is a signal to the previous stage to start producing new items.
Kanban manufacturing – benefits of use
Production kanban is a simple and effective way of managing production that allows you to better control the flow of materials and information. Here are some key aspects related to kanban and the benefits you can reap from it:
Reducing excess inventory
Kanban is based on “pull” production, that is, when there is actual demand. This avoids excess inventory and reduces costs associated with storage and maintenance.
Example: In an automobile factory, instead of stockpiling thousands of finished parts in warehouses, component production is initiated based on kanbans, which are pulled by workers when there is actual demand for a part.
Improving workflow
Kanban provides transparency and control over the production process. A visual kanban board shows what tasks are in progress, what delays are occurring and where the bottleneck may be. This allows the team to react quickly to problems and make adjustments.
Example: In an electronics manufacturing plant, the production team may see that the assembly of one of the components is delayed. They can take immediate action to fix the problem, such as supplying missing parts or shifting human resources to the appropriate position.
Continuous process improvement
Kanban enables workflow monitoring and analysis to identify areas for improvement. Production teams can focus on eliminating waste, optimizing sequences of operations and streamlining activities.
Example: In a textile production line, a team may notice that there are frequent delays in the shipment of raw materials. As a result of kanban analysis, they may conclude that suppliers should be more regular or that it is worth investing in larger raw material warehouses.
Kanban manufacturing – implementation steps
Understanding the production process
First of all, it is important to thoroughly understand the production process, the stages, resources and the relationships between them. This will help identify areas that can be optimized with kanban.
Selecting an area to implement kanban
We start by selecting one area where we want to implement kanban. This could be a production line, a specific stage of production or even a supply of materials.
Determine the elements of kanban
Next, it is necessary to determine what elements will be controlled by kanban. This can be a particular part, component or production task. Each element should have a corresponding kanban assigned to it.
Creating a kanban board
A visual kanban board is a key kanban tool. You can create it on a corkboard or use online tools. The board should show cells corresponding to each stage of production, with kanbans placed in the appropriate cells.
Employee training
It is important to train employees in kanban principles so that everyone understands how to use the kanban board, how to interpret kanbans and how to respond to signals.
Monitoring and improvement
After implementing kanban, monitor workflow, analyze results and respond to problems. Continually improve your processes, make improvements and adapt kanban to changing conditions.
Kanban manufacturing – examples of usage
An assembly line at a television factory
On the kanban board are kanbans representing various components, such as screens, cases, motherboards, etc. When a component is used, workers take the corresponding kanban and order the next supply. This allows for strict inventory control and avoids shortages or overstocking.
Furniture manufacturing
In a furniture manufacturing plant, kanbans can represent the various stages of production, such as woodworking, painting, assembly, etc. Workers take kanbans from the “Finished” section and move them to their stations, starting work. When a piece of furniture is ready, the kanban is placed in the “Made” section. This allows furniture to flow smoothly through the production process and quickly identify delays or problems.
Garment manufacturing
In a garment factory, kanbans can represent individual orders or models. On the kanban board, there are sections for different stages of production, such as cutting fabric, sewing, finishing, etc. Workers take kanbans from the “Finished” section and move them to the appropriate stations. When a stage is completed, the kanban is moved to the next section. This allows production progress to be monitored and any problems to be addressed.
Car production
In a car factory, kanban can be used at various levels, from the delivery of parts to the assembly of vehicles themselves. Kanban represents specific components, such as engines, brake systems or transmissions. When a component is needed for car assembly, the kanban is taken away and subsequent deliveries are ordered. This helps ensure a continuous flow of materials and minimizes the risk of shortages.
In these examples, kanban is used to control the flow of materials, manage inventory levels, minimize delays and improve production efficiency and flexibility. These are just a few applications of kanban, which can be adapted to the specifics of different industries and production processes.
Worth remembering
Production kanban is a simple but effective way to manage production. By reducing excess inventory, improving workflow and continuously improving processes, kanban contributes to a company’s efficiency and competitiveness. Kanban implementation begins with understanding the production process, selecting an area for implementation, defining kanban elements, creating a kanban board, training employees and monitoring and improving processes. If your company is focused on efficiency and flexibility, a manufacturing kanban can be an excellent tool that will bring tangible benefits.
Implementation support – using Signalo systems
We encourage you to contact Signalo, an expert in optimizing manufacturing processes. Our company specializes in the implementation of proprietary IT tools that help streamline business operations. Thanks to our vast experience and knowledge, we are able to customize solutions to meet the individual needs of organizations.
Our IT tools enable automation of processes, elimination of waste, optimization of workflows and close monitoring of efficiency. As a result, a company can achieve significant productivity gains, cost reductions and shorter production cycle times.
Signalo’s team consists of experienced specialists who are well versed in the needs of many industries and are able to provide solutions tailored to the specifics of each organization. Working with us, you will receive not only modern IT tools, but also support and advice at every stage of implementation.
