Indirect costs constitute a significant element of the cost structure of manufacturing firms. In contrast to direct costs, which can be unequivocally attributed to specific products, indirect costs are not directly related to the production of specific product units.
Definition
The definition of indirect costs encompasses all costs not directly related to production, such as administrative costs, office support costs, management costs, or infrastructure maintenance costs. These are costs that cannot be unambiguously assigned to a specific product but are necessary for the efficient functioning of the company as a whole.
Significance
The significance of indirect costs for manufacturing firms is enormous because they impact the efficiency and profitability of operations. Without proper control over indirect costs, a company may struggle to achieve profitability in the long term. Therefore, it is essential to monitor and analyze them carefully to make effective management decisions.
Types of Indirect Costs
Indirect costs are those costs that cannot be directly assigned to a specific product or service but are necessary for overall production. It is important to understand the various types of indirect costs to effectively manage and control company expenditures.
Indirect Costs Directly Related to Production
These include costs such as the electricity needed to operate machinery or personnel wages for operating the production line. These costs must be calculated and included in production costs to determine the correct selling prices.
Indirect Costs Related to Administration and Management
Another type of indirect costs pertains to administrative and management activities within the company. These may include salaries of office workers, accounting costs, or expenses on marketing and advertising. Although these costs are not directly related to production, they are necessary for the smooth functioning of the company and must be considered when calculating total operating costs.
Indirect Costs Related to Infrastructure Maintenance
These include costs such as building repairs or the purchase of modern machinery and equipment. While these costs may be difficult to predict, they are necessary to ensure production continuity and operational efficiency.
Methods of Allocating
Effective management of indirect costs is necessary for accurately determining production costs and establishing selling prices. There are several different methods of allocating indirect costs that can be used depending on the nature of the business.
Direct Costing Method
The direct costing method is one of the methods used to allocate indirect costs in manufacturing firms. It involves directly assigning indirect costs to specific products based on their consumption or usage. This method enables obtaining more precise information about production costs and determining the actual unit cost of a product.
The key benefits of using the direct costing method include:
Precise determination of unit costs
By directly assigning indirect costs to specific products, more reliable information about production costs can be obtained.
Facilitation of profitability analysis
It is possible to conduct profitability analysis of individual products and make decisions regarding further production.
Ability to react quickly to market changes
The flexibility of the direct costing method allows for rapid adaptation to changing market conditions and appropriate actions to be taken.
It is worth noting that despite its many advantages, the direct costing method also has some limitations, such as not considering all indirect costs or difficulties in determining non-direct costs. Therefore, it is worth considering the use of other methods of allocating indirect costs depending on the nature of the company’s activities.
Full Unit Cost Method
This method involves allocating all costs (both direct and indirect) to individual production units. As a result, we obtain the full unit cost, including both direct and indirect costs.
Steps for using the full unit cost method:
Identification of direct costs
It is essential to accurately determine the direct costs associated with the production of a specific product. These may include costs of raw materials, semi-finished products, or wages of employees directly involved in production.
Allocation of indirect costs
Next, indirect costs must be allocated to individual production units. This can be done by applying various allocation keys, such as the number of working hours, energy consumption, or the area occupied by production.
Calculation of full unit cost: By summing up direct and indirect costs for a given production unit, we obtain the full unit cost of the product. This is crucial information when making decisions regarding selling prices, inventory valuation, or profitability analysis of individual products.
Fixed and Variable Cost Method
This method involves dividing indirect costs into two categories: fixed costs and variable costs. Fixed costs are independent of production and do not change with the quantity of units produced. Examples of fixed costs include management salaries, administrative costs, or rents. Variable costs, on the other hand, are directly related to production and change with an increase or decrease in production. Examples of variable costs may include raw material costs, fuel costs, or packaging costs.
Assumption
This method assumes that indirect costs can be divided into two categories based on their behavior depending on changes in production. This allows for a more precise determination of unit costs and an analysis of the impact of production changes on total company costs.
Application of the Fixed and Variable Cost Method
The fixed and variable cost method is primarily used when indirect costs are difficult to unambiguously assign to specific production units. By dividing costs into fixed and variable, it is easier to monitor and control cost variability and make optimization decisions according to the company’s needs.
Additionally, this method allows for better management of risk associated with fluctuations in raw material prices or other factors affecting production costs. By tracking fixed and variable costs, companies can react more quickly to market changes and adjust their strategies to new conditions.
