Continuous improvement, also known by the Japanese term “Kaizen,” refers to the process of continual enhancement of actions at all organizational levels. This term can be applied both personally and professionally, encompassing a wide range of activities—from daily routines to comprehensive business processes. The guiding idea is the belief that even the smallest, seemingly insignificant changes can eventually lead to significant benefits and improvements.
History
The history of continuous improvement dates back to the early 20th century, though its roots may be much deeper. It is primarily associated with the Japanese industry and management philosophy post-World War II. Kaizen, as a formal concept, was popularized by Masaaki Imai in the 1980s, but similar ideas to continuous improvement had been utilized earlier, for example, within Lean Management, aimed at eliminating all forms of waste.
Applications
Continuous improvement is crucial not only in production and management but also in education, healthcare, administration, and even in each individual’s personal life. At the organizational level, it promotes a culture of openness, collaboration, and continuous learning, resulting in increased efficiency, cost reduction, and improved work quality. In personal life, the principles of continuous improvement can aid in goal achievement, developing new skills, and better time management.
Key Principles of Continuous Improvement
Continuous improvement is based on several fundamental principles that can be applied in various contexts—from personal development to complex production processes in large organizations. Here’s an overview of the most important ones
Endless Iteration
Continuous improvement is based on the belief that there is always room for improvement. This process has no end and occurs through continuous iterations, where each subsequent attempt aims to surpass the previous one. In production, the iterative approach can involve regular reviews of assembly lines to identify areas for optimization.
Small Changes
In contrast to radical innovations, continuous improvement focuses on small, incremental changes that are easier to implement and entail lower risk. In the context of production, these could be minor modifications to processes or small changes in work organization, which together contribute to significant improvements.
Engagement of All Organizational Levels
Continuous improvement requires the engagement of all employees, from management to the production line workers. Each person has unique knowledge about their work, meaning improvement ideas can come from various levels. Promoting a culture of openness, where everyone can share their suggestions, is crucial.
Application in Production
Endless Iteration
In production, endless iteration can take the form of continuous monitoring and assessment of machine performance and process efficiency. Through regular data analysis, it’s possible to quickly identify areas needing attention and implement necessary changes.
Small Changes
Applying the principle of small changes in production can involve implementing simple improvements in work organization, such as rearranging tools, which makes access easier and shortens work time. These changes are often low-cost but can significantly impact productivity and quality.
Engagement of All Organizational Levels
In production, engaging employees at all levels can take the form of regular team meetings where employees can share observations and suggestions for improvements. Creating space for open communication and recognizing employees’ contributions to the improvement process motivates active participation and innovation. Specialized tools like Cluer can also be used for this purpose.
Note
Implementing these principles of continuous improvement in production processes can lead to significant benefits, including waste reduction, improved product quality, increased productivity, and higher employee satisfaction and engagement. However, the key to success lies in consistency and openness to change at all levels of the organization.
Process of Continuous Improvement
The process of continuous improvement, although it may seem complex, is based on a simple and iterative approach that can be applied in various fields and at different levels of operation. The central element of this process is the PDCA cycle (Plan-Do-Check-Act), which helps in systematically approaching the introduction and consolidation of changes.
Description of the Continuous Improvement Process (PDCA)
1. Plan
The first step is to identify the area requiring improvement and establish goals. In this phase, data is collected, processes are analyzed, and actions are planned to implement changes.
2. Do
Planned actions are implemented on a smaller scale, under controlled conditions, to minimize risk and better assess the effects.
3. Check
After implementing changes, an analysis of the effects is conducted, comparing results with expectations and goals defined in the planning phase. This is a crucial moment to assess whether the changes have yielded the desired results.
4. Act
Based on the results of the analysis, decisions are made regarding further actions. If the experiment was successful, changes are implemented on a larger scale. In the case of unsatisfactory results, the process returns to the planning phase to identify new improvement opportunities.
Tools and Methodologies Supporting the Process
- PDCA – As mentioned, the PDCA cycle forms the basis of the continuous improvement process, providing a structure for systematic changes and improvements.
- 5S – The 5S methodology (Sort, Systematize, Shine, Standardize, Sustain) is particularly useful in organizing the workspace and production processes, directly translating into efficiency and work quality.
- Six Sigma – The Six Sigma methodology focuses on reducing variability in production and business processes, aiming to minimize errors and waste through detailed data and process analysis.
Integration of Continuous Improvement with Daily Operations
Integrating continuous improvement with daily operations requires engagement at all levels of the organization and adaptation of the organizational culture that promotes innovation, openness to change, and continuous learning. It’s important for the process of continuous improvement not to be perceived as an additional burden but as an integral part of daily work contributing to better organizational functioning and employee satisfaction. In practice, this means regular training, openness to change suggestions from all employees, and incorporating continuous improvement principles into standard operating procedures.
