Reducing labor costs
Strategies for Reducing Labor Costs Without Compromising Quality for Producers
With increasing competition and cost pressures, finding effective strategies to reduce labor expenses without compromising the quality of the final product has become a significant challenge for many businesses.
Managing labor costs is important for the sustainability and profitability of any business. Labor costs typically constitute a substantial portion of a producer’s overall expenses. Therefore, it is essential to find ways to optimize labor expenses without sacrificing the quality of the end product. Moreover, maintaining high-quality standards is essential to fulfill customer expectations and retain a competitive edge in the market. Ensuring a balance between labor costs and product quality is crucial for long-term success and growth.
Efficient Workforce Management
Emphasizing Workforce Planning and Scheduling
Efficient workforce planning and scheduling are essential for optimizing productivity and minimizing labor costs. By accurately determining staffing requirements based on demand forecasts, organizations can ensure they have the right number of employees at the right time. This not only prevents overstaffing and understaffing situations but also enables better utilization of resources and reduces unnecessary labor expenses.
Utilizing Technology-Driven Solutions for Demand Forecasting and Resource Allocation
Technology-driven solutions, such as labor management software, provide invaluable tools for accurate demand forecasting and efficient resource allocation. These software solutions use data, and analytics to adjust their workforce accordingly. By aligning staffing levels with demand, organizations can avoid unnecessary overtime costs or idle employees, ultimately leading to increased productivity and reduced labor expenses.
Enhancing Flexibility through Cross-Training Employees
Overdependence on specific skillsets can be detrimental to an organization’s efficiency and cost-effectiveness. Cross-training employees across various roles and responsibilities enhances flexibility within the workforce. When employees are trained to handle multiple tasks, organizations can easily reallocate resources based on changing demands or unexpected absences. This reduces downtime and ensures that work continues smoothly without the need for additional hiring or outsourcing. Cross-training also improves employee morale, job satisfaction, and overall engagement, leading to a positive work environment.
Implementing Lean Manufacturing Practices – Reducing labor costs
Reducing Labor Costs while Maintaining Quality through Lean Manufacturing Practices
Lean manufacturing practices have proven to be highly effective in reducing labor costs without compromising on the quality of products. By eliminating waste, optimizing processes, and improving overall efficiency, companies can achieve significant cost savings while maintaining high standards of quality.
One of the keyways lean manufacturing achieves this is through the concept of waste reduction. By identifying and eliminating non-value adding activities, such as overproduction, waiting time, and unnecessary transportation, companies can effectively reduce labor requirements. This means that employees can focus their efforts on value-added tasks, leading to increased productivity and reduced labor costs.
Furthermore, implementing standardized work procedures ensures consistent quality across all production processes. By clearly defining the steps and specifications for each task, companies can minimize errors and rework, resulting in improved efficiency and reduced labor costs associated with fixing mistakes.
Streamlining Production Processes with Techniques like Value Stream Mapping and Waste Reduction Initiatives
Value stream mapping is a powerful tool used in lean manufacturing to identify areas of waste and inefficiency within production processes. By visually mapping out the entire value stream, from raw materials to the final product, companies gain a comprehensive understanding of the entire process and can identify opportunities for improvement.
Standardized work procedures also play a critical role in streamlining production processes. By establishing clear guidelines for each task, companies can ensure that employees follow the most efficient and effective methods. This reduces variability in production and allows for smoother workflows, ultimately reducing labor costs.
Positive Outcomes of Implementing Lean Manufacturing
Implementing lean manufacturing practices can yield numerous positive outcomes for companies.
- Improved efficiency is one of the most significant benefits. By eliminating waste and optimizing processes, companies can achieve faster cycle times and increased productivity, resulting in cost savings and improved customer satisfaction.
- Lean manufacturing practices can reduce downtime by addressing bottlenecks and improving overall equipment effectiveness. This translates into a more productive workforce and reduced labor requirements.
- Implementing lean manufacturing practices often leads to decreased labor requirements. By eliminating wasteful activities and streamlining processes, companies can achieve higher levels of productivity with fewer employees. This not only reduces labor costs but also allows companies to allocate resources to other areas for further growth and development.
Automation and Robotics Integration
Automation systems and robots are designed to carry out tasks efficiently, consistently, and without fatigue. This reduces the need for breaks, shifts, training, and employee turnover. The consistency and precision of automation also contribute to improved product quality, as robots can follow programmed instructions precisely and consistently.
