Have you ever wondered how to improve the efficiency of manufacturing processes? One useful tool could be a DFD (Data Flow Diagram). With it, processes can become more transparent, and managing them can become simpler. How exactly does the diagram work, and how can it be applied in production? Let’s find out!
What is a DFD?
A Data Flow Diagram is a graphical representation of the flow of information within a system. It consists of several elements:
- Processes – operations that process data.
- Data flows – streams of information between elements.
- Data stores – places where data is stored.
- External entities – external units that interact with the system.
Why is it worth using a DFD in production?
Clarity and understanding of processes
One of the biggest advantages of the diagram is its ability to visualize complex processes. In production, where many stages and operations need to be synchronized, understanding how data flows is crucial. By using a DFD, it’s easy to identify bottlenecks, inefficiencies, and potential improvements.
Facilitating communication
A Data Flow Diagram is a tool that facilitates communication between different departments within a company. Engineers, managers, and production line workers can use it to understand how various elements of the system operate. This significantly reduces the risk of misunderstandings and errors.
Identifying problems
Another benefit is the ability to quickly identify problems. If something isn’t working as it should, the diagram makes it easy to pinpoint the cause and location of the issue. This, in turn, leads to faster and more efficient repairs.
How to create a DFD for production processes?
☛ Step 1 – Gathering Information
Before you start drawing the diagram, you need to gather all the necessary information about the production processes. This includes talking to employees, observing operations, and analyzing existing documentation.