If your company is focused on continuous development, efficiency and competitiveness, contact us today. Together we will develop a strategy for streamlining production processes that will allow you to achieve a higher level of production efficiency.
Values
Discover the benefits of collaboration
We offer a free consultation as the first step of collaboration, allowing you to familiarize yourself with our approach and verify our advisory competencies. This way, even before making a decision, you’ll feel that your situation and problem have been well understood, and the proposed solution will be optimally tailored to your company’s situation.
Our services (support) are included in a subscription, which does not generate hidden costs. The subscription-based billing allows for a significant reduction in the entry threshold into the system and enables immediate testing.
We are communicationally independent – we can develop our system without depending on the client’s IT department. We do not generate additional work for the client’s IT department. This way, we lower the implementation risk and associated costs. The possibility of quicker implementation of the solution results in faster return on investment.
Login to our applications is secured at a high level, characteristic of banking solutions. At the same time, the login process is intuitive. Your data is as secure as in a bank thanks to our system.
We offer multilingualism in our solutions through real-time translation—each employee operates applications in their native language. This enhances efficiency and reduces costs by expanding the potential labor market and eliminating the need to hire translators.
Our software features an interface optimized for quick, easy, and intuitive use, even by digitally excluded or poorly skilled employees. This means real-time savings in both time and training costs for your workforce in using the new software. The ability for rapid deployment of software for use results in a shorter transition/implementation period.
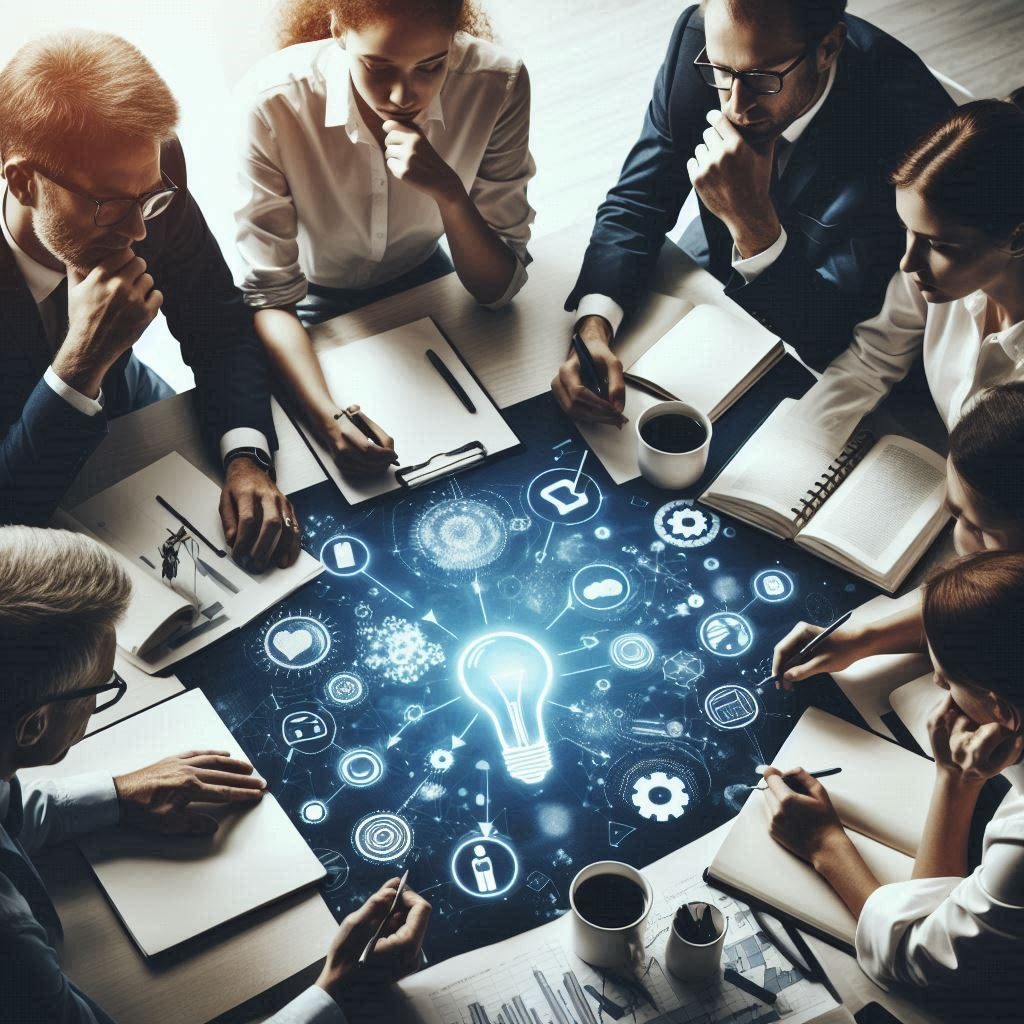