Additionally, automation and robotics can optimize production processes, leading to better resource utilization and reduced waste. Automated systems can identify and rectify errors or inefficiencies in real-time, resulting in higher-quality products and reduced rework or scrap.
Examples of automation technologies used in various industries
- Robotic Process Automation (RPA): RPA technology uses software robots or “bots” to automate repetitive, rule-based tasks typically performed by humans. It can be applied in industries such as banking, insurance, customer service, and healthcare to streamline processes like data entry, invoice processing, claims processing, and more.
- Industrial Robots: These robots are commonly used in manufacturing and assembly lines to perform tasks such as welding, painting, packaging, and material handling. They can work at high speeds, with precision, and in hazardous environments, reducing labor costs and improving productivity.
- Collaborative Robots (Cobots): Cobots are designed to collaborate with humans in shared workspaces. They can assist with tasks that require human dexterity and decision-making while ensuring safety. Cobots are utilized in industries like electronics, automotive, and healthcare for tasks such as assembly, inspection, and collaborative logistics.
- Autonomous Vehicles: These include self-driving cars, drones, and automated guided vehicles (AGVs). They are employed in transportation, logistics, and warehousing industries to automate tasks such as delivery, inventory management, and material handling.
The potential benefits of integrating automation and robotics
- By automating repetitive tasks, companies can significantly reduce the time required for completion, resulting in faster production cycles and increased output.
- Automation also enhances precision by eliminating human errors and inconsistencies. This leads to higher product quality, reduced defects, and fewer product recalls or rework, ultimately saving costs associated with these issues.
- Robotics and automation can boost overall productivity by optimizing resource utilization, minimizing downtime, and enabling continuous operation. With increased productivity, companies can achieve higher output levels without the need for additional labor, thus reducing labor expenses.
Outsourcing and Contractor Utilization
Exploring the Option of Outsourcing Non-Core Activities or Using Contract Workers to Mitigate Labor Costs
Outsourcing non-core activities or utilizing contract workers can be an effective strategy for businesses looking to mitigate labor costs. By outsourcing tasks that are not directly related to the core operations of the company, businesses can significantly reduce labor overheads. This allows companies to allocate their resources more efficiently and focus on their core strengths.
The Advantages of Outsourcing
- Reduced labor overheads. By outsourcing tasks to external vendors or contractors, businesses can avoid hiring additional full-time employees and the associated costs such as benefits, training, and office space.
- Access to specialized skills and expertise. External vendors often have a team of professionals with extensive experience in the specific task or service being outsourced. This allows businesses to tap into a pool of talent that they might not otherwise have access to, resulting in higher quality outputs.
- Outsourcing also provides scalability. Businesses can easily ramp up or down the outsourced services based on their current needs. This flexibility allows companies to adapt to changing market conditions, without the burden of hiring or laying off staff.
Addressing Potential Challenges
- While outsourcing offers various advantages, it also presents potential challenges that businesses need to address. One crucial challenge is ensuring adherence to quality standards. When outsourcing tasks, it is essential to establish clear expectations and guidelines to maintain consistent quality in the deliverables. Regular monitoring and feedback mechanisms can help ensure that the outsourced work meets the desired standards.
- Effective communication is another challenge when working with external vendors or contractors. Without proper communication channels in place, misunderstandings can arise, leading to delays and inefficiencies. Establishing regular communication protocols and leveraging technology tools can help facilitate effective communication between the outsourcing partner and the business.
- Maintaining control over outsourced operations is also a concern for businesses. It is essential to establish strong contractual agreements that outline expectations, deliverables, and performance metrics. Regular performance evaluations and audits can help businesses maintain control and ensure that the outsourced operations align with their objectives.
Continuous Improvement and Employee Involvement
Fostering a Culture of Continuous Improvement
The emphasis on constant growth and development helps companies stay ahead of the curve and adapt to changes in the market. By instilling a mindset of continuous improvement, organizations empower their employees to seek out better ways of doing things, identify and resolve problems, and drive innovation.
