Six Sigma, as a quality management system, is an integral part of modern business. Since its inception in the 1980s, Six Sigma has gained significant popularity and is recognized as one of the most important tools for improving efficiency and reducing defects in business processes.
What is Six Sigma?
Six Sigma is a management approach that focuses on process improvement through the identification, analysis, and elimination of defects, errors, or variations. The goal of Six Sigma is to achieve the lowest possible level of standard deviation in processes.
The role of Six Sigma in improving efficiency
Six Sigma enables organizations to achieve high efficiency by eliminating waste, reducing operational costs, and increasing productivity. Through data analysis and statistics, Six Sigma allows for the identification of weak points in processes and the implementation of improvements that lead to operational excellence.
Reducing defects in processes
The main goal of Six Sigma is to reduce defects in business processes. Defects refer to any deviations from expected results that lead to imperfections, errors, or losses. Six Sigma enables organizations to identify the causes of defects and then implement corrective actions that minimize the risk of their occurrence in the future.
Methods and Tools of Six Sigma
Six Sigma is based on the application of various methods and tools that support the improvement process. One of the most popular tools used in Six Sigma is DMAIC (Define, Measure, Analyze, Improve, Control). DMAIC is a structured, five-stage process that enables organizations to effectively implement Six Sigma solutions.
History
Six Sigma was initiated in the 1980s by Motorola, which aimed to minimize errors and defects in its manufacturing processes. During this time, the company began working intensively on understanding and improving the quality of its products, which brought excellent results.
Evolution
After the successful implementation of Six Sigma at Motorola, other companies such as General Electric, Honeywell, and AlliedSignal also started adopting this methodology, contributing to its further development. Over time, Six Sigma evolved to become not only a quality control tool but also a comprehensive business approach.
Essence of Six Sigma as a set of tools and techniques
Minimization of Deviation from Norm
Six Sigma aims to minimize deviation from the norm at all stages of the production or service process. This is achieved through careful data analysis, identifying the main sources of problems, and eliminating them.
Elimination of Errors and Defects
A key concept of Six Sigma is the elimination of errors and defects that affect the quality of products or services. This method focuses on identifying the roots of problems and implementing appropriate actions to prevent the recurrence of flaws.
Benefits of implementing Six Sigma
Increased efficiency
Six Sigma allows for the identification and removal of barriers that lower process efficiency. Through the elimination of waste and optimization of operations, a company can achieve greater productivity and effectiveness.
Cost reduction
Eliminating defects and errors leads to a reduction in costs associated with complaints, repairs, and excess resources.
Improvement in customer satisfaction
Six Sigma enables companies to deliver products and services of higher quality. Satisfied customers are more loyal and likely to recommend products or services to others, leading to increased sales and strengthening of the company’s brand.
Key principles and methodology of Six Sigma – DMAIC
In this chapter, we will focus on the DMAIC method (Define, Measure, Analyze, Improve, Control), which is one of the most important techniques used in Six Sigma. It allows for step-by-step problem identification, measurement of parameters, data analysis, implementation of changes, and process control to achieve operational excellence.
Defining the Problem
The first stage of DMAIC is defining the problem. This is a crucial moment because precise identification of the problem will allow later focus on the right areas for improvement. In this stage, project goals and scope should be determined, as well as expected outcomes. It is also important to identify factors influencing the problem and its causes.
Measurement of Parameters
The next stage is measurement of parameters. During this stage, data is collected that will allow evaluation of the current state of the process. It is important to precisely define metrics that will measure process performance. It is also important to establish data sources and how they will be collected. Based on the gathered information, the effectiveness of the process can be assessed and areas in need of improvement can be identified.
Data Analysis
Data analysis is a crucial phase of DMAIC that allows understanding of the causes of problems. During this stage, various statistical tools are applied, such as histograms, cause-effect diagrams, or regression analysis. The goal is to identify the main factors influencing the problem and determine their relationships. Data analysis enables a better understanding of the process and the possibility of identifying optimal solutions.
Implementing Changes
After thorough data analysis, it is time to implement changes. During this stage, an action plan must be developed and implemented to eliminate problems and improve process performance. It is also important to involve employees who will be responsible for implementing the changes. Implementing changes may require restructuring the process and providing training to employees to equip them with the necessary skills for effective operation.
