Total Productive Maintenance – Utrzymanie Ruchu pod pełną kontrolą
Total Productive Maintenance (TPM) to metoda znajdująca się w obszarze lean manufacturing, który zakłada działania w celu osiągnięcia maksymalnej dostępność i efektywności maszyn i urządzeń. TPM koncentruje się na najbardziej efektywnym wykorzystaniu czasu działania wyposażania produkcyjnego w celu wytwarzania produktów dobrej jakości. TPM stosuje się również z zamysłem zwiększenia stabilności procesów produkcyjnych, a także wydłużenia możliwości eksploatacji maszyn i urządzeń. W efekcie wszystkie działania powinny prowadzić do obniżenia kosztów utrzymania wyposażenia produkcyjnego.
Historia metody TPM
Jako pierwsza zbiór technik składających się na TPM zastosowała japońska firma Denso, z grupy Toyoty. To japońskie przedsiębiorstwo znane jest z rozwijania i wytwarzania różnych części samochodowych, m.in. oprzyrządowania dla silników spalinowych, elementów pojazdów hybrydowych, świec zapłonowych, robotów przemysłowych itp.
Podział celów TPM
Metoda TPM realizuje swoje cele w dwóch obszarach:
– zasoby ludzkie
– wyposażenie produkcyjne (urządzenia i maszyny)
Zasoby ludzkie
Jeśli chodzi o zasoby ludzkie TPM zakłada zwiększanie efektywności poprzez poszerzenie umiejętności i wiedzy pracowników – co jest równoznaczne ze zwiększeniem ich odpowiedzialności i poziomu kwalifikacji. Założeniem jest by stali się oni bardziej zaangażowani w powierzone im obowiązki, dokonywali trafniejszych ocen sytuacji. W przypadku spełnienia tych założeń są oni gotowi na samodzielne podejmowanie właściwych decyzji.
Służby utrzymania ruchu mają za zadanie utrzymanie maszyn i urządzeń w stanie gotowości, w momencie, kiedy potrzebna jest realizacja przez nich zaplanowanych działań. Zespół pracujący bezpośrednio z maszynami (operatorzy, konserwatorzy, specjaliści UR) powinni mieć możliwość składania propozycji ulepszeń (Kaizen). Maksymalizacja dostępności maszyn, bezawaryjność, ma w bezpośredni sposób wpływ na zmniejszenie kosztów wytwarzania. A skoro koszty są mniejsze, tym samym, potencjalnie zwiększa się szansa na powiększenie zysków przedsiębiorstwa.
Wyposażenie produkcyjne
TPM obala mit, jakoby tylko zakup nowych maszyn mógł przełożyć się na wzrost efektywności całego procesu produkcyjnego. Zakup nowych maszyn przeważnie wiąże się ze sporą inwestycją. Zaleceniem jest poprawa efektywności wykorzystania dostępnych aktualnie maszyn i urządzeń. Warto zauważyć, że często zakup nowej maszyny nie przekłada się na natychmiastową poprawę efektywności. Nowe maszyny wymagają dobrego planu na ich wykorzystanie, odpowiednio wyedukowanej w obsłudze załogi. Spełnienie tych warunków wymaga czasu.
TPM zaleca taką zmianę organizacji pracy maszyny by spowodowała ona wzrost jej wydajności. W tym aspekcie warto przyjrzeć się w pierwszej kolejności procedurom jej obsługi, stopniu w jakim wyszkolona do jej obsługi jest załoga oraz przestrzeganiu zasad konserwacji.
8 filarów TPM
- Autonomiczne UR
Zakłada, że za poprawę efektywności pracy maszyn i urządzeń odpowiada samodzielny zespół utrzymania ruchu. Spoczywa na nim podejmowanie decyzji w kwestii napraw i konserwacji a także troska o utrzymanie w dostępności parku maszynowego.