Activity-Based Costing Method
ABC is based on the assumption that indirect costs should be allocated based on the actual consumption of resources by individual activities or production operations, rather than just using traditional indicators such as the number of working hours or production units.
Description of the ABC Method
The ABC method focuses on identifying and analyzing all activities performed in the production process or service provision. Then, indirect costs are assigned to specific activities based on their resource consumption. Finally, these costs are allocated to specific products or services based on the actual contribution of each activity to the value creation process.
Significance of the ABC Method
Using the ABC method allows for a more precise determination of indirect costs associated with the production of a specific product or provision of a particular service. This makes cost management more efficient, and decisions regarding pricing, assortment, or investments are made based on reliable data. Furthermore, the ABC method enables the identification of activities and processes that generate the highest costs and facilitates actions aimed at their optimization.
Summary
Choosing the appropriate method for allocating indirect costs is crucial for effective financial management in manufacturing companies. Each of the mentioned methods has its advantages and limitations, so it is essential to carefully analyze the specifics of the company’s operations and cost management goals to choose the most suitable method.
Managing
Analysis
Indirect costs constitute a significant part of a company’s overall operating costs and can have a significant impact on its profitability. Therefore, it is necessary to regularly monitor and analyze these costs to identify areas where expenses can be effectively managed.
Process Optimization
To effectively manage indirect costs, it is also necessary to optimize processes within the company. This can be achieved by eliminating unnecessary production stages, reducing material waste, and streamlining internal operations. This can lead to cost reduction and increased operational efficiency of the company.
Control
Control is a crucial element of effective financial management in manufacturing companies. It is necessary to regularly check and analyze reports on indirect costs to monitor their level and identify any abnormalities. Proper control allows for quick response to changes and the implementation of appropriate corrective actions.
Decision-Making Based on Indirect Costs
Indirect costs provide valuable information that can be used to make strategic decisions in the company. Therefore, it is important for the financial director to interpret this data correctly and use it to plan the long-term development strategy of the company. Decisions regarding investments, plant expansion, or the introduction of new products should be based on a solid analysis to ensure optimal resource utilization and maximize profits.
Examples of Challenges Faced by Manufacturing Companies
Increasing Administrative Costs
As a manufacturing company grows, an increase in administrative costs becomes inevitable. Activities related to personnel management, accounting, customer service, and other aspects of office work generate additional costs that can significantly impact the profitability of the company. Therefore, continuous monitoring and optimization of these processes are necessary to maintain administrative costs at an appropriate level.
Need for Investment in New Technologies
In today’s world, technological development plays a crucial role in the manufacturing industry. Companies that do not invest in modern technologies can easily be pushed to the sidelines of the market. However, the introduction of new technologies entails high investment costs, which can be difficult to cover, especially for smaller companies. Therefore, it is necessary to find a balance between investing in new technologies and maintaining the financial liquidity of the company.
Price Competitiveness vs. Marketing Costs
The contemporary market is extremely competitive, which means that manufacturing companies must constantly fight for their place. One of the key factors in positioning in the market is the price of the offered products. However, reducing prices to increase competitiveness can lead to a decrease in margins and limit investment opportunities. Therefore, effective management of marketing costs is essential to achieve an optimal balance between price competitiveness and company profitability.
Summary
Indirect costs play a crucial role in shaping the financial results of manufacturing companies. They often constitute a significant part of total operating costs and can have a significant impact on the profitability and competitiveness of companies. Analysis is essential for effective financial management and achieving business goals.
Recommendations for managing
Continuous control and monitoring
Regular analysis allows for identifying areas where savings can be made or processes optimized. Continuous tracking of costs enables quick response to deviations and implementation of appropriate corrective actions.
Identification and elimination of waste
Eliminating unnecessary indirect costs and reducing waste of time, energy, and resources can contribute to improving the profitability of the company. It is worth regularly analyzing processes and procedures to identify areas where waste occurs.
Optimization of resource utilization
Effective management also includes optimizing the use of company resources, such as employees, materials, or machinery. The financial director should analyze the effectiveness of resource utilization and take actions to optimize it.
In summary, effective management of indirect costs is one of the most important elements for achieving financial success in manufacturing companies. They not only affect financial results but also the competitiveness and market position of the company. Therefore, it is worth regularly monitoring , identifying areas where savings can be made, and optimizing resource utilization to increase profitability and efficiency of company operations.
Support from Signalo
Signalo supports manufacturing
companies by providing innovative IT solutions that help increase production efficiency.
