Ciągłe doskonalenie, znane także pod japońską nazwą „Kaizen”, oznacza proces stałego ulepszania działań na wszystkich poziomach organizacyjnych. Termin ten może być stosowany zarówno w kontekście osobistym, jak i profesjonalnym, obejmując szeroki zakres działań – od codziennych rutyn po kompleksowe procesy biznesowe. Ideą przewodnią jest przekonanie, że nawet najmniejsze, pozornie nieistotne zmiany mogą z czasem przynieść znaczące korzyści i ulepszenia.
Historia
Historia ciągłego doskonalenia sięga początków XX wieku, choć jej korzenie mogą być znacznie głębsze. Współcześnie kojarzona jest przede wszystkim z japońskim przemysłem i filozofią zarządzania po drugiej wojnie światowej. Kaizen, jako formalna koncepcja, został spopularyzowany przez Masaaki Imaiego w latach 80. XX wieku, lecz idee podobne do ciągłego doskonalenia były stosowane już wcześniej, np. w ramach tzw. Lean Management (szczupłe zarządzanie), którego celem jest eliminacja wszelkich form marnotrawstwa.
Zastosowania
Ciągłe doskonalenie ma kluczowe znaczenie nie tylko w produkcji i zarządzaniu. Jego zasady znajdują zastosowanie w edukacji, zdrowiu, administracji, a nawet w życiu osobistym każdego z nas. Na poziomie organizacji promuje kulturę otwartości, współpracy i ciągłej nauki, co przekłada się na zwiększenie efektywności, redukcję kosztów i poprawę jakości pracy. W życiu osobistym zasady ciągłego doskonalenia mogą pomóc w osiąganiu celów, rozwijaniu nowych umiejętności i lepszym zarządzaniu czasem.
Zwróć uwagę!
Ciągłe doskonalenie jest więc nie tylko strategią biznesową, ale także filozofią życiową, która zachęca do stałej refleksji nad własnymi działaniami i poszukiwania dróg do ich optymalizacji. W erze szybkich zmian technologicznych i ciągłej konkurencji, zdolność do adaptacji i ulepszania istniejących procesów stała się kluczową kompetencją, zarówno dla jednostek, jak i dla organizacji.
Podstawowe zasady ciągłego doskonalenia
Ciągłe doskonalenie opiera się na kilku fundamentalnych zasadach, które mogą być stosowane w różnych kontekstach – od osobistego rozwoju po skomplikowane procesy produkcyjne w dużych organizacjach. Oto przegląd najważniejszych z nich:
Niekończąca się iteracja
Podstawą ciągłego doskonalenia jest przekonanie, że zawsze istnieje możliwość ulepszenia. Proces ten nie ma końca i odbywa się poprzez ciągłe iteracje, gdzie każda kolejna próba ma na celu przewyższenie poprzedniej. W produkcji, iteracyjne podejście może oznaczać regularne przeglądy linii montażowych w celu identyfikacji obszarów do optymalizacji.
Małe zmiany
W przeciwieństwie do radykalnych innowacji, ciągłe doskonalenie skupia się na małych, stopniowych zmianach, które są łatwiejsze do zaimplementowania i wiążą się z mniejszym ryzykiem. W kontekście produkcji, mogą to być drobne modyfikacje w procesach lub niewielkie zmiany w organizacji pracy, które razem przyczyniają się do znaczących ulepszeń.
Zaangażowanie wszystkich poziomów organizacji
Ciągłe doskonalenie wymaga zaangażowania wszystkich pracowników, od kadry zarządzającej po pracowników linii produkcyjnej. Każdy ma unikalną wiedzę na temat swojej pracy, co oznacza, że pomysły na ulepszenia mogą pochodzić z różnych poziomów. Promowanie kultury otwartości, gdzie każdy może przedstawić swoje sugestie, jest kluczowe.
Zastosowanie w produkcji
Niekończąca się iteracja
W produkcji, niekończąca się iteracja może przyjąć formę ciągłego monitorowania i oceny wydajności maszyn oraz efektywności procesów produkcyjnych. Dzięki regularnej analizie danych, możliwe jest szybkie identyfikowanie obszarów wymagających uwagi i wprowadzanie niezbędnych zmian.
Małe zmiany
Zastosowanie zasady małych zmian w produkcji może objawiać się poprzez implementację prostych ulepszeń w organizacji pracy, takich jak zmiana układu narzędzi, co ułatwia dostęp i skraca czas pracy. Takie zmiany są często niskokosztowe, ale mogą znacząco wpłynąć na poprawę produktywności i jakości.