- Planowanie nowych maszyn i urządzeń
Podejmowanie decyzji o inwestycji w par maszynowy bazujący na realnych danych. Dokonywanie zakupu wyłącznie w przypadku, gdy ma to faktyczne, ekonomiczne uzasadnienie.
- Koncentracja na wprowadzaniu usprawnień
Nieustające poszukiwanie możliwości zapobiegania problemom, które pojawiają się podczas eksploatacji posiadanych maszyn i urządzeń, a także poszukiwanie sposobów na poprawienie efektywności i jakości pracy.
- Edukacja i szkolenia
Zapewnienie najlepszej możliwie wiedzy operatorom, konserwatorom, specjalistom utrzymania ruchu w celu optymalizacji ich pracy. Np. zapewnienie operatorom takich umiejętności, by mogli samodzielnie reagować na drobniejsze awarie i sami umieli je usuwać.
- Bezpieczeństwo pracy i środowiska pracy
Zapewnienie odpowiedniego poziomu bezpieczeństwa zarówno załogi jak i środowiska poprzez np. wpływ na obniżenie emisji szkodliwych substancji.
- Zarządzanie parkiem maszynowym
Wypracowanie i utrzymanie standardu dobrych praktyk. Stałe monitorowanie istotnych wskaźników związanych z wykorzystaniem maszyn. Działania zmierzające do osiągnięcia możliwie największych efektów przy niewielkim nakładzie.
- Planowanie z wyprzedzeniem.
Istotne jest stworzenie planu konserwacji. Działanie takie powinno mieć charakter nawyku. Monitorowanie stanu maszyn i narzędzi jest kluczowe dla zapobiegania ich awariom. Terminarz przeglądów i konserwacji powinien być dostępny również służbą odpowiedzialnym za planowanie produkcji. Istotna jest zarówno data jak i szacunkowy czas przestoju.
- Zapewnienie wysokiej jakości
W przypadku problemów z jakością istotne jest błyskawiczne odnalezienie jej przyczyn, wyeliminowanie ich i podjęcie działań zmierzających do zapobiegania takiej sytuacji w przyszłości.
6 głównych strat według TPM dotyczących działania maszyn
– awarie
– niewielkie przestoje i bezczynność
– defekty, poprawki i odpad produkcyjny
– straty związane ze startem maszyn
– praca maszyn z ograniczoną szybkością
– przezbrojenia i nastawienia
Korzyści wynikające ze stosowania metodologii TPM – Total Productive Maintenance
- zredukowanie ilości i czasu przestojów planowanych i nieplanowanych (zero awarii)
- poprawa wykorzystania możliwości produkcyjnych
- zwiększenie produktywności
- redukcja czasu cyklu produkcyjnego
- optymalizacja kosztów produkcji
- zwiększenie jakości produkcji
- wydajniejsze zarządzanie zleceniami produkcyjnym
Wskaźnik OEE
Wskaźnik OEE jest jednym z głównych mierników realizacji strategii TPM oraz lean management. Na jego wymiar wpływ mają 3 składowe: jakość, dostępność oraz wydajność.
OEE = dostępność x wydajność x jakość
Od czego zacząć wdrażanie metodologii TPM?
Przede wszystkim należy skupić uwagę na najbardziej krytycznych obszarach w organizacji, które powinny w pierwszej kolejności być poddane analizie. Sensownym jest również wyznaczenie celu wdrożenia. W każdym momencie będzie on nadrzędną wartością wyznaczającą kierunek podejmowanych działań.
Jakie obszary warto objąć analizą w stosunku do posiadanego parku maszyn?
Warto skupić się na zbadaniu m.in.: awaryjności (badanie ilości awarii w określonym czasie), nowoczesności (np. jak trudna jest obsługa, czy można łatwo usprawnić maszynę w razie awarii), obciążeniu (jak mocno obciążona jest aktualnie maszyna), możliwości zastąpienia w razie awarii (warto opracować plan na wypadek gdyby maszyna uległa awarii, może on uwzględniać krótsze i dłuższe odcinki czasu).