Thanks to our tools, manufacturing companies reduce resource demand, resulting in savings and extending the life cycle of machines and equipment, as well as reducing the need for operator man-hours.
IT solutions provided by Signalo also allow for streamlining production processes, which translates into cost reduction and improvement in the company’s financial result.
An innovative approach to production management enables greater effectiveness and efficiency in your operations. We invite you to take advantage of a free consultation.
Instructions for conducting an audit of indirect costs PDF
Downloading the Instructions for Auditing Indirect Costs PDF – step by step, will help you increase efficiency and control over your company’s finances. With detailed instructions, you will be able to effectively conduct audits of indirect costs, allowing you to better manage your budget and minimize losses.
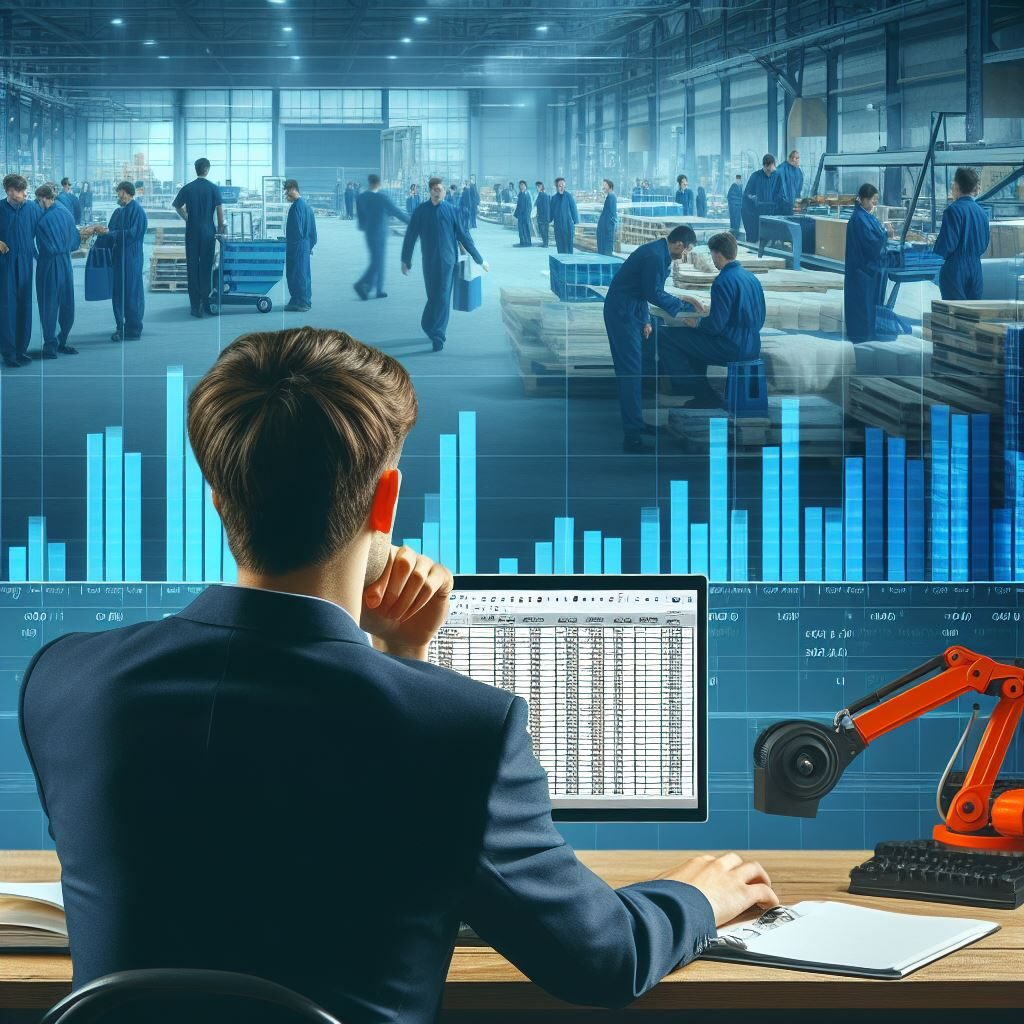
Values
Discover the benefits of collaboration
We offer a free consultation as the first step of collaboration, allowing you to familiarize yourself with our approach and verify our advisory competencies. This way, even before making a decision, you’ll feel that your situation and problem have been well understood, and the proposed solution will be optimally tailored to your company’s situation.