Zaangażowanie wszystkich poziomów organizacji
W produkcji, zaangażowanie pracowników na wszystkich poziomach może przybrać formę regularnych spotkań zespołowych, na których pracownicy mogą dzielić się obserwacjami i sugestiami dotyczącymi ulepszeń. Tworzenie przestrzeni dla otwartej komunikacji i uznawanie wkładu pracowników w proces doskonalenia motywuje do aktywnego uczestnictwa i innowacyjności. Można też wykorzystać do tego specjalistyczne narzędzie Cluer.
Zwróć uwagę!
Implementacja tych zasad ciągłego doskonalenia w procesach produkcyjnych może prowadzić do znaczących korzyści, w tym do redukcji marnotrawstwa, poprawy jakości produktów, zwiększenia wydajności oraz zwiększenia satysfakcji i zaangażowania pracowników. Kluczem do sukcesu jest jednak systematyczność i otwartość na zmiany na wszystkich poziomach organizacji.
Proces ciągłego doskonalenia
Proces ciągłego doskonalenia, choć wydaje się złożony, w rzeczywistości opiera się na prostym i iteracyjnym podejściu, które można zastosować w różnych dziedzinach i na różnych poziomach działalności. Centralnym elementem tego procesu jest cykl PDCA (Planuj – Rób – Sprawdzaj – Działaj), który pomaga w systematycznym podejściu do wprowadzania i utrwalania zmian.
1: Planuj (Plan)
Pierwszym krokiem jest zidentyfikowanie obszaru wymagającego ulepszenia oraz ustalenie celów. W tej fazie zbiera się dane, analizuje procesy i planuje działania, które mają na celu wprowadzenie zmian.
2: Rób (Do)
Wdraża się zaplanowane działania na mniejszą skalę, w kontrolowanych warunkach, aby zminimalizować ryzyko i lepiej ocenić efekty.
3: Sprawdzaj (Check)
Po wdrożeniu zmian przeprowadza się analizę efektów, porównując wyniki z oczekiwaniami i celami określonymi w fazie planowania. Jest to kluczowy moment na ocenę, czy zmiany przyniosły pożądane rezultaty.
4: Działaj (Act)
Na podstawie wyników analizy podejmuje się decyzję o dalszych działaniach. Jeśli eksperyment się powiódł, zmiany są implementowane na większą skalę. W przypadku wyników niesatysfakcjonujących, proces wraca do fazy planowania, aby zidentyfikować nowe możliwości ulepszeń.
Narzędzia i metodyki wspierające proces
- PDCA – Jak już wspomniano, cykl PDCA stanowi podstawę procesu ciągłego doskonalenia, zapewniając strukturę dla systematycznych zmian i ulepszeń.
- 5S – Metodyka 5S (Sortuj, Systematyzuj, Sprzątaj, Standaryzuj, Utrzymuj dyscyplinę) jest szczególnie przydatna w organizowaniu przestrzeni roboczej i procesów produkcyjnych, co bezpośrednio przekłada się na wydajność i jakość pracy.
- Six Sigma – Metodyka Six Sigma skupia się na redukcji zmienności w procesach produkcyjnych i biznesowych, dążąc do minimalizacji błędów i marnotrawstwa, co jest osiągane poprzez szczegółową analizę danych i procesów.
Integracja ciągłego doskonalenia z codziennymi operacjami
Integracja ciągłego doskonalenia z codziennymi operacjami wymaga zaangażowania na wszystkich poziomach organizacji oraz adaptacji kultury organizacyjnej, która promuje innowacyjność, otwartość na zmiany i ciągłe uczenie się. Ważne jest, aby proces ciągłego doskonalenia nie był postrzegany jako dodatkowe obciążenie, ale jako integralna część codziennej pracy, która przyczynia się do lepszego funkcjonowania organizacji i satysfakcji pracowników. W praktyce oznacza to regularne szkolenia, otwartość na sugestie zmian od wszystkich pracowników, a także włączenie zasad ciągłego doskonalenia do standardowych procedur operacyjnych.
Praktyczne strategie wdrażania
- Rozpoczęcie od szkolenia pracowników – Zrozumienie filozofii i narzędzi ciągłego doskonalenia jest fundamentem dla wszystkich pracowników.
- Ustalenie klarownych celów – Jasno określone cele pomagają w skoncentrowaniu wysiłków i śledzeniu postępów.
- Stworzenie kultury otwartości na zmiany – Promowanie kultury, w której każdy pracownik czuje się odpowiedzialny i upoważniony do zgłaszania propozycji ulepszeń.
- Wykorzystanie narzędzi i metodyk do monitorowania i analizy – Regularne stosowanie PDCA, 5S, i Six Sigma do oceny efektywności procesów i wprowadzania potrzebnych korekt.