Process Control
The final stage of DMAIC is process control. After implementing changes, it is necessary to monitor and maintain the achieved results. Various tools, such as control charts or audits, are used during this stage. This allows for assessing the effectiveness of the implemented changes and preventing the recurrence of problems. If necessary, further improvements can also be introduced to increase process efficiency.
Examples of Six Sigma applications
Six Sigma can be effectively applied in various industries, from manufacturing to services. Here are a few specific examples:
- Automotive industry – Implementing Six Sigma in the production line has led to significant reduction in errors and defects, as well as improvement in the quality of cars.
- Telecommunications industry – Applying Six Sigma in the customer service area has resulted in reduced response time, elimination of recurring problems, and increased customer satisfaction.
- Medical services – Six Sigma has been successfully applied in healthcare, contributing to the reduction of medical errors, improvement in the quality of care, and shorter waiting times for procedures.
Tools and Techniques
In the previous chapters, we discussed the philosophy of Lean Six Sigma and its benefits. Now, we would like to present widely used tools and techniques that are integral parts of the Six Sigma methodology.
Risk analysis
It allows for the identification, assessment, and management of risks associated with production or service processes. This enables minimizing the chances of errors occurring and their impact on the organization’s performance.
Cause and effect diagrams
Ishikawa diagrams or fishbone diagrams are used to identify the causes of problems or defects. They visually represent complex relationships between various factors and causes, allowing focus on the most significant areas that have the greatest impact on quality.
Process mapping
Process mapping is a technique that enables a thorough understanding and identification of all steps and resources associated with a given process. It provides a clear visualization of how a process currently functions, allowing for the identification of areas for improvement. Process mapping is a key tool that helps eliminate waste and optimize process performance.
Data analysis
Allows for the collection, processing, and interpretation of data related to processes. Data analysis enables the identification of trends, patterns, and potential sources of defects. This tool enables fact-based decision-making and provides support in achieving established quality goals.
Design of experiments
It allows for the planning and execution of experiments necessary to assess the influence of individual factors on product or service quality. Design of experiments enables process optimization and the achievement of desired output parameters.
Measurement of effectiveness
To monitor progress and success in implementing Six Sigma, it is necessary to use appropriate indicators and measures. One of the most popular indicators is the DPMO (Defects Per Million Opportunities) ratio, which allows for the evaluation of process quality, defect analysis, and comparison of performance between different processes or areas of the organization. For process control and continuous improvement are used also quality indicators .
Six Sigma in production and services
The Six Sigma methodology can be applied in both manufacturing and service organizations. Regardless of the type of business, the goals and techniques of Six Sigma remain the same – minimizing defects, reducing waste, improving quality, and increasing efficiency.
Implementing – steps to success
Employee training
- A crucial aspect of introducing Six Sigma in a company is providing employees with the necessary knowledge and skills.
- Employees should be trained in both the theory of Six Sigma and the practical tools and techniques used in the methodology.
- Training should be tailored to different levels of involvement in Six Sigma projects so that each employee understands their role and tasks.
Appointment of Six Sigma leaders
- Every company implementing Six Sigma should have designated and qualified Six Sigma leaders.
- Six Sigma leaders are typically responsible for managing Six Sigma projects and coordinating the actions of project teams.
- They should possess both technical skills and leadership skills to effectively lead projects and motivate team members.
Development of action plans
- Implementing Six Sigma requires careful development of action plans that define the goals, scope, and schedule of Six Sigma projects.
- Planning should include identifying key processes that should be improved and determining expected results.
- Additionally, action plans should consider resource allocation, budgeting, and risk assessment.
Monitoring progress
- Effective implementation of Six Sigma requires regular monitoring of project progress and analysis of achieved results.
- Monitoring progress allows for identifying any delays, problems, or the need to make changes to action plans.
- Introducing appropriate tools and metrics allows for measuring progress and tracking achieved benefits.
We encourage you to take action!
Implementing Six Sigma can bring numerous benefits to a company, such as:
• Improving the quality of products
and services
• Increasing process efficiency
• Reducing operational costs
• Enhancing customer satisfaction by delivering products and services that meet their expectations
• Eliminating defects and errors in production processes
• Reducing process variability and minimizing risk
It is worth exploring the possibilities of implementing Six Sigma in your company. This methodology has the potential to significantly improve operational performance and competitiveness of the organization. Taking action in this direction can bring significant benefits for both the company and its customers. Don’t wait, start acting today!