Our services (support) are included in a subscription, which does not generate hidden costs. The subscription-based billing allows for a significant reduction in the entry threshold into the system and enables immediate testing.
We are communicationally independent – we can develop our system without depending on the client’s IT department. We do not generate additional work for the client’s IT department. This way, we lower the implementation risk and associated costs. The possibility of quicker implementation of the solution results in faster return on investment.
Login to our applications is secured at a high level, characteristic of banking solutions. At the same time, the login process is intuitive. Your data is as secure as in a bank thanks to our system.
We offer multilingualism in our solutions through real-time translation—each employee operates applications in their native language. This enhances efficiency and reduces costs by expanding the potential labor market and eliminating the need to hire translators.
Our software features an interface optimized for quick, easy, and intuitive use, even by digitally excluded or poorly skilled employees. This means real-time savings in both time and training costs for your workforce in using the new software. The ability for rapid deployment of software for use results in a shorter transition/implementation period.
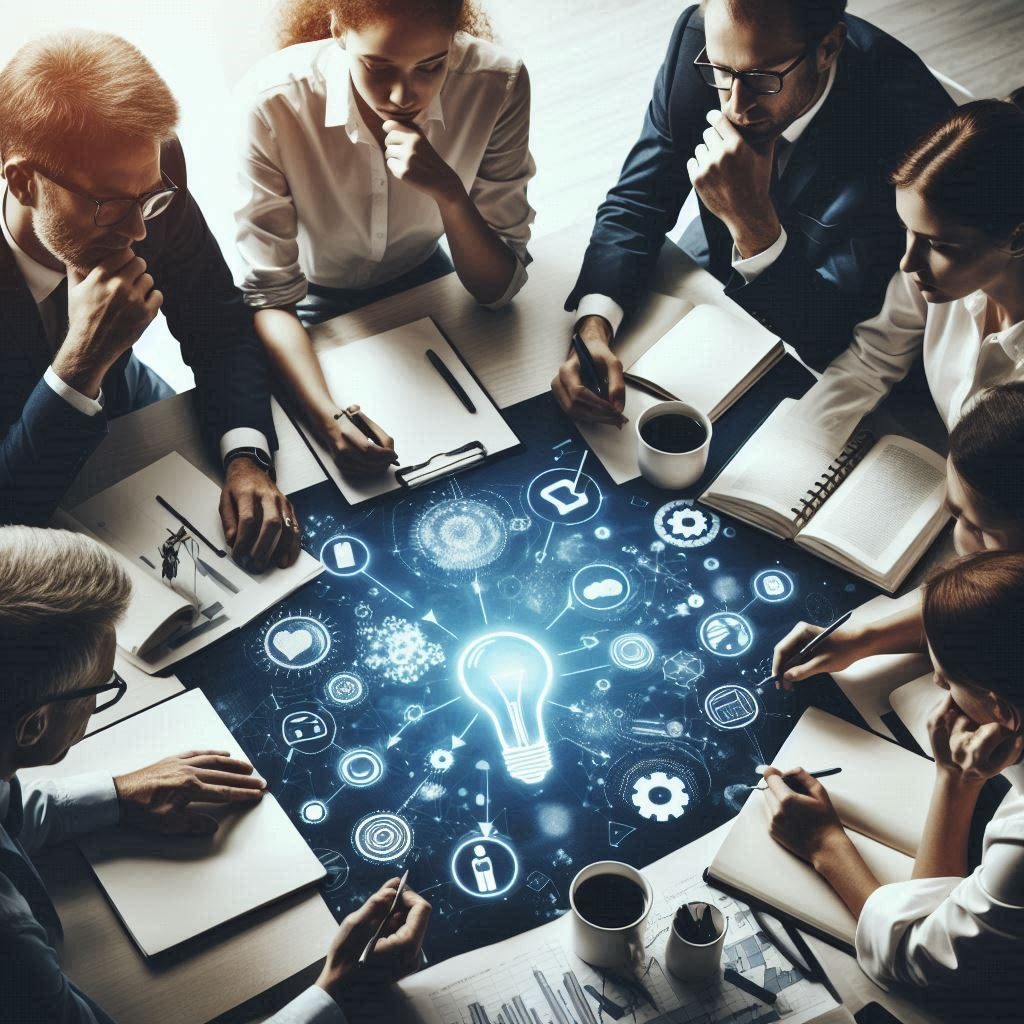