Process mapping is a recommended practice in business management that helps organizations understand and improve their operations. It involves developing a visual representation of the sequence of activities needed to achieve a specific goal.
Using a process map, one can see the entire flow of a given process, considering all the resources, steps, and decisions involved. This is particularly useful for complex, multi-stage processes where there are many opportunities for improvement and optimization.
What is it useful for?
The graphical representation of a process enables understanding its logic and flow of information, as well as identifying potential issues, delays, or unnecessary activities. Consequently, organizations can implement appropriate changes and improvements that enhance work efficiency and effectiveness.
And also:
Process mapping also facilitates a better understanding of the role of individual employees and resources within a specific process. This facilitates assigning responsibilities, distributing tasks, and conducting any necessary training or restructuring.
Process mapping – Benefits
Improving efficiency and effectiveness
By identifying unnecessary and time-consuming steps in a process, it is possible to eliminate or streamline them, leading to a shorter task completion time. As a result, the company can achieve better financial results while increasing customer satisfaction.
Identifying areas for improvement
By analyzing and understanding each stage in the process, potential problems that may affect the quality of services or products can be identified. This allows the organization to take corrective actions and avoid problems in the future.
Enhancing communication between departments
Often, different departments in a company are responsible for various stages in the business process. By creating a process map, it is possible to visualize the interdependencies between departments and identify potential areas where ineffective communication may occur. Improving communication leads to fewer errors and delays in task completion.
Increasing profitability
Better understanding and optimization of individual steps in the process result in increased profitability. By analyzing and eliminating unnecessary activities, the company can save time and resources, thereby improving its competitiveness in the market.
When is it worth using?
Process mapping can bring many benefits in various business situations. Below are a few tips to help you identify moments when it is worth using this methodology.
Company restructuring
During company restructuring, it is often necessary to identify the sources of problems and inefficiencies. Process mapping allows you to trace the individual stages of the company’s activities, indicating areas that require optimization. This enables understanding of the changes that need to be made to improve the efficiency and performance of the organization.
Introducing new technologies
When introducing new technologies to a company, it is important to understand how these changes will impact business processes. Process mapping enables precise identification of which stages of activity require adjustment to the new tools, as well as assessing the effectiveness of these changes. This allows avoiding unforeseen problems and optimizing the implementation of new technologies.
Business development
Process mapping is particularly useful when it comes to business development, as it involves coordinating new areas of activity with existing processes. This enables determining the necessary changes to introduce new products or services, as well as identifying potential problems and challenges. Process mapping allows for a better understanding of how different elements of the business are interconnected and how they affect each other.
How to conduct process mapping?
Process mapping is a complex task that requires a thorough understanding of the organization’s goals and analysis of the actions performed by employees.
Process Mapping – Stages
Goal identification
The organization must determine why it wants to conduct process mapping and what benefits it wants to achieve. Often, the main goal is to increase efficiency and improve the quality of the organization’s operations.
Gathering information from employees
This is an important stage that allows gaining insights into the daily activities. Employees should be involved in this process as they possess the most detailed knowledge about the processes and can provide valuable information. An effective and convenient tool for collecting information from employees is, for example, the Cluer system.
Analysis of gathered information
In this stage, key steps and dependencies between them need to be identified. It is also possible to determine what information is processed in a given process and what the outcomes of these actions are.
Development of process map
There are many techniques and tools that can help accurately present the sequence of actions. One of them is Data Flow Diagrams (DFDs), which show how information flows between different parts of the organization. Another technique is the use of Process Maps in the form of Event-Driven Process Chain (EPC) diagrams. EPC diagrams allow for a detailed presentation of the sequence of actions and their dependencies.
Verification
This involves checking if the process map aligns with the actual operation of the organization. This can be done through consultations with employees involved in the process or through on-site observation of activities.
Implementation of process mapping
The organization needs to ensure that employees are aware of the changes and understand the benefits that can arise from the new way of operating. This may require training and the introduction of new procedures.
How to use process mapping results?
Process mapping results are an extremely valuable tool for any organization as they allow for a better understanding and analysis of actions taken within the company. This enables the implementation of appropriate strategies aimed at improving the business.
Identification of automation areas
One of the main ways to use process mapping results is to identify potential areas for automation. Mapping allows for the precise identification of processes that can be streamlined through the use of technology. Automating these processes can lead to significant reduction in execution time and increased efficiency. Examples include automating accounting processes or customer data management.