Six Sigma
How to Avoid Mistakes During Implementation - PDF
Download your free mini-guide, designed specifically to help you avoid pitfalls related to implementation. Wishing you a pleasant and productive experience!
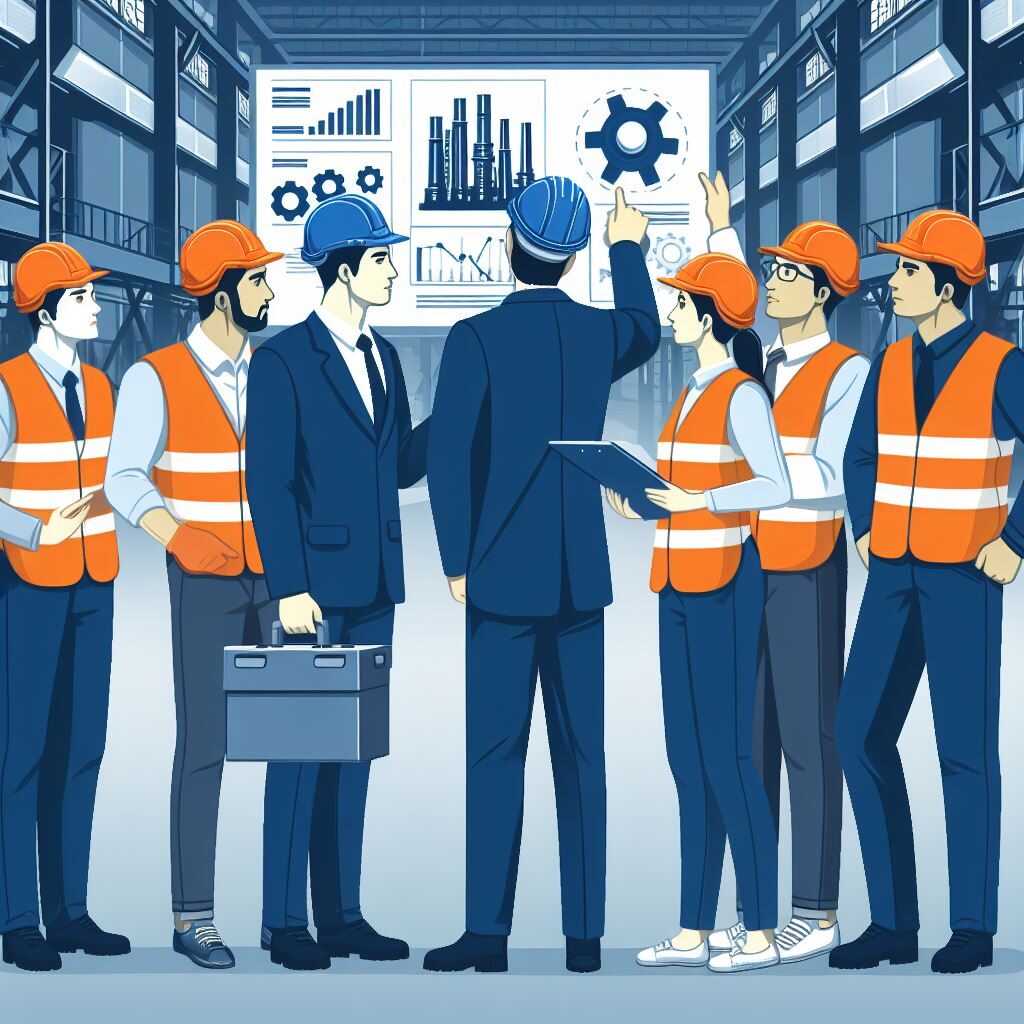
Values
Discover the benefits of collaboration
We offer a free consultation as the first step of collaboration, allowing you to familiarize yourself with our approach and verify our advisory competencies. This way, even before making a decision, you’ll feel that your situation and problem have been well understood, and the proposed solution will be optimally tailored to your company’s situation.
Our services (support) are included in a subscription, which does not generate hidden costs. The subscription-based billing allows for a significant reduction in the entry threshold into the system and enables immediate testing.