- Zachęcanie do współpracy między działami – Integracja zespołów z różnych działów w celu wymiany wiedzy i doświadczeń.
- Utrzymywanie motywacji – Regularne uznawanie i nagradzanie pracowników za ich wkład w proces doskonalenia.
- Ewaluacja i dostosowywanie strategii – Stałe przeglądy strategii wdrażania ciągłego doskonalenia w celu dostosowania do zmieniających się warunków i osiągnięć.
Wdrażanie ciągłego doskonalenia w firmach produkcyjnych jest procesem wymagającym zaangażowania na wszystkich poziomach organizacji. Sukces zależy od jasnej wizji, skutecznej komunikacji, ciągłego szkolenia i zaangażowania pracowników. Przyjęcie tych zasad może przynieść znaczące korzyści, w tym zwiększenie wydajności, poprawę jakości produktów i usług, a także budowanie silniejszej, bardziej zintegrowanej kultury organizacyjnej.
Wyzwania i przeszkody
Wprowadzanie ciągłego doskonalenia w firmach produkcyjnych, mimo swoich licznych korzyści, wiąże się z różnymi wyzwaniami i przeszkodami. Ich zrozumienie i skuteczne zarządzanie jest kluczowe dla utrzymania dynamiki procesu i osiągnięcia trwałych rezultatów.
Typowe wyzwania
- Odporność na zmiany – Pracownicy na różnych poziomach organizacji mogą być niechętni do zmian, zwłaszcza jeśli nie widzą bezpośrednich korzyści lub obawiają się dodatkowej pracy.
- Brak zrozumienia lub szkolenia – Niewystarczające szkolenie i brak zrozumienia celów i metod ciągłego doskonalenia mogą prowadzić do niskiego zaangażowania.
- Niewystarczające zasoby – Ograniczenia czasowe, finansowe lub brak odpowiednich narzędzi mogą hamować postępy.
- Niejasne cele – Brak jasno zdefiniowanych, mierzalnych celów może prowadzić do rozproszenia wysiłków i nieskutecznych działań.
- Słaba komunikacja – Nieefektywna komunikacja między zespołami i poziomami zarządzania może prowadzić do nieporozumień i braku koordynacji.
Przypadki, w których ciągłe doskonalenie może nie przynieść oczekiwanych rezultatów
- Nierealistyczne oczekiwania – Spodziewanie się zbyt szybkich lub zbyt dużych rezultatów może prowadzić do frustracji i rezygnacji z procesu.
- Ignorowanie kultury organizacyjnej – Nieuwzględnienie istniejącej kultury organizacyjnej i wartości pracowników może prowadzić do oporu i sabotowania inicjatyw.
- Brak wsparcia kierownictwa – Brak aktywnego wsparcia i zaangażowania ze strony kierownictwa może osłabić wysiłki zespołu i ograniczyć zasoby.
Jak pokonać przeszkody i utrzymać postępy
- Budowanie kultury otwartej na zmiany. Wdrażanie kultury, która celebruje innowacje i jest otwarta na zmiany, jest kluczowe. Ważne jest również regularne szkolenie pracowników i zapewnienie im dostępu do niezbędnych zasobów.
- Zarządzanie oczekiwaniami. Ustalanie realistycznych celów i harmonogramów oraz regularne informowanie o postępach i sukcesach pomaga w utrzymaniu motywacji.
- Angażowanie pracowników. Włączenie pracowników na wszystkich poziomach w proces decyzyjny i zachęcanie do udziału w proponowaniu zmian zwiększa ich zaangażowanie i poczucie własności.
- Silne przywództwo. Aktywne wsparcie ze strony kierownictwa, zarówno słowne, jak i poprzez alokację zasobów, jest niezbędne do pokonania oporu i utrzymania pędu.
- Komunikacja i współpraca. Poprawa komunikacji wewnątrz organizacji i współpraca między działami pomagają w przezwyciężaniu barier i skutecznym realizowaniu celów.
Pokonywanie wyzwań związanych z ciągłym doskonaleniem wymaga cierpliwości, wytrwałości i elastyczności. Kluczowe jest, aby pamiętać, że proces ten jest maratonem, a nie sprintem, i wymaga ciągłego zaangażowania oraz gotowości do adaptacji i uczenia
Przykład udanego wdrażania ciągłego doskonalenia u producenta komponentów samochodowych
Kontekst
Uznany producent komponentów samochodowych, zauważyła spadek wydajności na jednej ze swoich kluczowych linii produkcyjnych. Pomimo stosowania nowoczesnych technologii i posiadania wykwalifikowanego personelu, występowały problemy z jakością produktów i nieefektywnością procesów.