Practical Implementation Strategies
- Start with employee training: Understanding the philosophy and tools of continuous improvement is foundational for all employees.
- Set clear goals: Clearly defined goals help focus efforts and track progress.
- Foster a culture of openness to change: Promote a culture where every employee feels responsible and empowered to suggest improvements.
- Utilize tools and methodologies for monitoring and analysis: Regularly apply PDCA, 5S, and Six Sigma to assess process effectiveness and implement necessary corrections.
- Encourage collaboration across departments: Integrate teams from different departments to exchange knowledge and experiences.
- Maintain motivation: Regularly recognize and reward employees for their contributions to the improvement process.
- Evaluate and adjust strategies: Continuously review the implementation strategies of continuous improvement to adapt to changing conditions and achievements.
Implementing continuous improvement in manufacturing companies is a process that requires engagement at all levels of the organization. Success depends on a clear vision, effective communication, continuous training, and employee engagement. Embracing these principles can yield significant benefits, including increased productivity, improved product and service quality, and building a stronger, more integrated organizational culture.
Challenges and Obstacles
Implementing continuous improvement in manufacturing companies, despite its numerous benefits, comes with various challenges and obstacles. Understanding and effectively managing them is crucial for maintaining the dynamics of the process and achieving sustainable results.
Typical Challenges:
- Resistance to change: Employees at different levels of the organization may be resistant to change, especially if they do not see direct benefits or fear additional work.
- Lack of understanding or training: Insufficient training and lack of understanding of the goals and methods of continuous improvement can lead to low engagement.
- Inadequate resources: Time, financial, or lack of appropriate tools constraints can hinder progress.
- Unclear goals: Lack of clearly defined, measurable goals can lead to scattered efforts and ineffective actions.
- Poor communication: Ineffective communication between teams and management levels can lead to misunderstandings and lack of coordination.
Scenarios Where Continuous Improvement May Not Yield Expected Results:
- Unrealistic expectations: Expecting too quick or too large results can lead to frustration and resignation from the process.
- Ignoring organizational culture: Disregarding the existing organizational culture and employee values can lead to resistance and sabotage of initiatives.
- Lack of leadership support: Lack of active support and engagement from leadership can weaken team efforts and limit resources.
Overcoming Obstacles and Sustaining Progress
- Building a Change-Ready Culture: Implementing a culture that celebrates innovation and is open to change is crucial. It’s also important to regularly train employees and provide them with access to necessary resources.
- Managing Expectations: Setting realistic goals and timelines, and regularly informing about progress and successes, helps maintain motivation.
- Engaging Employees: Involving employees at all levels in the decision-making process and encouraging participation in proposing changes increases their engagement and sense of ownership.
- Strong Leadership: Active support from leadership, both verbal and through resource allocation, is necessary to overcome resistance and maintain momentum.
- Communication and Collaboration: Improving communication within the organization and collaboration between departments helps overcome barriers and effectively achieve goals.
Overcoming challenges associated with continuous improvement requires patience, perseverance, and flexibility. It’s crucial to remember that this process is a marathon, not a sprint, and requires continuous commitment and readiness for adaptation and learning.
Successful Implementation Example at an Automotive Component Manufacturer
Context:
A renowned automotive component manufacturer noticed a decline in performance on one of its key production lines. Despite using modern technologies and having skilled personnel, there were issues with product quality and process inefficiencies.
Implemented Changes:
- The company decided to implement a continuous improvement program based on Lean methodology and tools such as 5S and Kaizen. The program began with a series of educational workshops for employees at all levels to raise awareness about the principles of continuous improvement and its benefits.
- Subsequently, multidisciplinary teams consisting of employees from various departments, including production, quality, and maintenance, started regular meetings to identify areas needing improvement and propose solutions. The PDCA (Plan-Do-Check-Act) tool was used for planning, testing, and implementing changes, with progress monitored using Key Performance Indicators (KPIs).
Results:
Within the first year of implementing the program, the company recorded significant improvements in key areas:
- Increased production line efficiency by 20% through waste elimination and process optimization.
- Improved product quality, resulting in a 30% reduction in customer complaints.
- Increased employee engagement and improved communication between departments.
Success Analysis:
The key success factors were the involvement of management, intensive employee training, effective communication throughout the organization, and a systematic approach to identifying and solving problems. The company confirmed that continuous improvement had become an integral part of its organizational culture, enabling ongoing process enhancement and competitiveness in the market.
Lessons from the Case Study
The case of the mentioned company demonstrates that effective implementation of continuous improvement requires more than just applying tools and techniques; crucial is the building of a change-ready culture, fostering collaboration between departments, and engaging and supporting at all levels of the organization. It also shows that a systematic approach to problem-solving can lead to significant improvements in efficiency and quality, benefiting both the company and its customers.