☛ Step 2 – Identifying Elements
Identify all the processes, data flows, data stores, and external entities. Make sure you have a complete picture of the system before moving on to creating the diagram.
☛ Step 3 – Drawing the Diagram
Start by drawing the external entities, which are outside the system. Then, add the processes, data flows, and data stores. Remember to use the appropriate symbols and maintain the clarity of the diagram.
☛ Step 4 – Validation and Verification
After creating the DFD, conduct a verification session with key stakeholders. Ensure that the diagram is accurate and complete, and that all involved parties understand its content.
Examples of DFD Applications in Production
Production Line Optimization
A sample automotive company used a DFD to optimize its production line. The diagram helped identify unnecessary steps and streamline the flow of information, resulting in a 15% increase in efficiency.
Inventory Management
Another example is a food industry company that used a diagram for inventory management. By analyzing the data flow, they reduced downtime and better organized deliveries. These actions significantly lowered storage costs.
DFD – Conclusions
A Data Flow Diagram is a powerful tool that can significantly impact the efficiency of production processes. With its ability to visualize and analyze the flow of information, it aids in problem identification, communication, and activity optimization. Regardless of the company’s size, it can be an effective tool for greatly improving its operations.
Download the Excel Data Flow Tracking Sheet
☛ This Excel sheet is a tool that will help you monitor data flow in real-time and quickly identify problems. With its clear layout, you can easily track each process, its source, destination, and status. Download it now to streamline data management in your company!
Manufacturing software