Wprowadzone zmiany
- Firma zdecydowała się na wdrożenie programu ciągłego doskonalenia, opierając się na metodologii Lean i narzędziach takich jak 5S i Kaizen. Program rozpoczął się od serii warsztatów edukacyjnych dla pracowników na wszystkich poziomach, mających na celu podniesienie świadomości na temat zasad ciągłego doskonalenia i korzyści z niego płynących.
- Następnie zespoły multidyscyplinarne składające się z pracowników różnych działów, w tym produkcji, jakości i utrzymania ruchu, rozpoczęły regularne spotkania, aby identyfikować obszary wymagające poprawy i proponować rozwiązania. Zastosowano narzędzie PDCA (Planuj – Rób – Sprawdzaj – Działaj) do planowania, testowania i wdrażania zmian, a postępy były monitorowane za pomocą wskaźników KPI (Key Performance Indicators).
Wyniki
W ciągu pierwszego roku od wdrożenia programu, firma odnotowała znaczące ulepszenia w kluczowych obszarach:
- Zwiększenie wydajności linii produkcyjnej o 20% dzięki eliminacji marnotrawstwa i optymalizacji procesów.
- Poprawa jakości produktów, co przełożyło się na 30% redukcję reklamacji od klientów.
- Zwiększenie zaangażowania pracowników i poprawa komunikacji między działami.
Analiza sukcesu
Najważniejszymi czynnikami sukcesu były: zaangażowanie kadry zarządzającej, intensywne szkolenia pracowników, skuteczna komunikacja w całej organizacji oraz systematyczne podejście do identyfikacji i rozwiązywania problemów. Firma potwierdziła, że ciągłe doskonalenie stało się integralną częścią jej kultury organizacyjnej, co pozwala na ciągłe ulepszanie procesów i podnoszenie konkurencyjności na rynku.
Lekcje z case study
Przypadek wspomnianej firmy pokazuje, że skuteczne wdrożenie ciągłego doskonalenia wymaga więcej niż tylko zastosowania narzędzi i technik; kluczowe jest budowanie kultury otwartej na zmiany, promowanie współpracy między działami oraz zaangażowanie i wsparcie na wszystkich poziomach organizacji. Pokazuje również, że systematyczne podejście do problemów i ich rozwiązywanie może prowadzić do znaczących ulepszeń w wydajności i jakości, przynosząc korzyści zarówno dla firmy, jak i jej klientów.
Narzędzia i zasoby
Dla firm produkcyjnych dążących do wdrożenia i utrzymania ciągłego doskonalenia, dostępne są różnorodne narzędzia i zasoby. Ich efektywne wykorzystanie może znacznie przyspieszyć procesy optymalizacji i podniesienia jakości.
Narzędzia wspierające ciągłe doskonalenie
Oprogramowanie
- Systemy zarządzania projektami (np. Trello, Asana, Jira) pomagają w organizacji zadań, terminów i współpracy między zespołami.
- Narzędzia do analizy procesów (np. Minitab, JMP) ułatwiają gromadzenie danych, ich analizę statystyczną i wizualizację, co jest kluczowe w procesie identyfikacji obszarów do doskonalenia.
- Oprogramowanie do zarządzania jakością (np. MasterControl, TrackWise) wspiera procesy zapewnienia jakości i zarządzania niezgodnościami.
- Systemy zbierania sugestii pracowniczych (np. Cluer)
Szkolenia
- Szkolenia Lean Six Sigma oferują różne poziomy certyfikacji (Yellow Belt, Green Belt, Black Belt), kształcąc pracowników w zakresie metod i narzędzi optymalizacji procesów.
- Warsztaty Kaizen koncentrują się na praktycznym zastosowaniu zasad ciągłego doskonalenia w miejscu pracy. (np. https://cluer.eu/szkolenia-kaizen/ )
- Kursy online (np. na platformach Coursera, Udemy) zapewniają elastyczny dostęp do wiedzy na temat ciągłego doskonalenia z możliwością dostosowania tempa nauki do indywidualnych potrzeb.
Książki
- „Kaizen: Klucz do konkurencyjnego sukcesu Japonii” autorstwa Masaaki Imaiego jest klasyką, wprowadzającą w świat japońskich metod zarządzania i doskonalenia procesów.
- „The Toyota Way” autorstwa Jeffrey K. Liker opisuje 14 zasad zarządzania w Toyota, które stanowią fundament filozofii Lean.
- „Lean Six Sigma For Dummies” autorstwa Johna Morgan i Martina Brenig-Jones to przystępne wprowadzenie do metodologii Lean Six Sigma, kierowane do szerokiego grona odbiorców.
Zasoby online i miejsca, gdzie można znaleźć więcej informacji
Fora i społeczności internetowe
- LinkedIn Groups, takie jak Lean Six Sigma czy Continuous Improvement, są platformami do wymiany doświadczeń i najlepszych praktyk.
