TQM – What does it involve?
The quality of products and services is crucial for the success of businesses and customer satisfaction. In the current market situation, where customers have increasing expectations, quality becomes one of the main factors determining the choice of products and services.
Quality in production refers to meeting the requirements and expectations of customers in terms of functionality, reliability, durability, safety, and aesthetics of products. Ensuring high quality contributes to building customer trust in the brand and maintaining competitiveness in the market.
Challenges related to ensuring high quality
Although quality is extremely important, ensuring it in the production process can be difficult and challenging for businesses. Manufacturers must deal with various factors that can affect the quality of products.
The main problems related to ensuring high quality in production are:
Quality control
Manufacturers need to develop appropriate quality control systems and procedures to ensure that every product coming off the production line meets the specified standards. Lack of effective quality control procedures can lead to defective products and complaints.
Cultivating a culture of quality
High quality must be a priority for all employees in the organization. It is necessary to implement appropriate training and incentive programs that will shape a positive culture of quality in all areas of the organization.
Supplier management
Quality does not only begin on the production line. It is important for manufacturers to collaborate with reputable suppliers who also have high quality standards. Failure to meet requirements by suppliers can affect the quality of the final product.
Continuous improvement
Implementing the philosophy of Total Quality Management (TQM) is one of the key solutions that help manufacturers achieve high quality. TQM involves managing quality at all levels of the organization, from the efficiency of production processes to employee involvement in quality improvement.
TQM in Production – Understanding the Problem
Currently, many companies struggle with the problem of low quality and errors in production processes, which leads to inefficiency and negative consequences for the company.
Inefficiency in production – reasons
- Low product quality can result from various factors, such as inadequate employee training, lack of control over the production process, errors in product design or in the production process itself. These problems lead to frequent defects and flaws in products, which negatively impact the final product quality.
- Furthermore, production errors can have long-term effects on a company, such as a decrease in customer trust. Customers expect high-quality products and services, and when they receive defective products, they lose trust in the brand and may refrain from further purchases. This, in turn, leads to decreased sales and loss of competitiveness in the market.
Negative consequences
- Low-quality products lead to reduced company performance. Frequent occurrence of errors requires repairs, which, in turn, cause production interruptions and delays in deliveries. This increases the company’s costs and leads to inefficient allocation of resources.
- High costs of repairs and complaints are also inherent consequences of low-quality products. Companies are forced to spend on improving defective products, as well as on returns or exchanges for affected customers. These additional costs burden the company’s budget and lead to decreased profitability.
- Furthermore, the negative consequences of low-quality products can affect a company’s reputation. Poor quality and frequent complaints can negatively impact the perception of the brand by customers. Negative opinions and reviews about the company’s products can quickly spread in the era of social media, which can have long-lasting effects on the company’s image and position in the market.
What is TQM
Total Quality Management (TQM) is a management strategy aimed at achieving excellence in service and product quality through the involvement of all employees and their continuous improvement. The main goal of TQM is to provide customers with excellent quality products and services that meet their expectations and satisfy their needs in the most efficient way.
Benefits of implementing TQM
- Implementing TQM in the production process has many benefits for a company. Firstly, TQM focuses on continuous quality improvement, which leads to a reduction in defective products and increased customer satisfaction. By eliminating errors and defects at every stage of production, TQM contributes to significant cost reduction in quality.
- Another advantage of TQM is increased efficiency in the production process. Through optimization and standardization of procedures, waste elimination, and improved communication between departments, TQM allows for a smoother and more efficient flow of production. This is achieved by implementing principles of continuous improvement, motivating employees to participate in process improvement, and using appropriate tools and techniques such as line balancing or the 5S method.
- Lastly, but not least, customer satisfaction is a significant benefit of implementing TQM in production. By focusing on using customer feedback, their needs and expectations, a company can adjust its processes and products to market requirements. As a result, the company can build stronger customer relationships, increase loyalty, and gain a competitive advantage.
Management tools supporting TQM in production
Forklift management system
The implementation of a forklift management system is one of the important tools for improving internal logistics and minimizing material damages. Within TQM in production, this system enables optimal use of forklifts by providing information about their location, availability, and task load. As a result, companies can effectively manage forklift traffic, minimize waiting time, and reduce the risk of collisions and material damages.