Tools and Resources
For manufacturing firms aiming to implement and maintain continuous improvement, various tools and resources are available. Their effective utilization can significantly expedite optimization processes and enhance quality.
Tools Supporting Continuous Improvement
Software
- Project management systems (e.g., Trello, Asana, Jira) aid in organizing tasks, deadlines, and team collaboration.
- Process analysis tools (e.g., Minitab, JMP) facilitate data collection, statistical analysis, and visualization, crucial in identifying areas for improvement.
- Quality management software (e.g., MasterControl, TrackWise) supports quality assurance processes and non-conformance management.
- Employee suggestion collection systems (e.g., Cluer).
Training
- Lean Six Sigma training offers various certification levels (Yellow Belt, Green Belt, Black Belt), educating employees on process optimization methods and tools.
- Kaizen workshops focus on the practical application of continuous improvement principles in the workplace.
- Online courses (e.g., on platforms like Coursera, Udemy) provide flexible access to continuous improvement knowledge, allowing learning pace adjustment to individual needs.
Books
- “Kaizen: The Key to Japan’s Competitive Success” by Masaaki Imai is a classic introduction to Japanese management and process improvement methods.
- “The Toyota Way” by Jeffrey K. Liker describes the 14 management principles at Toyota, forming the foundation of the Lean philosophy.
- “Lean Six Sigma For Dummies” by John Morgan and Martin Brenig-Jones offers an accessible introduction to Lean Six Sigma methodology, catering to a wide audience.
Online Resources and Places to Find More Information
Forums and Online Communities
- LinkedIn Groups such as Lean Six Sigma or Continuous Improvement serve as platforms for exchanging experiences and best practices.
- Reddit hosts subreddits dedicated to Lean, Six Sigma, and continuous improvement, where users share advice and resources.
Websites and Blogs
- iSixSigma.com offers articles, case studies, and discussion forums dedicated to various aspects of Six Sigma methodology.
- LeanEnterpriseInstitute.org provides resources on Lean implementation in organizations, including training, books, and case studies.
- ASQ.org (American Society for Quality) is a rich source of knowledge on quality management, offering articles, webinars, and training.
By leveraging these tools and resources, manufacturing firms can not only more effectively implement continuous improvement but also inspire employees towards innovation and striving for excellence in every aspect of their operations.
The Future of Continuous Improvement
Continuous improvement, already a fundamental part of many organizations’ strategies, will continue to evolve, adapting to a changing world and new technologies. In the future, we can expect these processes to become even more integrated with companies’ daily operations and increasingly supported by modern technologies.
How Continuous Improvement May Evolve in the Future
- Increased focus on data and analytics: As companies digitize their operations further, data will become an even more critical component of continuous improvement. Advanced analytics and machine learning may provide deeper insights into processes, enabling more effective identification of areas requiring improvement.
- Personalization of employee experiences: Technological advancements will allow for a more personalized approach to employee training and development, crucial for maintaining their engagement and innovation. VR (virtual reality) tools, for example, may enable simulations and training in a more interactive manner.
- Enhanced integration with sustainable development: Continuous improvement will increasingly consider ecological aspects and sustainable development. Focus on waste reduction and energy efficiency will become standard, not only for ethical reasons but also for economic ones.
Potential New Directions and Technologies Supporting Continuous Improvement
• Internet of Things (IoT) and smart factories: IoT devices can provide real-time data on manufacturing processes, enabling immediate detection and resolution of issues. Smart factories, leveraging IoT, artificial intelligence, and robotics, will be able to autonomously optimize processes in real-time.
• Artificial intelligence and machine learning: These technologies can automatically analyze vast amounts of operational data, identifying patterns and predicting potential issues before they occur. This allows for even faster and more accurate implementation of improvements.
• Blockchain: This technology has the potential to increase transparency and traceability in supply chains. In the context of continuous improvement, blockchain can assist in better monitoring and managing product quality and more efficient collaboration with business partners.
• Digital twins: Digital replicas of physical manufacturing systems can enable testing of changes in a safe, virtual environment. This allows for experimenting with different scenarios and optimizations without the risk of disrupting real processes.
As the world becomes increasingly connected and digital, continuous improvement will play an even greater role in maintaining competitiveness and innovation in companies. Integrating new technologies and approaches, such as personalization, sustainable development, and advanced analytics, will be crucial for future success in continuous improvement.
Continuous Improvement
Download Excel spreadsheet - Set goals, track status!
We encourage you to utilize the Excel template for planning and monitoring continuous improvement within your company!
This tool will facilitate tracking project progress, ensure better organization, and engage all team members. Download the file and see how it can streamline your production processes and enhance operational efficiency.