- Reddit posiada subreddity poświęcone Lean, Six Sigma i ciągłemu doskonaleniu, gdzie użytkownicy dzielą się radami i zasobami.
Strony internetowe i blogi
- iSixSigma.com oferuje artykuły, case studies i forum dyskusyjne poświęcone różnym aspektom metodologii Six Sigma.
- LeanEnterpriseInstitute.org dostarcza zasobów na temat wdrażania Lean w organizacjach, w tym szkoleń, książek i studiów przypadku.
- ASQ.org (American Society for Quality) jest bogatym źródłem wiedzy na temat zarządzania jakością, oferując artykuły, webinaria i szkolenia.
Korzystając z tych narzędzi i zasobów, firmy produkcyjne mogą nie tylko skuteczniej wdrażać ciągłe doskonalenie, ale również inspirować pracowników do innowacji i dążenia do doskonałości w każdym aspekcie działalności.
Przyszłość ciągłego doskonalenia
Ciągłe doskonalenie, będące już fundamentalną częścią strategii wielu organizacji, nadal będzie ewoluować, dostosowując się do zmieniającego się świata i nowych technologii. W przyszłości możemy oczekiwać, że te procesy staną się jeszcze bardziej zintegrowane z codziennymi operacjami firm, a także będą coraz bardziej wspierane przez nowoczesne technologie.
Jak ciągłe doskonalenie może ewoluować w przyszłości
- Większe skupienie na danych i analityce. W miarę jak firmy będą coraz bardziej cyfryzować swoje operacje, dane staną się jeszcze bardziej kluczowym elementem ciągłego doskonalenia. Analityka zaawansowana i uczenie maszynowe mogą dostarczać głębszych wglądów w procesy, umożliwiając bardziej skuteczne identyfikowanie obszarów wymagających ulepszeń.
- Personalizacja doświadczeń pracowniczych. Rozwój technologii pozwoli na bardziej spersonalizowane podejście do szkolenia i rozwoju pracowników, co jest kluczowe dla utrzymania ich zaangażowania i innowacyjności. Narzędzia VR (wirtualna rzeczywistość) mogą na przykład umożliwić symulacje i treningi w bardziej interaktywny sposób.
- Zwiększona integracja z zrównoważonym rozwojem. Ciągłe doskonalenie będzie coraz bardziej uwzględniać aspekty ekologiczne i zrównoważony rozwój. Fokus na redukcję marnotrawstwa i efektywność energetyczną stanie się standardem, nie tylko ze względów etycznych, ale również ekonomicznych.
Potencjalne nowe kierunki i technologie wspierające ciągłe doskonalenie
- Internet Rzeczy (IoT) i inteligentne fabryki. Urządzenia IoT mogą dostarczać real-time danych dotyczących procesów produkcyjnych, umożliwiając natychmiastowe wykrywanie i rozwiązywanie problemów. Inteligentne fabryki, wykorzystujące IoT, sztuczną inteligencję i robotykę, będą mogły samodzielnie optymalizować procesy w czasie rzeczywistym.
- Sztuczna inteligencja i uczenie maszynowe. Te technologie mogą automatycznie analizować ogromne ilości danych operacyjnych, identyfikując wzorce i przewidując potencjalne problemy zanim wystąpią. Dzięki temu możliwe będzie jeszcze szybsze i dokładniejsze wprowadzanie ulepszeń.
- Blockchain. Technologia ta ma potencjał do zwiększenia przejrzystości i śledzenia w łańcuchach dostaw. W kontekście ciągłego doskonalenia, blockchain może pomóc w lepszym monitorowaniu i zarządzaniu jakością produktów oraz w efektywniejszym współdziałaniu z partnerami biznesowymi.
- Cyfrowe bliźniaki. Cyfrowe repliki fizycznych systemów produkcyjnych mogą umożliwić testowanie zmian w bezpiecznym, wirtualnym środowisku. To pozwoli na eksperymentowanie z różnymi scenariuszami i optymalizacje bez ryzyka zakłócenia rzeczywistych procesów.
W miarę jak świat staje się coraz bardziej połączony i cyfrowy, ciągłe doskonalenie będzie odgrywać jeszcze większą rolę w utrzymaniu konkurencyjności i innowacyjności firm. Integracja nowych technologii i podejść, takich jak personalizacja, zrównoważony rozwój, i wykorzystanie zaawansowanej analityki, będzie kluczowa dla przyszłego sukcesu w ciągłym doskonaleniu.
Ciągłe doskonalenie
Pobierz arkusz Excel - Określaj cele, sprawdzaj status!