Andon 4.0 concept
Another important tool in the context of TQM in production is the Andon concept. It is a method for quickly detecting and reacting to production problems in real-time. Andon relies on utilizing a system that notifies about failure, problems, or imperfections in the production process. This allows employees to take immediate corrective actions, contributing to faster problem resolution, minimizing losses, and increasing the overall efficiency of the production process.
Computerized Maintenance Management System (CMMS)
Another tool supporting TQM in production is the Computerized Maintenance Management System (CMMS). It is a computerized system for managing and maintaining production machinery. CMMS enables effective planning and monitoring of maintenance and repair work, resulting in minimized downtime and failures. With CMMS, companies can also track maintenance history accurately and predict future maintenance needs, thereby improving the quality and reliability of the production process.
Vibration measurement on machines
Another effective tool used within TQM in production is vibration measurement on machines. This method involves monitoring vibrations generated by machines during their operation to detect potential failures and prevent them. Vibrations serve as a signal that something might be wrong, so monitoring them allows for quick response and corrective actions. As a result, companies can minimize the risk of machine failures, ensuring production continuity and avoiding losses associated with downtime.
Kaizen as a complement to TQM
- The concept of Kaizen, which is often seen as an integral part of Total Quality Management (TQM), involves continuous improvement and optimization of processes to achieve better results. In the manufacturing industry, it is particularly important to constantly improve both products and the processes involved in their creation.
- The role of employees in suggesting Kaizen ideas and solving problems on an ongoing basis is extremely important. They are the most engaged and have the best knowledge of the daily challenges related to production. Therefore, they should be encouraged to submit their ideas for improvements and to solve the problems they encounter.
- In practice, Kaizen can involve many different actions aimed at improving quality, increasing efficiency, or eliminating waste in production. Examples of this could include reducing the time required for a particular task, decreasing the number of defective products, or optimizing the layout of workstations to increase productivity.
The Cluer system in service of TQM
One of the tools that can facilitate the collection of employee suggestions and problem reporting is Cluer software. This user-friendly tool allows employees to quickly and conveniently submit their ideas and problems, enabling timely responses to difficulties and implementing improvements.
Conclusion
As a result, Kaizen as a complement to TQM can bring numerous benefits to production. Continuous process improvement and employee engagement allow bottlenecks and production problems to be identified and solved much faster. Additionally, improving product quality, increasing efficiency, and eliminating waste contribute to enhancing the company’s competitiveness in the market.
Summary
This article emphasizes the importance of quality management in production and its impact on improving quality and effectiveness. The presented management tools, such as TQM, are invaluable aids in solving production problems and achieving success.
- Introducing Total Quality Management (TQM) to a company brings numerous benefits. One of them is continuous improvement of product and service quality, leading to customer satisfaction and long-term business relationships. TQM also enables increased efficiency and profitability of production by eliminating waste and reducing costs.
- In summary, the implementation of TQM and the management tools described in the article are significant in solving production problems and achieving success. We encourage taking action in this direction to improve the quality and effectiveness of production and increase the company’s competitiveness in the market.
TQM – Support from Signalo
Signalo is a company with extensive experience in working with multiple manufacturing companies. Their expertise includes implementing advanced IT systems that improve operational efficiency, increase workplace safety, and reduce production costs. We offer our support to clients through free consultations, during which we identify areas that can be optimized using tools developed by their team.
Benefits of implementing TQM with support from Signalo
Implementing TQM in a manufacturing company with support from Signalo brings numerous benefits.
Improved operational efficiency
It leads to increased production performance. The tools offered by Signalo enable monitoring, analysis, and optimization of production processes, resulting in shorter production cycles and increased units produced within a specific timeframe.
Enhanced safety
Advanced monitoring tools allow for the identification of potential hazards and early warnings, avoiding accidents and injuries in the workplace.
Reduction of production costs
Signalo’s tools allow for the identification and elimination of waste in production processes, significantly reducing the consumption of resources such as raw materials and energy, resulting in lower production costs.
Free consultation with Signalo
We invite you to take advantage of a free consultation, during which their experts will present opportunities for optimizing production processes using Signalo’s tools. Consultants will help identify areas where changes can be made to improve the quality, efficiency, and safety of production. You will receive a comprehensive analysis of your company and recommendations for steps to take in order to achieve your goals.