Values
Discover the benefits of collaboration
We offer a free consultation as the first step of collaboration, allowing you to familiarize yourself with our approach and verify our advisory competencies. This way, even before making a decision, you’ll feel that your situation and problem have been well understood, and the proposed solution will be optimally tailored to your company’s situation.
Our services (support) are included in a subscription, which does not generate hidden costs. The subscription-based billing allows for a significant reduction in the entry threshold into the system and enables immediate testing.
We are communicationally independent – we can develop our system without depending on the client’s IT department. We do not generate additional work for the client’s IT department. This way, we lower the implementation risk and associated costs. The possibility of quicker implementation of the solution results in faster return on investment.
Login to our applications is secured at a high level, characteristic of banking solutions. At the same time, the login process is intuitive. Your data is as secure as in a bank thanks to our system.
We offer multilingualism in our solutions through real-time translation—each employee operates applications in their native language. This enhances efficiency and reduces costs by expanding the potential labor market and eliminating the need to hire translators.
Our software features an interface optimized for quick, easy, and intuitive use, even by digitally excluded or poorly skilled employees. This means real-time savings in both time and training costs for your workforce in using the new software. The ability for rapid deployment of software for use results in a shorter transition/implementation period.
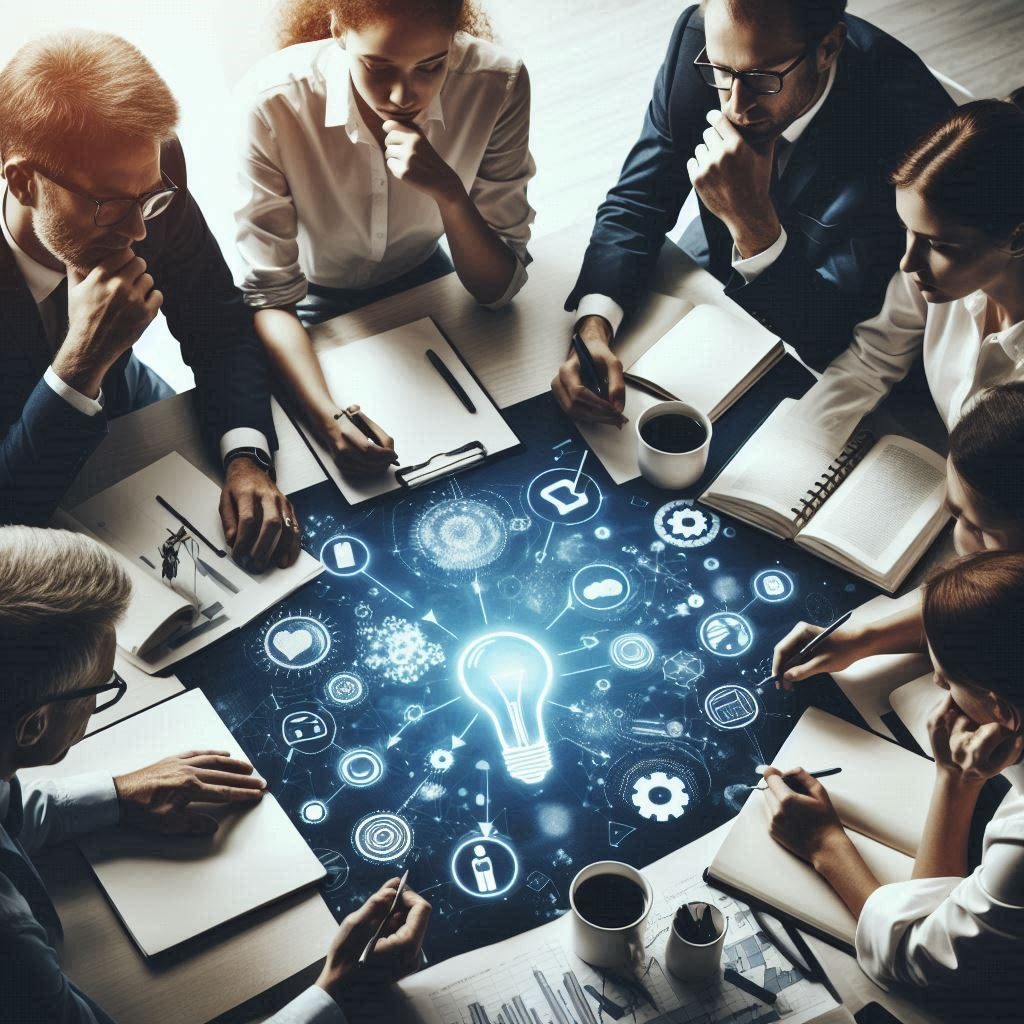