Zachęcamy do wykorzystania szablonu Excela do planowania i monitorowania ciągłego doskonalenia w Twojej firmie! To narzędzie ułatwi śledzenie postępów projektów, zapewni lepszą organizację i pozwoli zaangażować wszystkich członków zespołu. Pobierz plik i zobacz, jak może on usprawnić Twoje procesy produkcyjne oraz podnieść efektywność operacyjną.
Może Cię także zainteresować
Systemy IT dla produkcji
Z jakim wyzwaniem chciałbyś się zmierzyć?
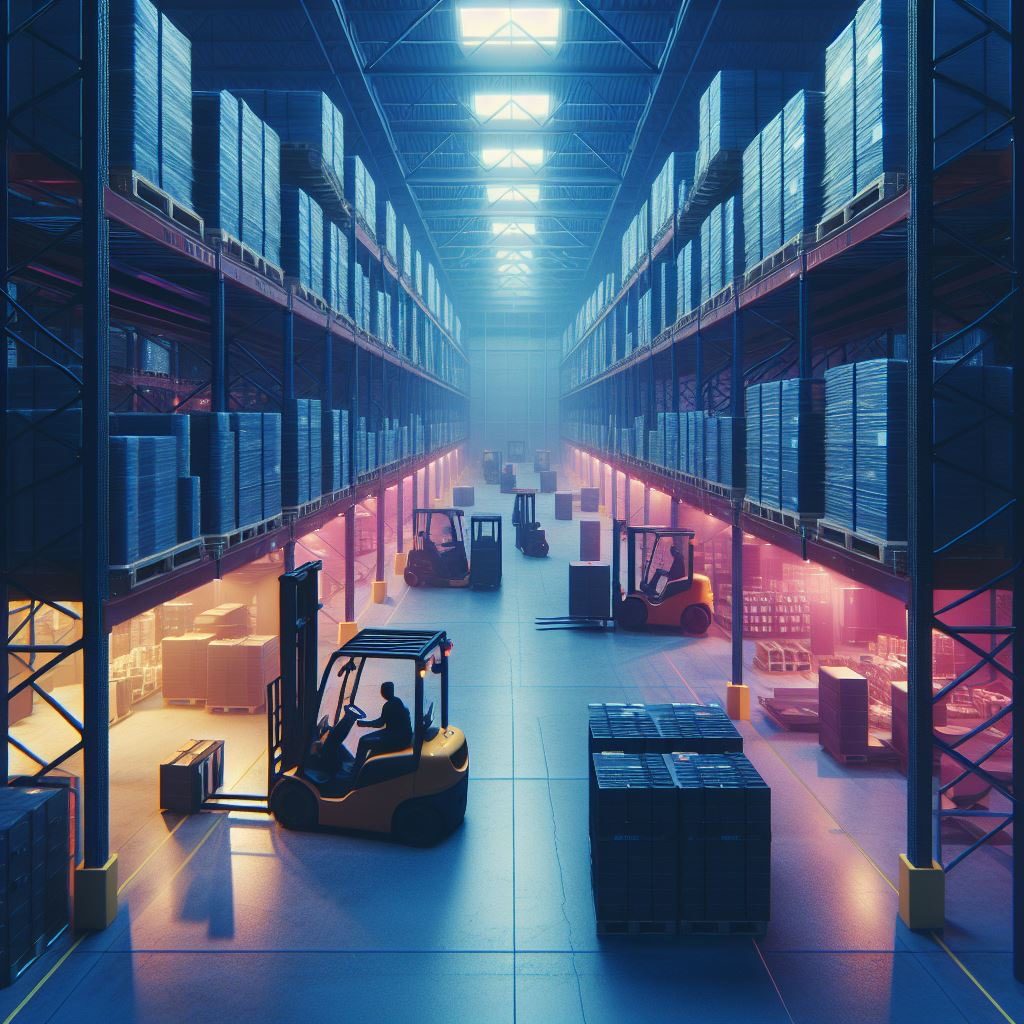
- Optymalizacja logistyki wewnętrznej
- Przywołania gniazd produkcyjnych
- Komunikaty z maszyn
- Wysokie koszty żużycia prądu, wody lub gazu
- Zarządzanie umiejętnościami pracowników
- Usprawnienie produkcji
- Zarzadzanie i kontrola dystybucji narzędzi
- Zbieranie sugestii pracowniczych (Kaizen, BHP, ESG)
- Instrukcje stanowiskowe / BHP na tablety
- Poprawa bezpieczeństwa
Wartości
Poznaj korzyści współpracy
Oferujemy darmową konsultację jako pierwszy krok współpracy, dzięki któremu możesz poznać nasz model działania oraz zweryfikować nasze kompetencje w zakresie doradztwa. Dzięki temu jeszcze przed podjęciem decyzji masz poczucie, że Twoja sytuacja i problem zostały dobrze zrozumiane oraz zaproponowane rozwiązanie będzie optymalnie pasować do sytuacji w Twoim przedsiębiorstwie.