We are communicationally independent – we can develop our system without depending on the client’s IT department. We do not generate additional work for the client’s IT department. This way, we lower the implementation risk and associated costs. The possibility of quicker implementation of the solution results in faster return on investment.
Login to our applications is secured at a high level, characteristic of banking solutions. At the same time, the login process is intuitive. Your data is as secure as in a bank thanks to our system.
We offer multilingualism in our solutions through real-time translation—each employee operates applications in their native language. This enhances efficiency and reduces costs by expanding the potential labor market and eliminating the need to hire translators.
Our software features an interface optimized for quick, easy, and intuitive use, even by digitally excluded or poorly skilled employees. This means real-time savings in both time and training costs for your workforce in using the new software. The ability for rapid deployment of software for use results in a shorter transition/implementation period.
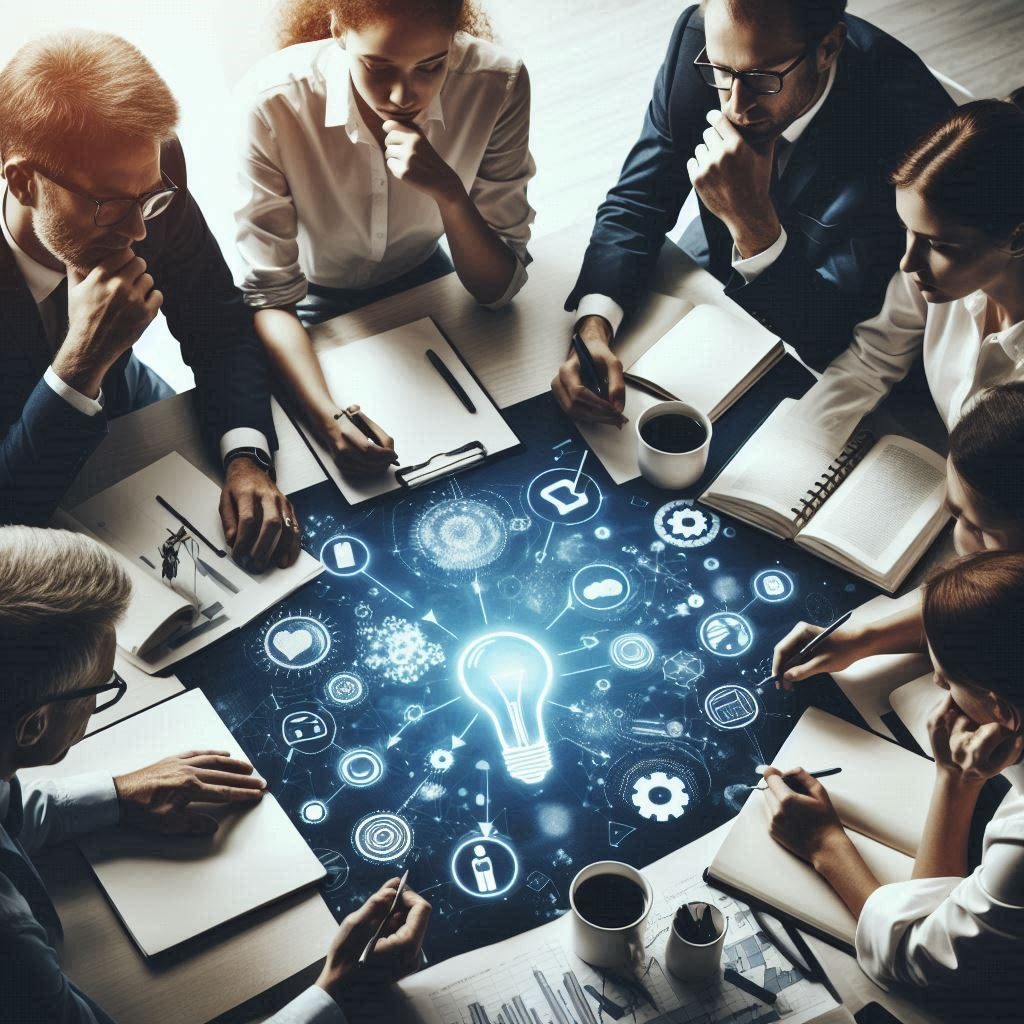