IT Systems
What challenge would you like to tackle?
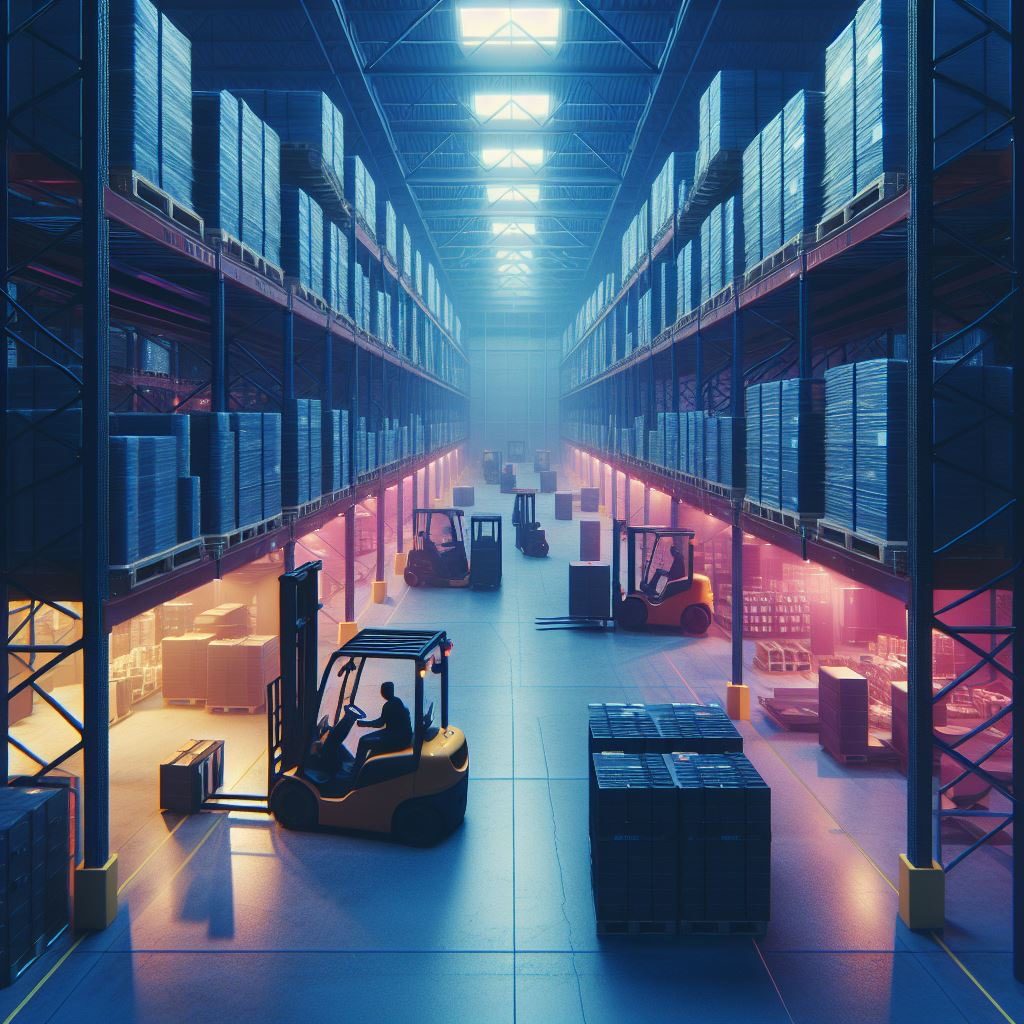
- Optimization of internal logistics
- Recalls of production sockets
- Messages from machines
- Monitoring electricity, water, gas, temperature, humidity, and vibrations
- Streamlining production
- Management and control of tool distribution
- Managing employee skills
- Collecting employee ideas for improvements
- Digital safety workplace instructions
- Improving safety
Values
Discover the benefits of collaboration
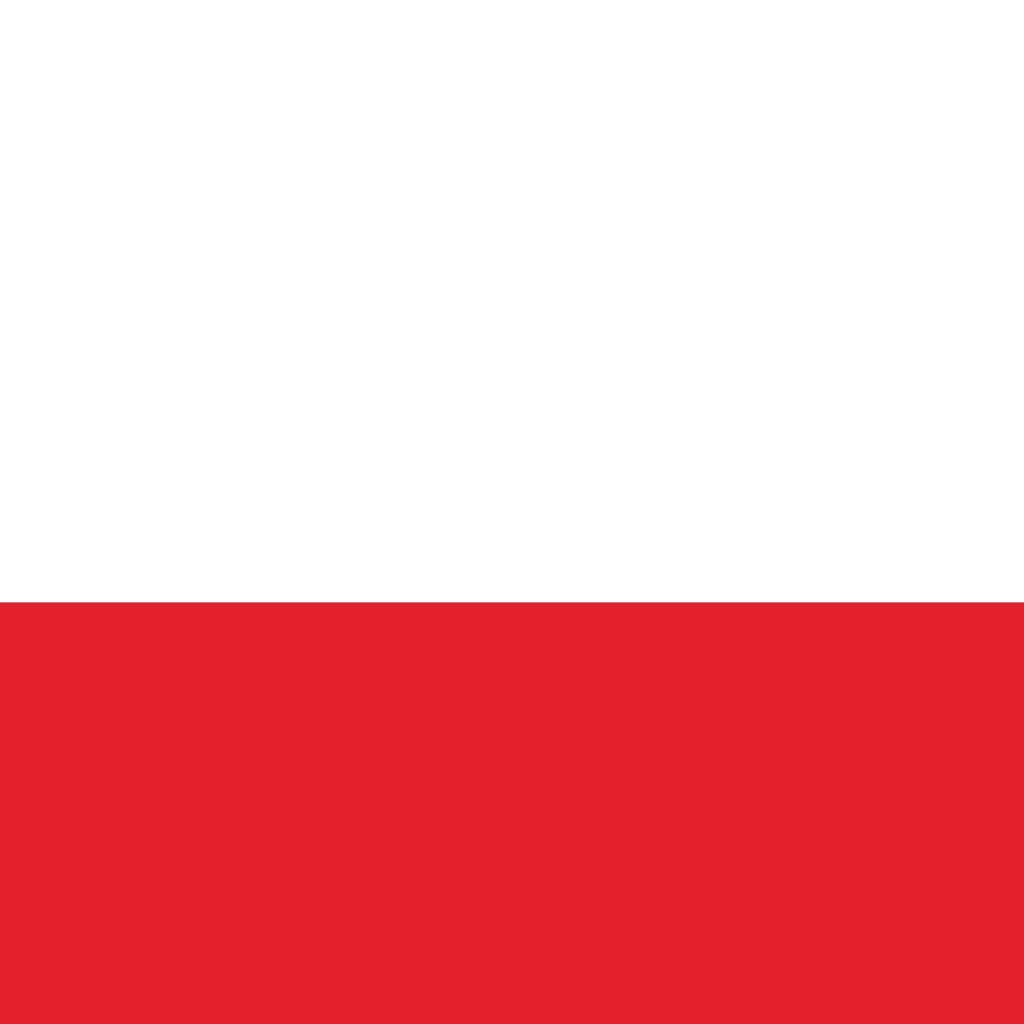
We offer a free consultation as the first step of collaboration, allowing you to familiarize yourself with our approach and verify our advisory competencies.
☛ This way, even before making a decision, you’ll feel that your situation and problem have been well understood, and the proposed solution will be optimally tailored to your company’s situation.
Our services (support) are included in a subscription, which does not generate hidden costs.
☛ The subscription-based billing allows for a significant reduction in the entry threshold into the system and enables immediate testing.
We are communicationally independent – we can develop our system without depending on the client’s IT department.
☛ We do not generate additional work for the client’s IT department. This way, we lower the implementation risk and associated costs.
The possibility of quicker implementation of the solution results in faster return on investment.
Login to our applications is secured at a high level, characteristic of banking solutions.
☛ At the same time, the login process is intuitive. Your data is as secure as in a bank thanks to our system.
We offer multilingualism in our solutions through real-time translation—each employee operates applications in their native language.
☛ This enhances efficiency and reduces costs by expanding the potential labor market and eliminating the need to hire translators.