Nasze usługi (wsparcie) są ujęte w abonamencie, co nie generuje kosztów ukrytych. Abonamentowa forma rozliczeń pozwala radykalnie obniżyć próg wejścia w system i od razu móc go testować.
Jesteśmy niezależni komunikacyjnie – potrafimy rozwinąć nasz system bez zależności od działu IT klienta. Nie generujemy dodatkowej pracy dla działu IT. Obniżamy w ten sposób ryzyko wdrożenia i związanych z tym kosztów. Możliwość szybszego wdrożenia rozwiązania skutkuje szybszym uzyskaniem zwrotu z inwestycji.
Logowanie do naszych aplikacji zabezpieczone jest na wysokim poziomie, charakterystycznym dla rozwiązań bankowych. Jednocześnie proces logowania jest intuicyjny. Twoje dane są dzięki naszemu systemowi bezpieczne jak w banku.
Oferujemy wielojęzyczność naszych rozwiązań poprzez zastosowanie tłumaczenia „w locie” — każdy pracownik obsługuje aplikacje w swoim ojczystym języku. Wpływa to na zwiększenie efektywności oraz obniżenie kosztów dzięki zwiększeniu potencjalnego rynku pozyskania pracowników, oraz braku konieczności zatrudniania tłumaczy.
Nasze oprogramowanie posiada interfejs zoptymalizowany pod kątem szybkiej, łatwej, intuicyjnej obsługi, nawet przez słabo wykwalifikowanego i wykluczonego cyfrowo pracownika. Oznacza to dla Ciebie realną oszczędność czasu i kosztów szkolenia pracowników w zakresie korzystania z nowego oprogramowania. Możliwość szybkiego wdrożenia oprogramowania do użycia — krótszy okres przejścia/wdrożenia.
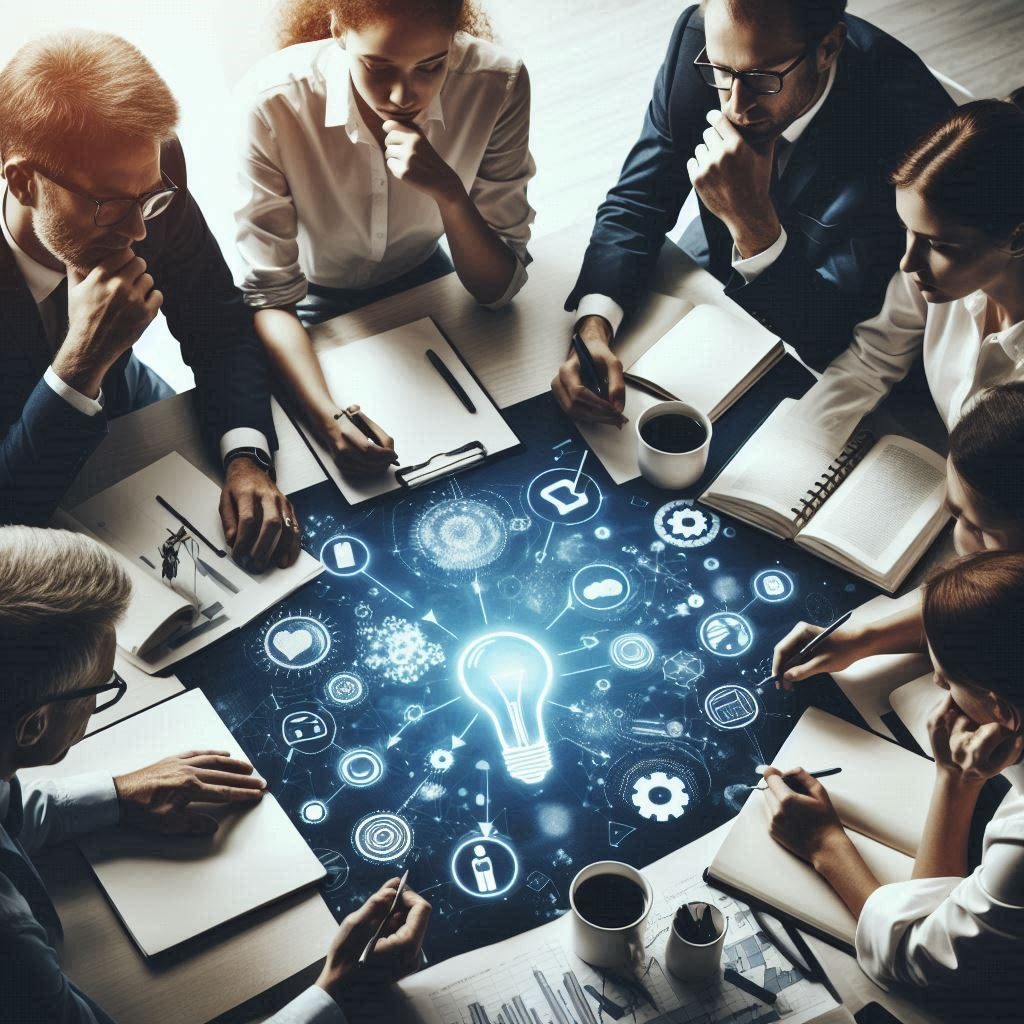
Współdzielenie know-how i doświadczenia w układaniu procesów