Employee Involvement – Harnessing the Power of Collective Intelligence
One of the most effective ways to foster a culture of continuous improvement is by involving employees in problem-solving initiatives, encouraging innovative ideas, and soliciting feedback. When employees are actively engaged in the improvement process, they feel valued and motivated to contribute their unique perspectives and expertise. This collective intelligence can lead to breakthrough ideas and creative solutions that might otherwise go unnoticed. Additionally, involving employees in decision-making processes boosts morale, increases job satisfaction, and enhances overall employee engagement. The Cluer tool is highly recommended; it is a platform that enables automated collection of suggestions through electronic submissions from every employee.
The Benefits of Employee-Driven Process Improvements
Employee-driven process improvements have numerous benefits for organizations.
Optimizing labor utilization
Employees on the front lines of the business often have valuable insights into inefficiencies or bottlenecks that can be addressed to streamline processes and improve productivity. This optimization leads to cost reductions and greater operational efficiency.
Enhancing product quality
Employees who are invested in the success of the organization are more likely to identify quality issues and propose solutions to rectify them. Their firsthand experience and understanding of customer needs enable them to suggest improvements that ultimately result in higher-quality products or services. This not only satisfies customers but also strengthens the organization’s reputation in the market.
Fostering a culture of continuous improvement and involving employees in problem-solving initiatives is essential for organizations aiming to stay competitive. By empowering employees to contribute their ideas and insights, organizations can optimize labor utilization, reduce costs, and enhance product quality. Embracing employee-driven process improvements not only benefits the organization but also leads to increased employee satisfaction and engagement.
Cost Savings through Information Technology Tools
Cost Reduction in Forklift Operations
The use of information technology tools can significantly contribute to cost savings in various aspects of a business. One area where this is evident is in the reduction of costs associated with forklift operations. By implementing advanced management systems, businesses can optimize the efficiency of their forklift fleets, thereby minimizing fuel consumption, maintenance costs, and labor requirements. This not only reduces costs but also enhances productivity and safety in the workplace.
Lowering Machine Costs through CMMS
Another way that information technology tools can generate cost savings is through the implementation of a Computerized Maintenance Management System (CMMS). CMMS enables businesses to streamline their maintenance operations, ensuring that machines are properly maintained, minimizing breakdowns, and extending their lifespan. By scheduling regular maintenance tasks, tracking equipment performance, and managing spare parts inventory efficiently, CMMS eliminates unnecessary downtime and prevents costly emergency repairs. Additionally, CMMS provides valuable insights into the overall health of machines, allowing businesses to make informed decisions about repair or replacement, ultimately reducing long-term investment costs.
Gathering Employee Suggestions – Cluer System for Continuous Improvement
Harnessing the knowledge and expertise of employees is crucial for continuous improvement in any organization. To encourage and collect employee suggestions effectively, businesses can utilize the Cluer system, an innovative information technology tool. The Cluer system allows employees to submit their ideas, suggestions, and feedback easily, creating a culture of involvement, collaboration, and empowerment. By providing a platform for employees to contribute their insights and experiences, businesses can tap into a wealth of knowledge and identify areas for improvement that may have otherwise gone unnoticed. This process promotes cost savings by optimizing processes, enhancing efficiency, and fostering a sense of ownership and engagement among employees.
Free Consultation with Signalo – Unlock Your Business Potential
Discover from Experts How Signalo Can Optimize Different Areas of Your Business
With Signalo’s free consultation service, you can tap into the expertise of our specialists and explore how our solutions can benefit your business.
Tailoring Signalo Solutions to Fit Your Specific Business Requirements
Each business has its unique characteristics and challenges. At Signalo, we understand that one size does not fit all. That’s why our free consultation service is designed to help tailor our solutions to match the specific needs of your business.
Understanding Your Business’s Requirements
During the consultation, our experts will take the time to understand the intricacies of your business, including industry nuances, operational workflows, and key pain points. By gaining a comprehensive understanding of your specific requirements, we can provide you with customized recommendations and solutions that address your business’s unique challenges.
Book your free consultation today and unlock your business’s true potential with Signalo.
Values
Discover the benefits of collaboration
We offer a free consultation as the first step of collaboration, allowing you to familiarize yourself with our approach and verify our advisory competencies. This way, even before making a decision, you’ll feel that your situation and problem have been well understood, and the proposed solution will be optimally tailored to your company’s situation.
Our services (support) are included in a subscription, which does not generate hidden costs. The subscription-based billing allows for a significant reduction in the entry threshold into the system and enables immediate testing.