Identification of inefficiencies
Another aspect that can be improved through process mapping results is internal procedures within the company. Analyzing the flow of information and actions allows for the identification of potential errors or inefficiencies in operation. This enables the implementation of changes that improve transparency, reduce the time required to complete a task, and decrease the risk of errors.
Cost reduction
Process mapping can also help significantly reduce operating costs for a company. Through a thorough examination of processes, all unnecessary activities or downtime that generate additional costs can be identified. Removing these elements can result in substantial savings and improve the company’s efficiency.
It is worth noting
Process mapping is not a one-time activity. To maintain competitiveness and adapt to changing market conditions, process maps should be regularly updated and monitored. This allows for real-time analysis of company operations and the ability to respond to potential problems or opportunities. This is particularly important in today’s fast-paced business environment where the pace of change is rapid.
Example of applying process mapping in practice
What does it look like in practice? Below we present a specific example of applying process mapping in a company.
The example is a manufacturing company that decided to map its processes to increase efficiency and improve the quality of its products.
Problem identification
Before starting the process mapping, the company encountered many problems such as frequent delivery delays, production errors, and low customer satisfaction.
Team
The first step was to create a team responsible for process mapping. The team consisted of representatives from different departments of the company, such as production, logistics, quality, sales, and customer service. This team was properly trained in process mapping and equipped with tools that facilitated the identification, analysis, and documentation of processes.
Process analysis
Next, the phase of process identification and analysis was started. The team conducted interviews and observations on the factory premises and collected data from employees about existing processes. This made it possible to accurately identify the stages and steps in individual processes, their dependencies, and the problems that occur.
Quality and efficiency analysis
After identifying the processes, the team proceeded to analyze them in terms of efficiency and quality. Using process mapping tools such as flowcharts, the team was able to visually present the entire process from start to finish. This made it easy to locate unnecessary activities, delays, duplicate actions, and other problems.
Process changes
The next step was to introduce changes to the processes. Based on the analysis, the team made modifications to individual stages and steps, eliminating unnecessary activities, optimizing the sequence of actions, and introducing new procedures aimed at improving the quality of products and services.
Monitoring of results
After implementing the changes, the team started monitoring the results. Using performance indicators such as order fulfillment time, number of customer complaints, or product returns, the company was able to assess the effectiveness of the implemented changes. In case of unsatisfactory results, further process modifications were made.
Benefits of process mapping
Order fulfillment time was significantly shortened, allowing the company to offer customers shorter delivery times. The quality of products also improved because greater control and optimization of production processes eliminated errors and defects.
Additionally, thanks to process mapping, the company increased its operational efficiency. Areas of redundancy and duplicate actions were identified, which allowed for saving time and resources. Employees also reported greater job satisfaction because process transparency made it easier for them to perform tasks.
Summary
Process mapping can bring many benefits, such as increased operational efficiency, improved service quality, or shortened order fulfillment time. The conclusion is that process mapping should be treated as an integral part of business management. It provides companies with visibility and control over their actions, enabling them to quickly respond to changing market conditions and achieve better results. Therefore, it is worth considering the implementation of process mapping in your company and using it as an effective tool to improve competitiveness and achieve benefits.
How can Signalo help?
Signalo provides comprehensive solutions that significantly streamline processes in companies. Below we present the benefits resulting from their implementation.
Task allocation for forklifts
Thanks to this system, the company can greatly increase efficiency and effectiveness in the logistics area. Automatic task assignment shortens order fulfillment time and optimizes the route of the forklift in the warehouse, saving 30% of the costs associated with the operation of the forklift fleet.
CMMS system
Implementing the CMMS system provided by Signalo enables effective management of maintenance and planning of maintenance operations. This prevents equipment failures, minimizes production downtime, and reduces repair and maintenance costs.
Competence matrix software
Signalo offers the SkillsMatrix system, which allows companies to effectively manage employees’ skills. This enables quick and precise allocation of the right employees to specific tasks, leading to better work organization, increased productivity, and minimized risk of errors.
Employee suggestion collection system
With the Cluer system, employees have the opportunity to submit suggestions and ideas for improving processes in the company. This is a valuable source of information for management, allowing for the identification of areas that need improvement and the implementation of innovative solutions.
Automatic tool cabinets
Signalo also implements an automatic tool cabinets that greatly facilitates the management and control of employee equipment. This helps prevent tool loss, increases availability, and ensures that tools are always in good technical condition.