Za nami wiele wdrożeń w największych zakładach przemysłowych w Polsce i Europie. ( Zobacz Case Studies: ABB, Dayco,Tenneco ). Nasza skuteczna praca, pozytywne opinie Klientów oraz ogromne doświadczenie są gwarancją, że współpraca z nami pozwoli osiągnąć Twoje cele w zakresie redukcji kosztów, usprawnienia procesów, poprawy organizacji pracy, wydajniejszego wykorzystania istniejących zasobów, a w efekcie lepszego wyniku finansowego.
Doradzimy Ci jak skonfigurować system na bazie wcześniejszych doświadczeń oraz know-how. Podzielimy się nasza wiedzą i doświadczeniem zdobytym na bazie setek już zrealizowanych projektów w Polsce i zagranicą.
Nie czekaj aż konkurencja Cię wyprzedzi, skontaktuj się z nami. Bezpłatna konsultacja nie zobowiązuje, a pozwoli wyjaśnić jakie rozwiązania mogą skutecznie wpłynąć na usprawnienia w Twojej firmie. Zamów darmową konsultację. Zadzwonimy do Ciebie, aby przedstawić plan, jak razem zbudujemy Twój sukces!
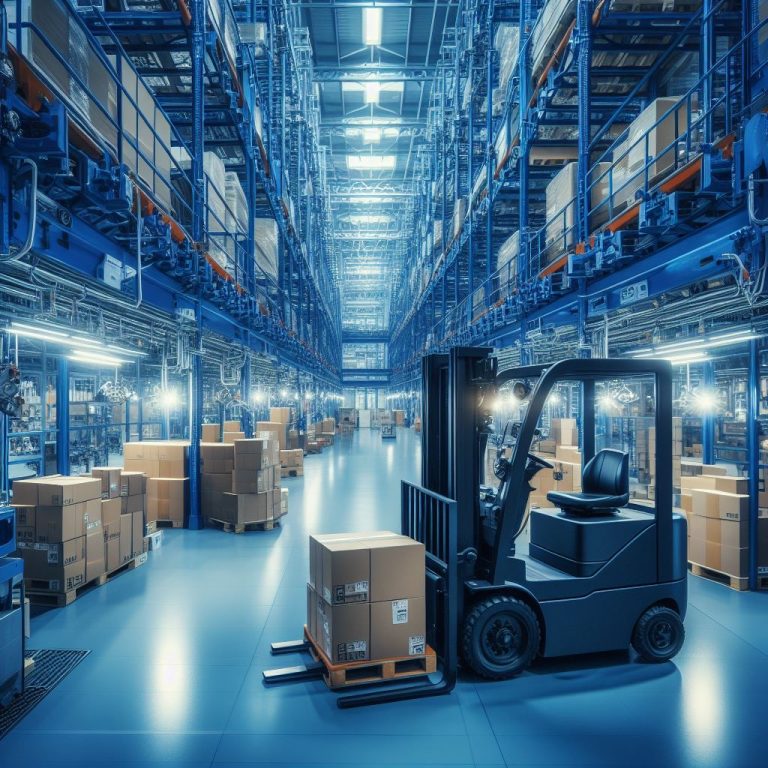
Pozwoli to na oszczędność czasu i pieniędzy, wynikającą z jak najbardziej efektywnego wykorzystania systemu oraz wypracowania nowych procesów w przedsiębiorstwie, które będą prowadzić do redukcji kosztów lub zwiększenia zysku.
Zaufały nam innowacyjne firmy z całego świata
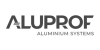
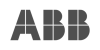
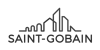
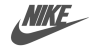
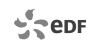
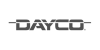
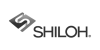
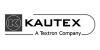
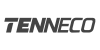
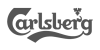
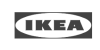