Our software features an interface optimized for quick, easy, and intuitive use, even by digitally excluded or poorly skilled employees.
☛ This means real-time savings in both time and training costs for your workforce in using the new software.
The ability for rapid deployment of software for use results in a shorter transition/implementation period.
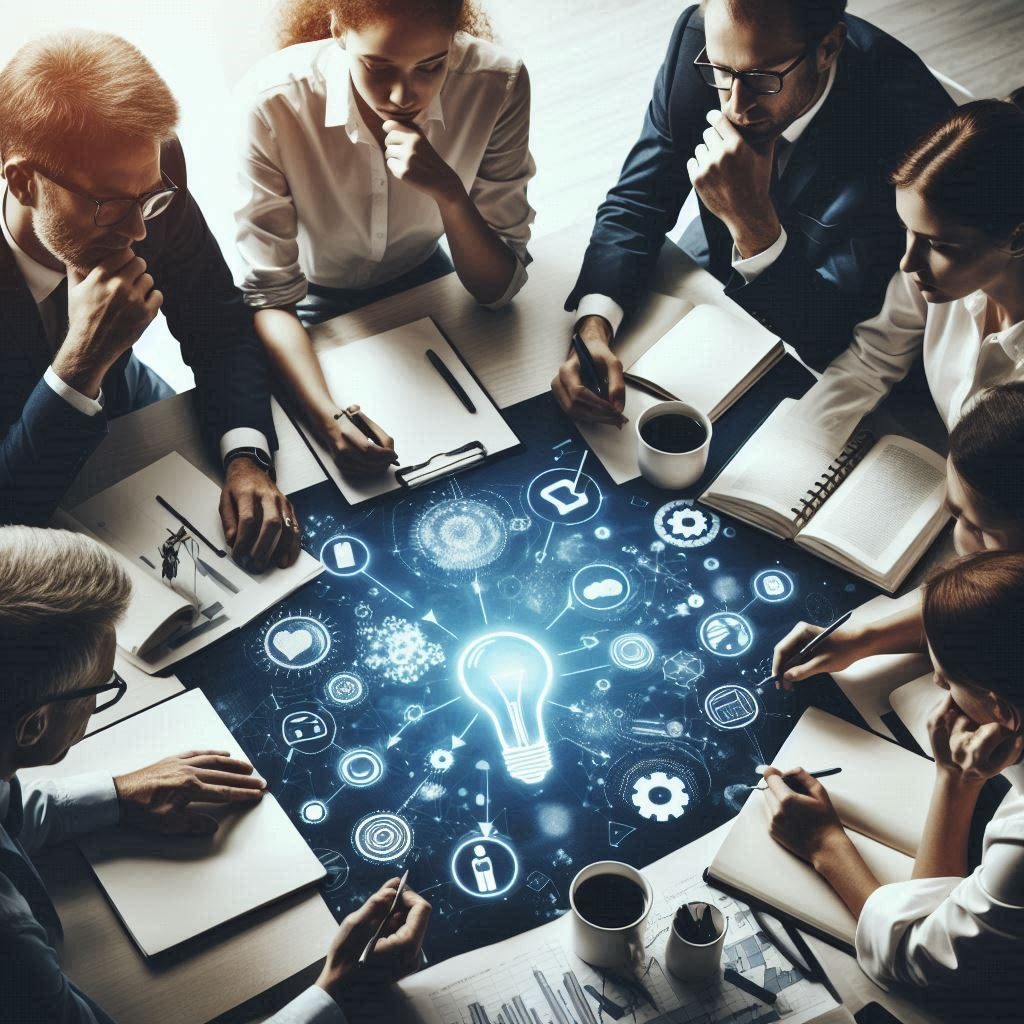
We have completed numerous implementations in the largest industrial plants around the world. (See Case Studies: ABB, Dayco, Tenneco, Aluprof).
☛ Our successful work, positive customer feedback, and extensive experience guarantee that cooperation with us will help you achieve your goals in terms of cost reduction, process improvement, workflow organization, more efficient use of existing resources, and ultimately better financial results.
We will advise you on how to configure the system based on our previous experiences and know-how. We will share our knowledge and experience gained from hundreds of completed projects.
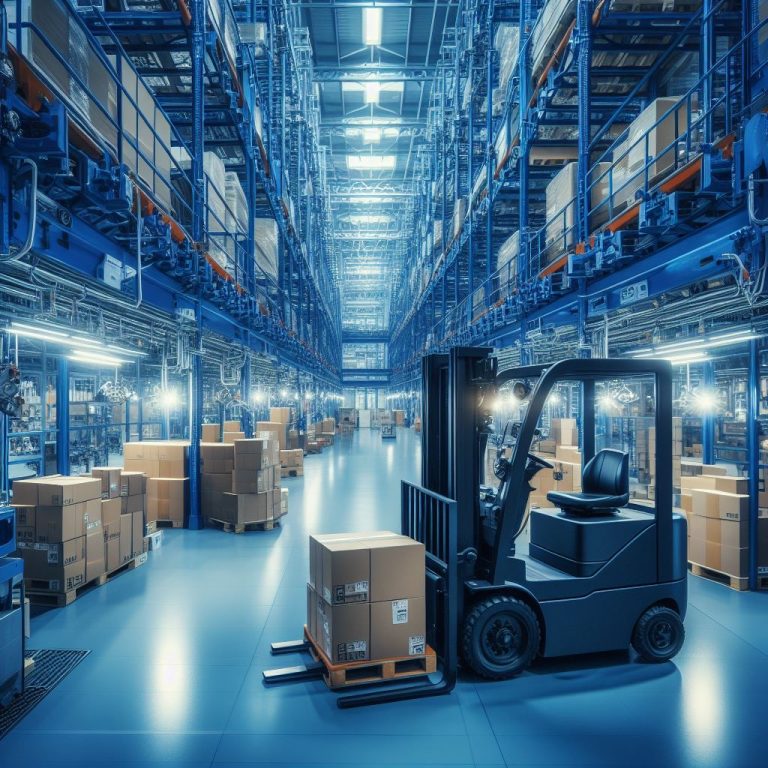
☛ Don’t wait for the competition to outpace you, contact us. A free consultation is non-binding and will help clarify what solutions can effectively improve your company. Order a free consultation. We will call you to present a plan on how to build your success together!
☛ Innovative companies from around the world have trusted us
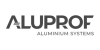
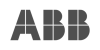
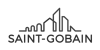
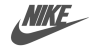
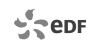
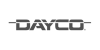
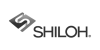
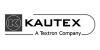
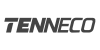
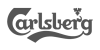
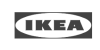