Note!
Implementing solutions from Signalo allows companies to increase efficiency, reduce costs, improve work organization, and enhance service quality. This is an investment that brings long-term benefits and significantly supports business development. As we have many other interesting solutions that reduce costs, increase efficiency, and optimize resource consumption, we invite you to a free consultation. We treat each client individually by proposing a solution after familiarizing ourselves with the specifics of operations and processes.
Identyfication of optimization areas
Would you like to find out how you can save costs?
See the auxiliary list and answer the questions. Send us your answers. We will call you and based on the obtained information, we will present proposed solutions.
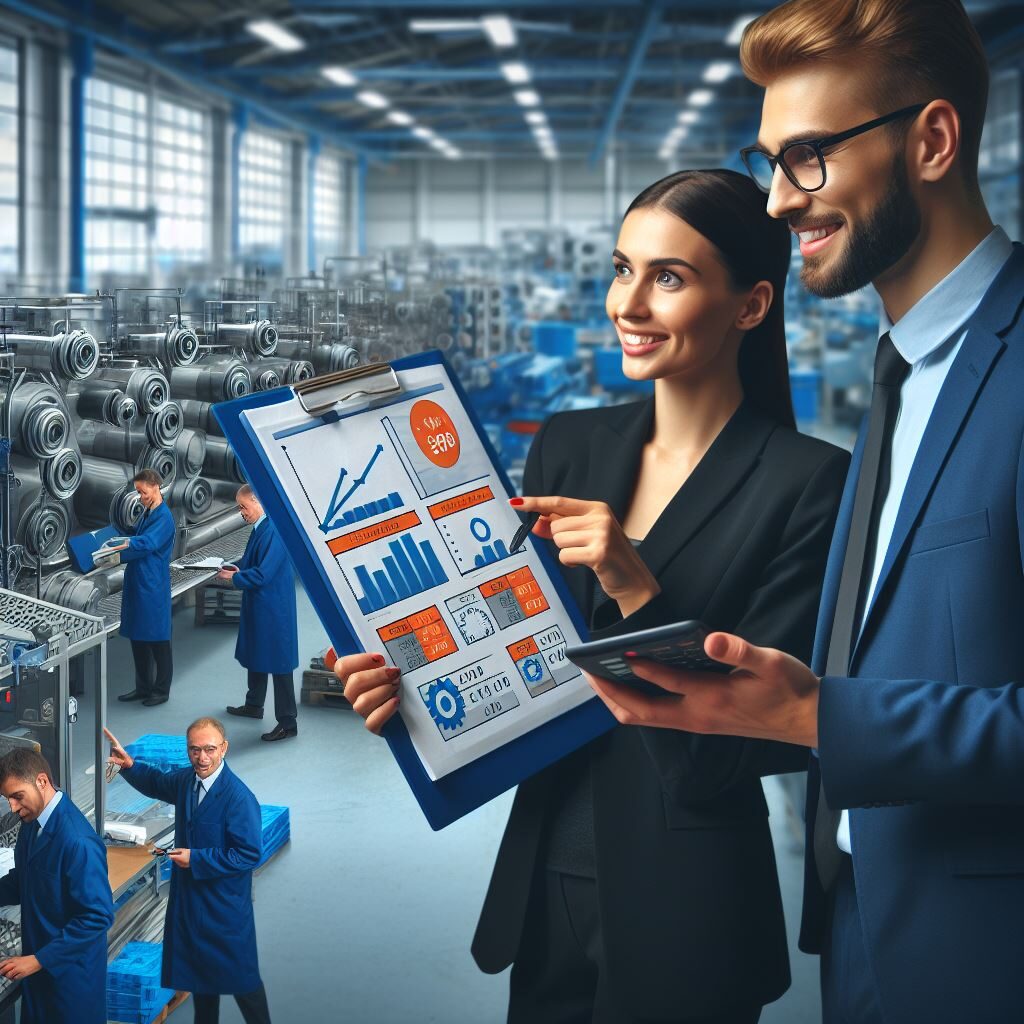
Values
Discover the benefits of collaboration
We offer a free consultation as the first step of collaboration, allowing you to familiarize yourself with our approach and verify our advisory competencies. This way, even before making a decision, you’ll feel that your situation and problem have been well understood, and the proposed solution will be optimally tailored to your company’s situation.