Narzędzia informatyczne wspierające TPM
W realizacji metodologii TPM zaleca się wykorzystanie systemów wspierających realizację założeń. Pozwalają one na szybsze i zautomatyzowane osiąganie celów, przyczyniając się do obniżenia kosztów poprzez m.in.
- opóźnienie konieczności zakupu nowych maszyn (system CMMS),
- Platforma Intelekta – zdigitalizowane instrukcje stanowiskowe i BHP
- przechowywanie informacji o koniecznych przeglądach i konserwacji (system CMMS)
- lepsze wykorzystanie zasobów (matryca kompetencji, system Andon),
- zapobieganie awariom (system CMMS),
- udostępnianie szczegółowych raportów dotyczących eksploatacji i funkcjonowania maszyn.
Zachęcamy do zapoznania się z naszymi rozwiązaniami. Od lat projektujemy i rozwijamy systemy z powodzeniem wykorzystywane w przemyśle. Dzięki zastosowaniu ich w branży produkcyjnej i logistyce nasi Klienci przeciętnie oszczędzają 30% kosztów. Skorzystaj z możliwości uzyskania realnych danych, dzięki zautomatyzowanym procesom oraz opomiarowaniu maszyn. Zaletą naszych wdrożeń jest rozliczenie abonamentowe, dzięki któremu Klienci nie muszą inwestować jednorazowo dużych sum, a oszczędności generowane są od pierwszego dnia działania systemu. Posiadamy ogromne doświadczenie i bogaty portfel Klientów będących liderami w swoich branżach. Jest to dla Ciebie gwarancją udanego i sprawnego wdrożenia, dzięki któremu Twoja organizacja szybko zrealizuje swoje cele, a Ty sam możesz stać się ojcem tego sukcesu. Nowe technologie sprzyjają odważnym, nagradzając ich za podążanie za postępem.
Jakiemu wyzwaniu chcesz sprostać?
Wartości
Poznaj korzyści współpracy
Oferujemy darmową konsultację jako pierwszy krok współpracy, dzięki któremu możesz poznać nasz model działania oraz zweryfikować nasze kompetencje w zakresie doradztwa. Dzięki temu jeszcze przed podjęciem decyzji masz poczucie, że Twoja sytuacja i problem zostały dobrze zrozumiane oraz zaproponowane rozwiązanie będzie optymalnie pasować do sytuacji w Twoim przedsiębiorstwie.
Nasze usługi (wsparcie) są ujęte w abonamencie, co nie generuje kosztów ukrytych. Abonamentowa forma rozliczeń pozwala radykalnie obniżyć próg wejścia w system i od razu móc go testować.
Jesteśmy niezależni komunikacyjnie – potrafimy rozwinąć nasz system bez zależności od działu IT klienta. Nie generujemy dodatkowej pracy dla działu IT. Obniżamy w ten sposób ryzyko wdrożenia i związanych z tym kosztów. Możliwość szybszego wdrożenia rozwiązania skutkuje szybszym uzyskaniem zwrotu z inwestycji.
Logowanie do naszych aplikacji zabezpieczone jest na wysokim poziomie, charakterystycznym dla rozwiązań bankowych. Jednocześnie proces logowania jest intuicyjny. Twoje dane są dzięki naszemu systemowi bezpieczne jak w banku.
Oferujemy wielojęzyczność naszych rozwiązań poprzez zastosowanie tłumaczenia „w locie” — każdy pracownik obsługuje aplikacje w swoim ojczystym języku. Wpływa to na zwiększenie efektywności oraz obniżenie kosztów dzięki zwiększeniu potencjalnego rynku pozyskania pracowników, oraz braku konieczności zatrudniania tłumaczy.