We are communicationally independent – we can develop our system without depending on the client’s IT department. We do not generate additional work for the client’s IT department. This way, we lower the implementation risk and associated costs. The possibility of quicker implementation of the solution results in faster return on investment.
Login to our applications is secured at a high level, characteristic of banking solutions. At the same time, the login process is intuitive. Your data is as secure as in a bank thanks to our system.
We offer multilingualism in our solutions through real-time translation—each employee operates applications in their native language. This enhances efficiency and reduces costs by expanding the potential labor market and eliminating the need to hire translators.
Our software features an interface optimized for quick, easy, and intuitive use, even by digitally excluded or poorly skilled employees. This means real-time savings in both time and training costs for your workforce in using the new software. The ability for rapid deployment of software for use results in a shorter transition/implementation period.
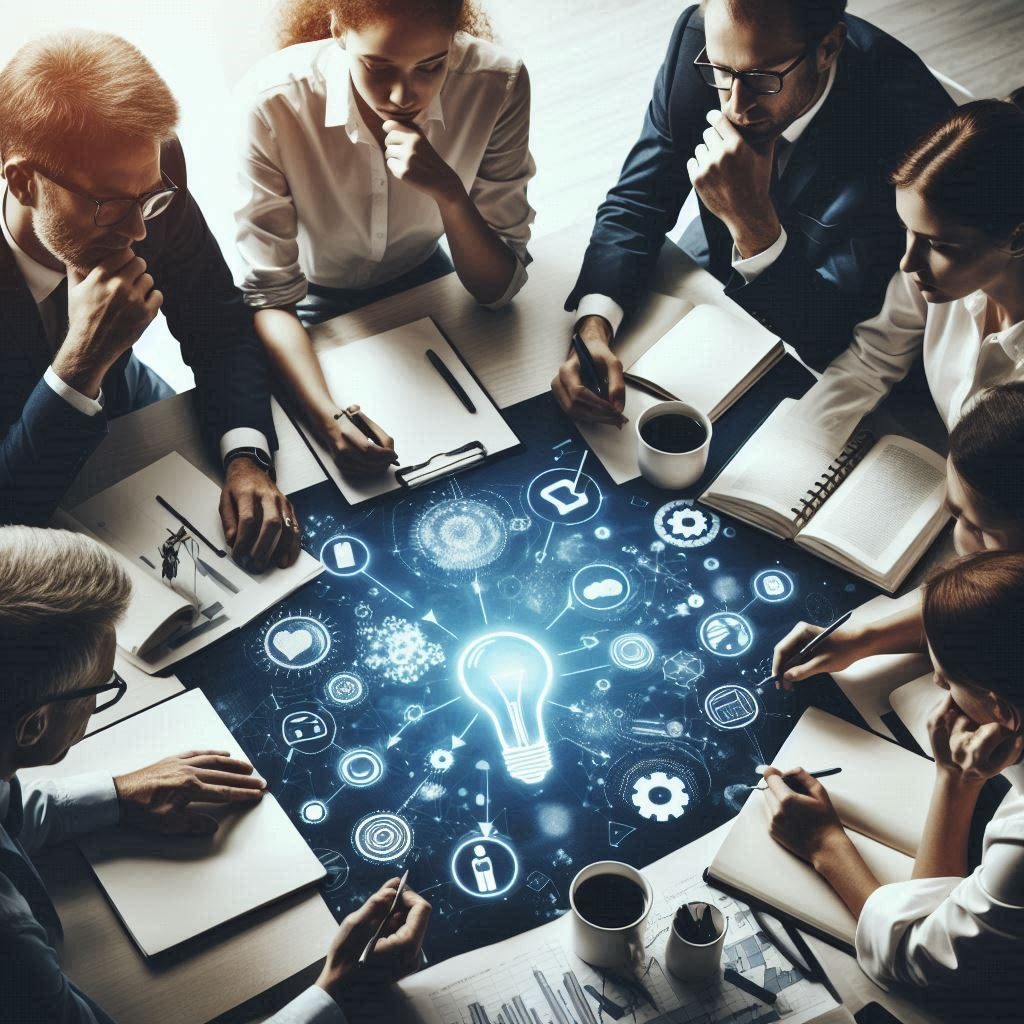