Our services (support) are included in a subscription, which does not generate hidden costs. The subscription-based billing allows for a significant reduction in the entry threshold into the system and enables immediate testing.
We are communicationally independent – we can develop our system without depending on the client’s IT department. We do not generate additional work for the client’s IT department. This way, we lower the implementation risk and associated costs. The possibility of quicker implementation of the solution results in faster return on investment.
Login to our applications is secured at a high level, characteristic of banking solutions. At the same time, the login process is intuitive. Your data is as secure as in a bank thanks to our system.
We offer multilingualism in our solutions through real-time translation—each employee operates applications in their native language. This enhances efficiency and reduces costs by expanding the potential labor market and eliminating the need to hire translators.
Our software features an interface optimized for quick, easy, and intuitive use, even by digitally excluded or poorly skilled employees. This means real-time savings in both time and training costs for your workforce in using the new software. The ability for rapid deployment of software for use results in a shorter transition/implementation period.
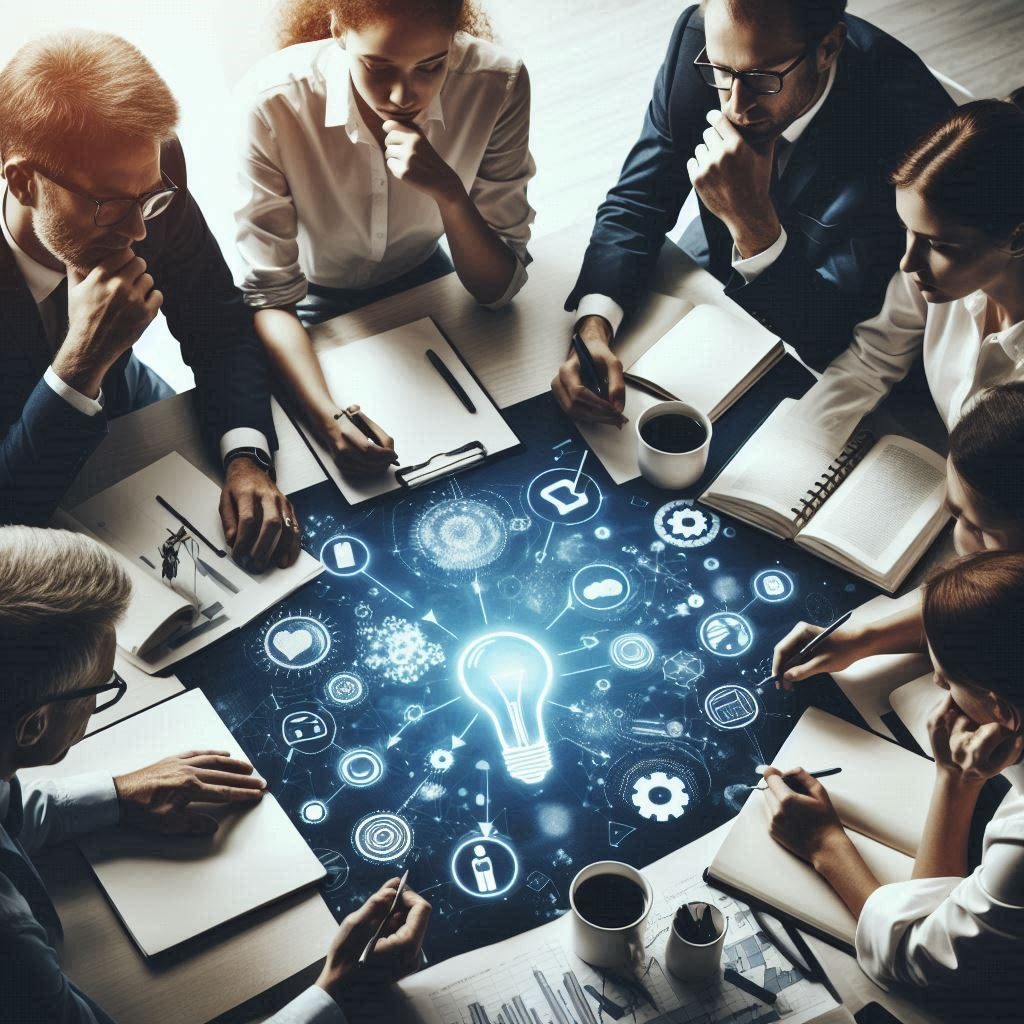