TQM GUIDE PDF
We encourage you to download our guide developed by Signalo, which will guide you step by step into the world of Total Quality Management (TQM) in production. Thanks to our guide, you will be able to implement TQM effectively and efficiently in your manufacturing company.
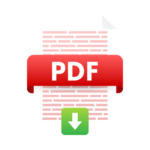
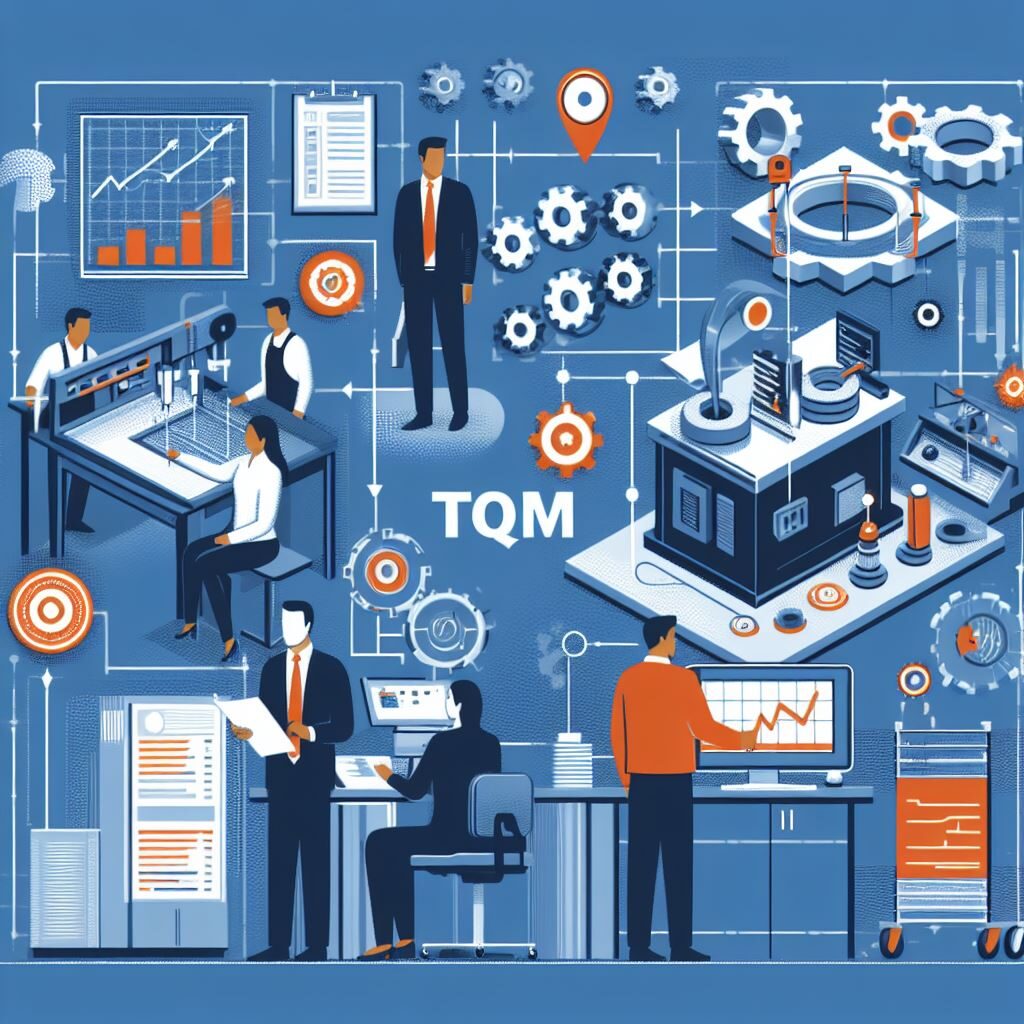
Values
Discover the benefits of collaboration
We offer a free consultation as the first step of collaboration, allowing you to familiarize yourself with our approach and verify our advisory competencies. This way, even before making a decision, you’ll feel that your situation and problem have been well understood, and the proposed solution will be optimally tailored to your company’s situation.
Our services (support) are included in a subscription, which does not generate hidden costs. The subscription-based billing allows for a significant reduction in the entry threshold into the system and enables immediate testing.