Nasze oprogramowanie posiada interfejs zoptymalizowany pod kątem szybkiej, łatwej, intuicyjnej obsługi, nawet przez słabo wykwalifikowanego i wykluczonego cyfrowo pracownika. Oznacza to dla Ciebie realną oszczędność czasu i kosztów szkolenia pracowników w zakresie korzystania z nowego oprogramowania. Możliwość szybkiego wdrożenia oprogramowania do użycia — krótszy okres przejścia/wdrożenia.
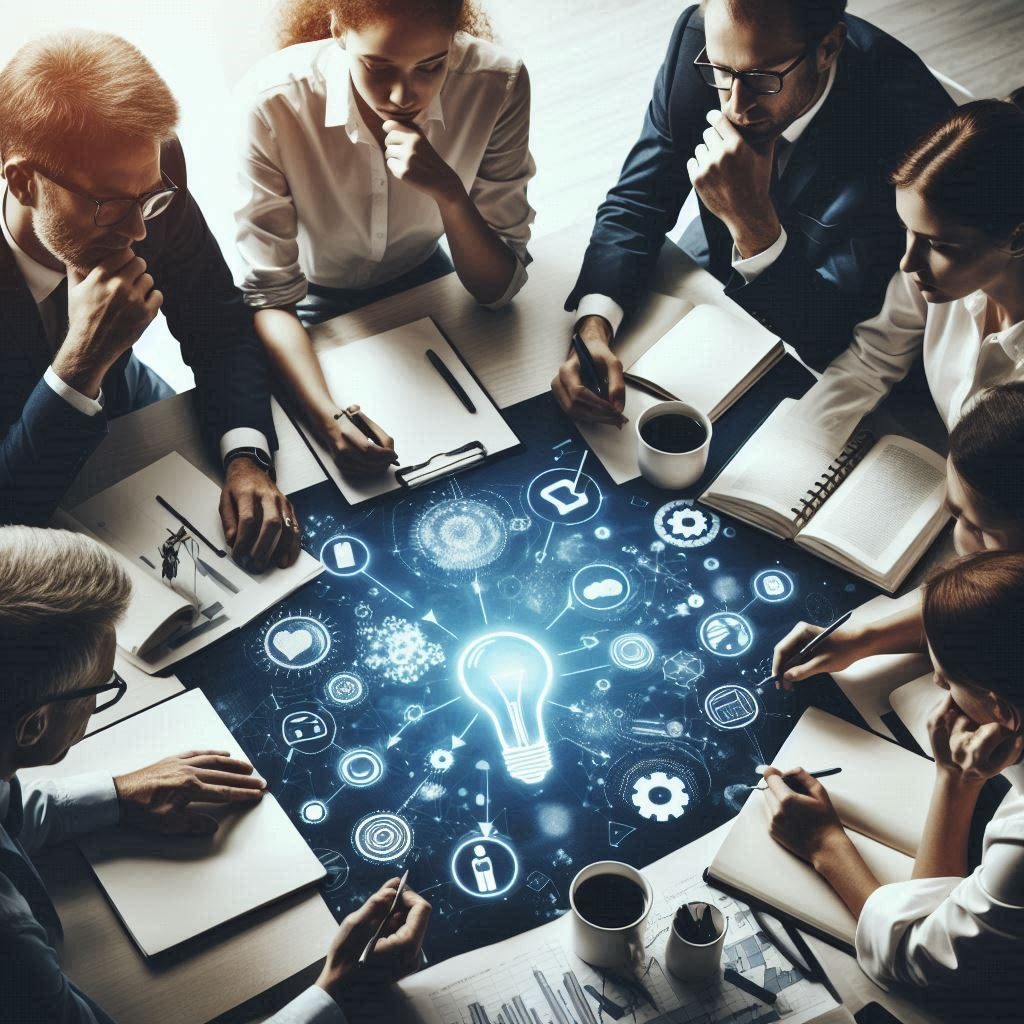