We are communicationally independent – we can develop our system without depending on the client’s IT department. We do not generate additional work for the client’s IT department. This way, we lower the implementation risk and associated costs. The possibility of quicker implementation of the solution results in faster return on investment.
Login to our applications is secured at a high level, characteristic of banking solutions. At the same time, the login process is intuitive. Your data is as secure as in a bank thanks to our system.
We offer multilingualism in our solutions through real-time translation—each employee operates applications in their native language. This enhances efficiency and reduces costs by expanding the potential labor market and eliminating the need to hire translators.
Our software features an interface optimized for quick, easy, and intuitive use, even by digitally excluded or poorly skilled employees. This means real-time savings in both time and training costs for your workforce in using the new software. The ability for rapid deployment of software for use results in a shorter transition/implementation period.
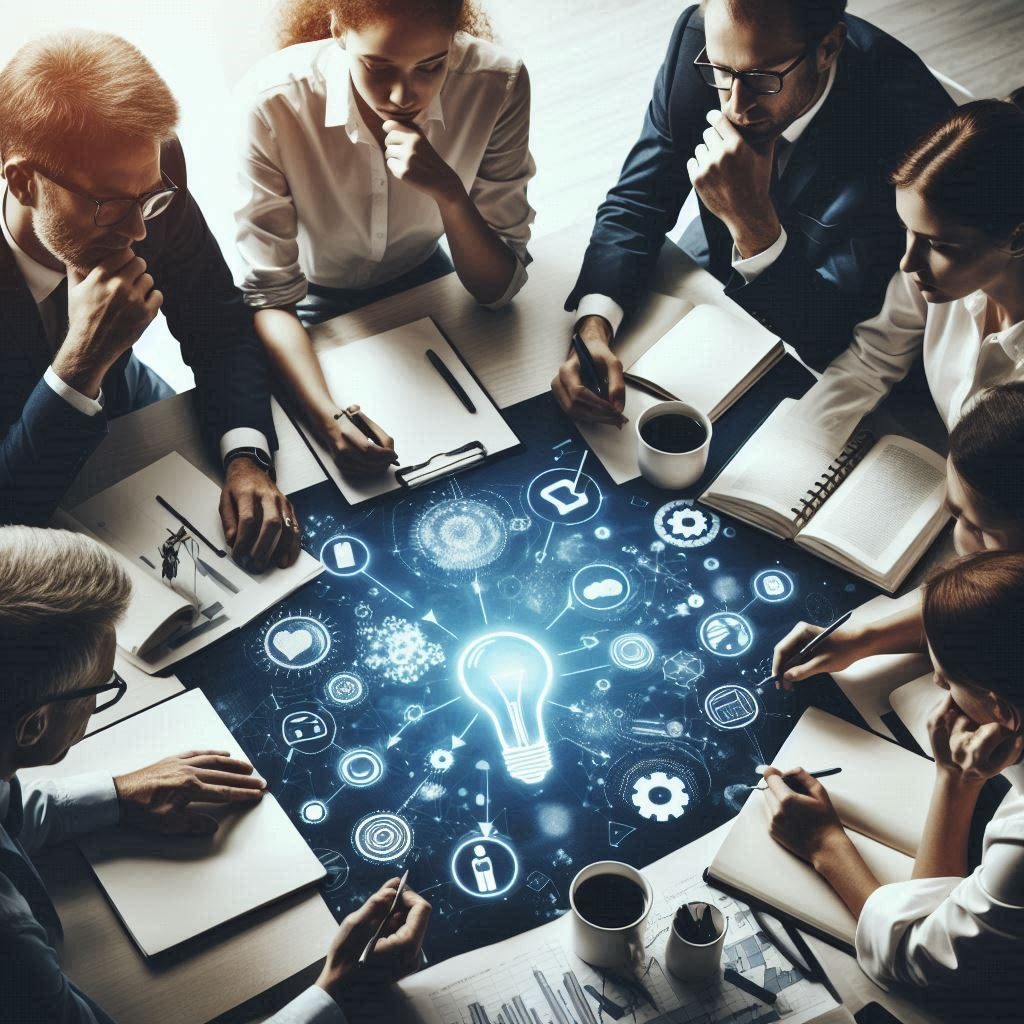